The Role of Furan Resin in Sand Casting Enhancing Foundry Performance
Furan resin is a synthetic polymer known for its excellent properties, making it a popular choice in the sand casting industry. This thermosetting resin, derived from furan-alkyd compounds, plays a critical role in improving the efficiency and effectiveness of sand casting processes. As foundries continuously strive to enhance their casting quality while minimizing production costs, furan resin has emerged as a vital material that contributes to these objectives.
What is Sand Casting?
Sand casting is one of the oldest and most widely used metal casting processes. It involves creating a sand mold into which molten metal is poured to form a specific shape. The mold is typically made of silica sand mixed with a binding agent. Traditionally, various binders, such as clay, have been used; however, the introduction of synthetic resins like furan has revolutionized the process.
The Advantages of Furan Resin
One of the primary benefits of using furan resin in sand casting is its superior bonding strength. Compared to traditional clay binders, furan resins provide a strong and durable bond, which improves the integrity of the mold. This enhanced strength allows for the production of intricate castings with finer details that would be difficult to achieve with clay-bonded molds.
Moreover, furan resin exhibits excellent thermal stability. This characteristic is crucial during the casting process, as the molds are subjected to high temperatures when the molten metal is poured in. The ability of furan resin to withstand these conditions without degrading ensures that the mold maintains its shape and dimensional accuracy, leading to high-quality castings.
Furan resin also offers a faster curing time compared to traditional binding materials. In foundry applications, time is often of the essence, and the ability to reduce curing time without compromising strength is a significant advantage. This rapid curing process increases production efficiency, allowing foundries to meet tight deadlines and increase overall output.
In addition, the use of furan resin-laden sands can improve the finish quality of castings. The smooth surface of furan resin molds can minimize the need for machining after the casting process, which can save both time and costs. This quality is particularly advantageous in industries where precision and aesthetics are paramount, such as in the production of automotive components or artistic sculptures.
furan resin sand casting
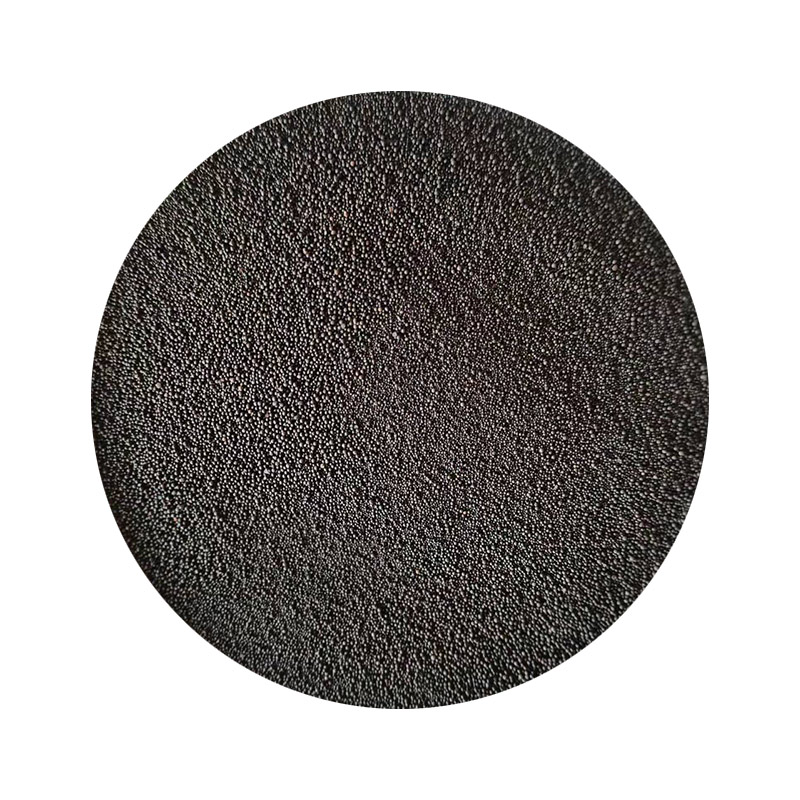
Environmental Considerations
As environmental concerns grow, the sand casting industry is being pushed to adopt more sustainable practices. Furan resin is heralded for its relatively low emission of volatile organic compounds (VOCs) during the curing process. This aspect is particularly appealing to foundries aiming to reduce their environmental footprint and comply with increasingly stringent regulations.
On the recycling front, molds created with furan resin can often be reclaimed and reused, further enhancing the sustainability of the casting process. This reduces waste and allows foundries to use resources more efficiently.
Challenges and Considerations
Despite its many benefits, the use of furan resin in sand casting does come with certain challenges. For instance, its cost is generally higher than that of traditional clay-bonded sands. Foundries must weigh the initial investment in furan resin technology against the potential long-term savings from increased production efficiency and reduced waste.
These challenges, coupled with the need for adequate training in handling and processing furan resin, underscore the importance of careful consideration and planning before transitioning to this material.
Conclusion
In summary, furan resin has proven to be a game-changer in the sand casting industry, offering numerous advantages including superior strength, faster curing times, and improved casting quality. As foundries continue to evolve in response to market demands and environmental challenges, the integration of furan resin technology represents a significant step forward in enhancing performance. By leveraging the unique properties of furan resin, foundries can achieve greater efficiency and produce high-quality castings that meet the rigorous standards of today's industrial applications.
Post time:des . 16, 2024 07:02
Next:difference between sand casting and die casting