3D Sand Printing in Casting Revolutionizing the Foundry Industry
In recent years, the foundry industry has witnessed a significant technological transformation, particularly with the advent of 3D sand printing for casting processes. This innovative approach combines traditional casting methods with advanced additive manufacturing techniques, offering numerous advantages that enhance productivity, precision, and sustainability.
3D sand printing involves the use of a computer-controlled printer to create complex and intricate molds from sand. This process eliminates the need for conventional mold-making methods, such as using patterns and core boxes, which can be time-consuming and labor-intensive. Instead, printers utilize a digital model to layer sand and binders, building up the mold in a matter of hours. This is a stark contrast to the traditional methods that often require days to fabricate a mold, significantly reducing lead times and enabling rapid prototyping.
3D Sand Printing in Casting Revolutionizing the Foundry Industry
Furthermore, the precision and accuracy offered by 3D sand printing can significantly improve the quality of castings. The technology minimizes human error and ensures that the molds are created with exceptional detail. This leads not only to better-fitting parts but also to reduced material waste, as designs can be tailored closely to the final product specifications. With the cost of raw materials continually rising, minimizing waste is both an economic and environmental imperative.
3d sand printing casting
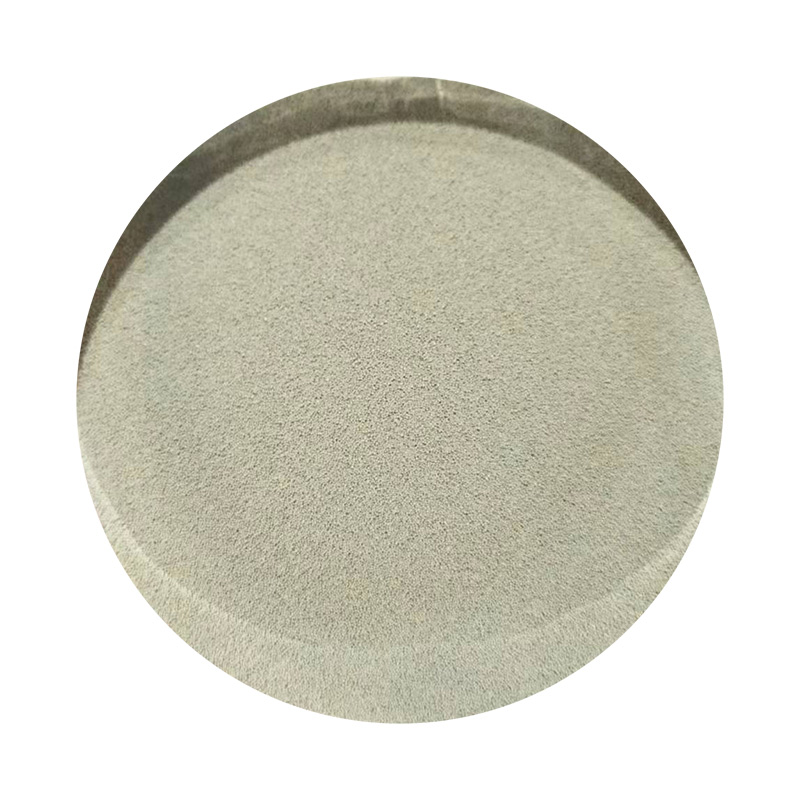
Sustainability is a critical concern in today’s manufacturing landscape, and 3D sand printing aligns well with green initiatives. The process typically requires fewer resources than traditional methods and generates less waste. Additionally, many 3D sand printing systems utilize recyclable sand, further enhancing the sustainability of the casting process. As environmental regulations become stricter, industries are increasingly looking for solutions that can minimize their footprint, and 3D sand printing offers an effective answer.
In terms of operational efficiency, 3D sand printing enables foundries to respond more quickly to market demands. The rapid prototyping capabilities facilitate shorter product development cycles, allowing businesses to bring their products to market faster. This agility is crucial in industries where competition is fierce and customer needs are continually evolving.
Despite the many advantages, challenges remain in the widespread adoption of 3D sand printing technology. Initial investment costs for the required equipment can be significant, and foundries may need to invest in training personnel to effectively utilize this new technology. However, as the technology matures and becomes more accessible, it is likely that we will see an increasing number of foundries integrating 3D sand printing into their operations.
In conclusion, 3D sand printing is revolutionizing the casting industry by enhancing efficiency, precision, and sustainability. As this technology continues to evolve, its impact on manufacturing processes will only grow, paving the way for a new era of innovation in the foundry sector. Embracing this change will enable manufacturers to stay competitive while addressing the pressing challenges of the modern world.
Post time:nóv . 03, 2024 22:56
Next:casting sand suppliers