The Art of High-Quality Sand Casting
Sand casting is one of the oldest and most versatile metal casting processes in use today. Its historical significance can be traced back over 2,000 years, and it remains a fundamental method for producing metal components across various industries. High-quality sand casting is characterized by precision, durability, and a superior finish, making it an essential technique in manufacturing.
What is Sand Casting?
At its core, sand casting involves creating a mold from a mixture of sand, clay, and water. The sand mold is formed around a pattern, which is a replica of the object to be cast. Once the mold is prepared, molten metal is poured into it, allowed to cool, and solidified. Finally, the mold is broken away to reveal the finished casting. This method is lauded for its simplicity and effectiveness, but achieving high quality requires meticulous attention to detail.
The Importance of Quality in Sand Casting
High-quality sand casting is crucial for numerous applications, from automotive and aerospace components to intricate artistic pieces. A high-quality casting ensures the desired mechanical properties are met, including strength, ductility, and resistance to wear and corrosion. Defects such as sand inclusions, porosity, and dimensional inaccuracies can compromise the performance of the final product, leading to expensive failures and reworks. Therefore, a focus on quality is not merely advantageous but essential for safety, performance, and economic effectiveness.
Key Factors Affecting Sand Casting Quality
1. Sand Quality The choice of sand is pivotal in determining the success of the casting process. High-quality sand is usually fine and clean, with complementary properties that facilitate mold making and ensure minimal defects. Silica sand is the most common, but other types like zircon sand are also used for specific applications due to their superior thermal properties.
high quality sand casting
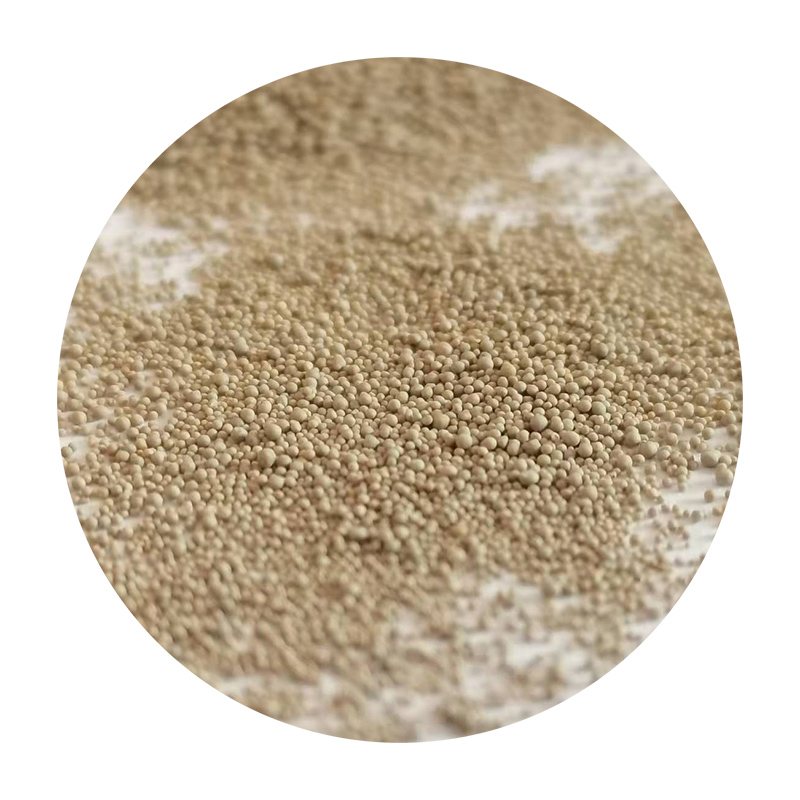
2. Binder Materials Binders like clay play a significant role in sand casting. They help hold the sand grains together to form a sturdy mold. The right balance of binder adds strength without compromising the flowability of the sand, which is critical when pouring molten metal. The quality and type of binder used directly impact the mold's integrity and the overall quality of the cast.
3. Mold Design The design of the mold itself is crucial. It must ensure proper pouring techniques and cooling rates, as these factors are directly linked to the final properties of the casting. Advanced techniques such as the use of 3D printing for patterns can help create more complex shapes and fine details, ensuring precision and reducing the risk of defects.
4. Metal Composition The type of metal chosen for casting can significantly influence the outcome. For high-quality sand casting, alloys that provide excellent fluidity and mechanical properties are preferred. The metallurgical characteristics of the metal must be well-understood and controlled to avoid issues during the cooling and solidification process.
5. Environmental Factors Temperature and humidity can impact the quality of sand casting. For instance, excessive humidity can cause the mold to break down, leading to defects in the cast. Maintaining optimal conditions in the foundry is integral to ensure consistency and quality.
Advancements in Sand Casting Techniques
With the advancement of technology, modern sand casting practices have evolved. Techniques such as computer simulation for mold filling and solidification analysis have emerged, enabling manufacturers to predict and solve potential issues before the casting process begins. Additionally, the integration of automated equipment enhances precision and efficiency, reducing human error.
Conclusion
High-quality sand casting plays a vital role in numerous sectors, providing reliable and robust components. By focusing on sand quality, binder materials, mold design, metal composition, and environmental controls, manufacturers can achieve superior results. As technology continues to progress, the methods and materials used in sand casting will undoubtedly evolve, leading to even higher standards in quality and efficiency. The art of sand casting not only exemplifies traditional craftsmanship but also embodies the innovative spirit of modern manufacturing, ensuring its relevance for years to come.
Post time:des . 15, 2024 21:22
Next:Steel Sand Casting Process for Efficient Metal Fabrication and Design Solutions