The Benefits of Sand Casting
Sand casting, one of the oldest and most versatile metal casting processes, has been utilized for centuries to create complex metal parts and components. This technique involves pouring molten metal into a sand mold, where it cools and solidifies into the desired shape. While modern methods like die casting and investment casting have emerged, sand casting remains a favored choice across various industries for several compelling reasons. In this article, we will explore the key benefits of sand casting that highlight its relevance and efficiency in today’s manufacturing environment.
1. Cost-Effectiveness
One of the primary advantages of sand casting is its cost-effectiveness, particularly for low to medium production volumes. The materials used in sand casting, primarily silica sand, are relatively inexpensive and readily available. Additionally, the molding process requires minimal investment in equipment compared to more advanced casting techniques. This affordability makes sand casting an attractive option for startups and small manufacturers looking to produce parts without incurring significant capital expenses.
2. Flexibility and Design Freedom
Sand casting offers remarkable design flexibility. The process allows for the creation of complex geometries that would be challenging or impossible with other methods. Mold design can be easily modified to accommodate various part designs, and intricate details can be incorporated into the molds without additional costs. This flexibility extends to the range of materials that can be used; sand casting can handle numerous alloys, including aluminum, iron, and bronze, making it suitable for a wide array of applications across different sectors.
3. Scalability
Another noteworthy benefit of sand casting is its scalability. Whether producing a single prototype or thousands of parts, sand casting can adapt to the volume requirements. For companies that need to ramp up production quickly or test different designs, sand casting is an ideal solution. The process can be streamlined for large-scale production, increasing efficiency while maintaining quality.
4. Durability and Strength
Sand casting produces parts that are inherently strong and durable. The cooling rate of the cast metal significantly influences its mechanical properties, and sand casting typically allows for a slower cooling process. This slower cooling rate contributes to a finer grain structure, enhancing the strength and durability of the final product. As a result, parts produced through sand casting often exhibit excellent wear resistance and can perform effectively in demanding environments.
sand casting benefits
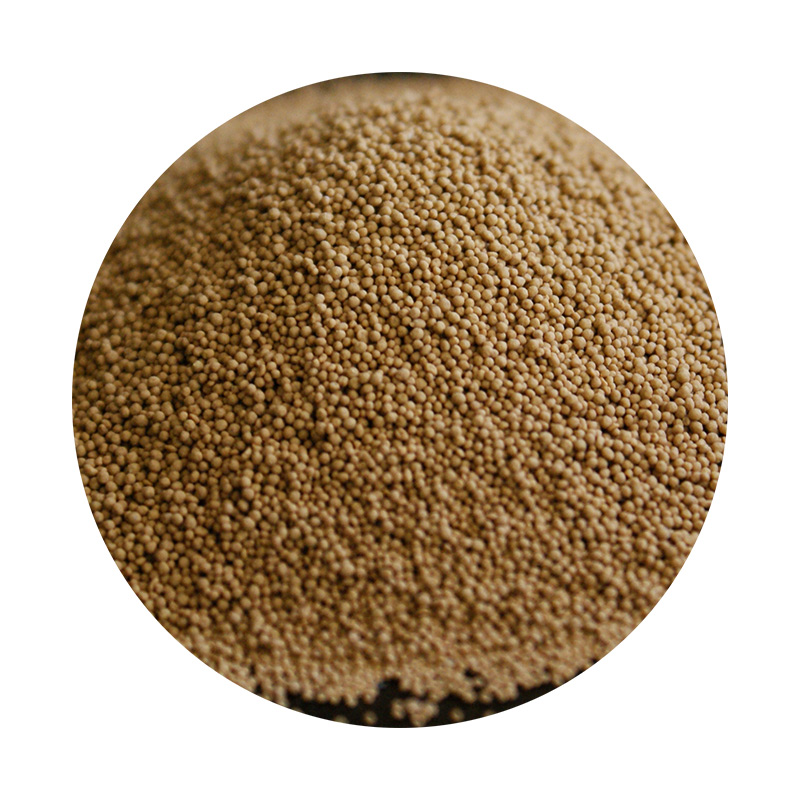
5. Low Waste Generation
The sand casting process is also characterized by its minimal waste generation. Unlike some manufacturing methods that chop away material from a solid block, sand casting uses only the requisite amount of metal. Any surplus sand can be reused for future molds, further reducing material waste and promoting sustainability in manufacturing. This eco-friendly aspect appeals to industries that are increasingly focused on reducing their environmental footprint.
6. Rapid Prototyping
For engineers and designers, the ability to quickly create prototypes is crucial in product development. Sand casting facilitates rapid prototyping by allowing designers to create molds in a relatively short timeframe. This speed enables companies to test designs and make adjustments based on performance analysis without extensive lead times. The iterative process fosters innovation and accelerates the product development cycle, providing a competitive edge in the market.
7. Simplicity in Process
The sand casting process is straightforward, involving just a few essential steps creating the mold, pouring molten metal, and allowing it to cool. This simplicity means that setup for production can be accomplished in a timely manner. Additionally, the learning curve for employees is relatively low, allowing companies to train workers quickly and efficiently.
8. Versatility Across Industries
Finally, sand casting’s versatility allows it to be employed across a myriad of industries. From automotive and aerospace to art and architecture, sand casting can produce components ranging from engine blocks to intricate sculptures. This cross-industry applicability ensures that sand casting remains a vital component in the global manufacturing landscape.
Conclusion
In conclusion, sand casting offers a myriad of benefits that continue to make it a relevant and valuable method in the manufacturing sector. Its cost-effectiveness, design flexibility, scalability, durability, and low waste generation make it an ideal choice for various applications. As industries continue to strive for efficiency and innovation, sand casting stands out as a time-honored technique that meets modern demands while paving the way for future developments in metal casting technology.
Post time:Դկտ . 25, 2024 20:59
Next:High-Quality Fine Casting Sand for Precision Metal Molding and Foundry Applications