The Advantages of Lost Foam Casting
Lost foam casting (LFC) is an innovative and efficient metal casting process that has gained traction in various industries. It involves the creation of a foam pattern that is coated with a refractory material and then placed in a mold. Once the molten metal is poured into the mold, it vaporizes the foam pattern, resulting in a final product that closely resembles the original design. This process offers a range of advantages that set it apart from traditional casting methods.
1. Design Flexibility and Complexity
One of the most significant advantages of lost foam casting is the design flexibility it provides. The foam patterns can be produced with intricate details and complex geometries that are often challenging to achieve with traditional casting methods. This allows manufacturers to create highly detailed components with smooth surfaces, reducing the need for additional machining. As a result, companies can achieve higher precision and create parts that meet demanding specifications without compromising on the design integrity.
2. Reduced Production Costs
LFC is known for its cost-effectiveness, particularly for medium to large production runs. The process minimizes the need for tooling, such as metal molds, which can be expensive and time-consuming to produce. Instead, foam patterns can be created quickly and at a fraction of the cost. Moreover, the elimination of machining processes required for traditional castings leads to significant savings in labor and material costs. This makes lost foam casting an attractive option for manufacturers looking to optimize their production efficiency and reduce overall costs.
3. Improved Material Properties
Another notable benefit of lost foam casting is the ability to produce parts with improved material properties. The LFC process generally results in a more uniform microstructure, which can enhance the strength and durability of the final product. The rapid cooling of the molten metal as it fills the mold also contributes to a denser and more robust casting. Industries that demand high-performance components, such as aerospace and automotive sectors, can particularly benefit from these enhanced material characteristics.
advantages of lost foam casting
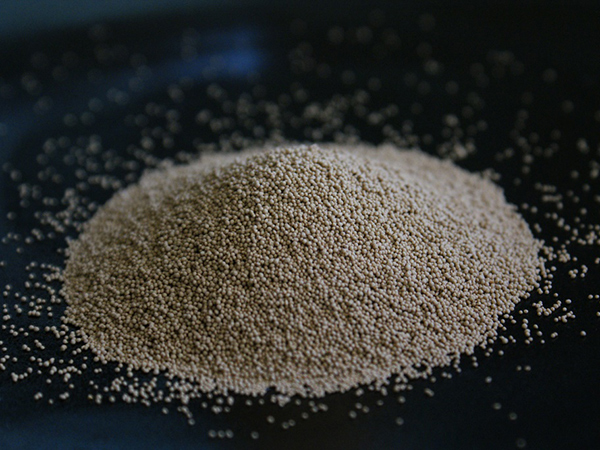
In an era where sustainability is a critical concern, lost foam casting offers several environmental benefits. The process generates less waste compared to traditional casting methods. The foam patterns can be recycled, and the refractory coating used in the process is often made from environmentally friendly materials. Additionally, the LFC technique typically requires less energy, contributing to a lower carbon footprint. As companies increasingly pursue greener manufacturing practices, the environmental advantages of LFC make it an appealing option.
5. Reduction of Leads and Cycle Times
The lost foam casting process can significantly reduce lead times and cycle times in production. Since the foam patterns can be produced quickly and do not require the lengthy preparation associated with traditional molds, manufacturers can respond more rapidly to market demands. This flexibility allows companies to adapt to changes in product requirements or production volumes without extensive delays. In today's fast-paced business environment, this ability to streamline production processes is invaluable.
6. Excellent Surface Finish
Parts created through lost foam casting often have superior surface finishes compared to those produced using traditional casting methods. Since the foam pattern directly influences the final surface quality, the absence of a rigid mold helps reduce the occurrence of defects such as seams, mismatches, or rough surfaces. A better surface finish can reduce the need for post-processing, thus saving time and costs associated with additional machining operations.
Conclusion
The advantages of lost foam casting make it a compelling option for various industries seeking efficiency, precision, and sustainability in their manufacturing processes. With its flexibility in design, compatibility with complex geometries, reduced production costs, superior material properties, and environmental benefits, LFC stands out as a modern solution to the challenges faced in traditional casting. As technology continues to evolve, the lost foam casting process is likely to gain even more prominence, further establishing its role as a key player in the future of manufacturing. Businesses that embrace this innovative technique are not only likely to enhance their production capabilities but also position themselves as leaders in an increasingly competitive market.
Post time:Des . 03, 2024 19:40
Next:metal sand casting