Understanding Sand Casting A Comprehensive Overview
Sand casting is one of the oldest and most widely used methods for manufacturing metal parts. This versatile and cost-effective casting technique plays a crucial role in various industries, including automotive, aerospace, and construction. In this article, we'll explore the process of sand casting, its advantages, and some applications, providing a thorough understanding for anyone interested in this fascinating method of metalworking.
The Sand Casting Process
The sand casting process begins with the creation of a mold. This involves the following steps
1. Pattern Creation A pattern, typically made of metal, wood, or plastic, is created to reflect the final product's dimensions. The pattern acts as a template for the mold, and it is generally made slightly larger to accommodate for metal shrinkage during the cooling process.
2. Sand Preparation A mixture of sand, clay, and water is prepared to form the mold. This mixture must have the right consistency to hold the shape of the pattern while allowing for easy removal.
3. Mold Making The pattern is placed in a molding box, and the sand mixture is packed around it. The mold is then hardened to ensure it retains the shape of the pattern. This is often done using a process known as jolting, in which the mold box is vibrated to help the sand settle and fill voids.
4. Core Creation (if needed) For parts with hollow sections, cores made of sand must be created. Cores are placed in the mold to form internal cavities.
5. Pouring the Metal Once the mold is prepared, molten metal is poured into the cavity created by the pattern and cores. The metal fills in the space and takes the shape of the mold.
6. Cooling The metal is allowed to cool and solidify. The cooling time depends on the size of the casting and the type of metal used.
7. Mold Removal After the metal has cooled, the sand mold is broken away. The cast part is then cleaned, which may involve removing excess sand and any imperfections.
8. Finishing The final step is finishing the product, which may include machining, polishing, and inspecting for quality.
Advantages of Sand Casting
make sand casting
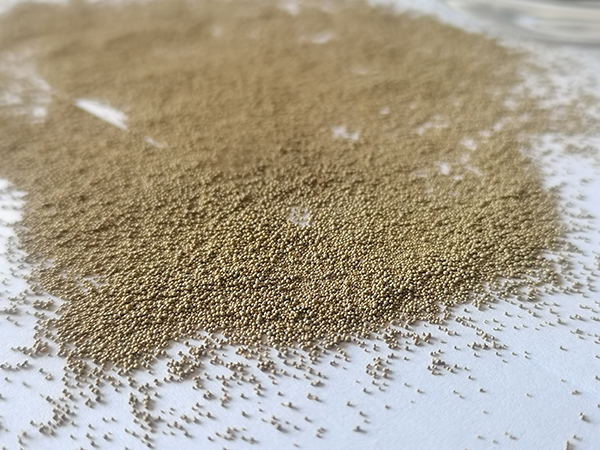
Sand casting offers several notable benefits
- Cost-Effective Sand casting utilizes less expensive materials compared to other casting methods. The reusable nature of the sand also contributes to cost savings.
- Versatility This method accommodates various metal types, including aluminum, iron, and bronze, making it suitable for a wide range of applications.
- Complex Designs Sand casting can produce intricate shapes and large parts with complex geometries that may be challenging for other manufacturing processes.
- Scalability From prototypes to large production runs, sand casting can be scaled to meet production demands without significant changes to the setup.
Applications of Sand Casting
Sand casting is used across numerous sectors
- Automotive Industry Production of engine blocks, transmission casings, and various other components. - Aerospace Applications Manufacturing lightweight yet strong components crucial for aircraft durability and performance.
- Artistic Creations Sculptors and artisans often use sand casting to create unique metal artworks.
- Construction Structural components, such as beams and decorative elements, are often sand cast.
Conclusion
In conclusion, sand casting is a time-honored technique with a wide variety of applications across multiple industries. Its cost-effectiveness, versatility, and ability to produce complex designs make it an invaluable method in the manufacturing process. Understanding the intricacies of this method can enhance appreciation for the metal products we often take for granted, showcasing the skill and craftsmanship involved in their creation.
Post time:Oct . 17, 2024 10:00
Next:Understanding the Benefits and Uses of Resin Coated Sand in Modern Applications