Sand Casting Alloys An Overview
Sand casting is one of the oldest and most widely used metal casting processes, favored for its versatility and ability to produce complex shapes. This process involves creating a mold out of sand that can withstand the high temperatures of molten metal. The choice of alloy used in sand casting is crucial, as it directly influences the properties and performance of the final product. In this article, we will explore the common alloys used in sand casting, their characteristics, and their applications.
Common Alloys in Sand Casting
1. Aluminum Alloys Aluminum is one of the most popular materials used in sand casting due to its lightweight and excellent corrosion resistance. Common aluminum alloys used in sand casting include A356 and A380. A356 is known for its good fluidity and mechanical properties, making it suitable for automotive and aerospace components. A380, on the other hand, is ideal for high-pressure die casting but is also used in sand casting when intricate shapes are needed.
2. Iron Alloys Gray iron is the most common type of iron used in sand casting due to its excellent casting properties. It has a high level of castability and good wear resistance, which makes it an ideal choice for heavy-duty applications such as engine blocks and machinery components. Ductile iron, a high strength variant, is also used in sand casting. It offers higher ductility compared to gray iron, enabling it to withstand greater impacts, making it suitable for automotive and industrial applications.
3. Copper Alloys Bronze and brass are the main copper alloys used in sand casting. Bronze, typically a mix of copper and tin, exhibits excellent corrosion resistance, and is often used in marine applications. Brass, an alloy of copper and zinc, has good malleability and is used in decorative items, plumbing fittings, and electrical components. Copper alloys are sought after for their aesthetic appeal and mechanical properties.
4. Magnesium Alloys Magnesium alloys are lighter than aluminum and can offer high strength-to-weight ratios. They are commonly alloyed with aluminum or zinc. While magnesium is less commonly cast than aluminum, it has gained traction in industries where weight savings are critical, such as aerospace and automotive. However, magnesium's high reactivity with air requires careful handling during the casting process.
sand casting alloys
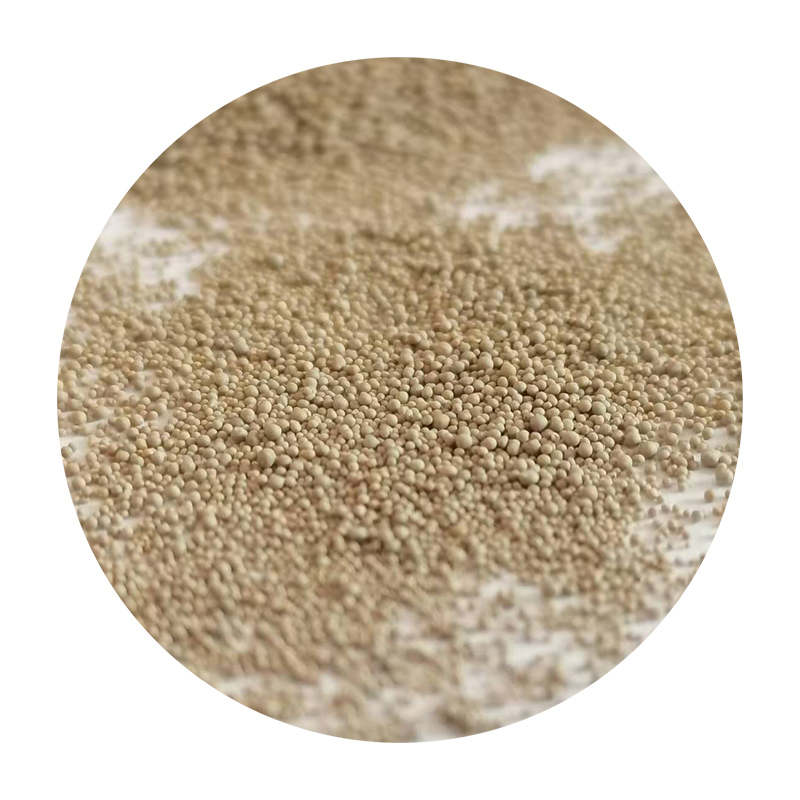
Considerations When Choosing Alloys
When selecting an alloy for sand casting, several factors must be taken into account, such as
- Casting Complexity Some alloys flow better than others into intricate mold shapes. Aluminum and zinc alloys are often preferred for complex geometries. - Mechanical Requirements The intended use of the casting will determine the required strength, ductility, and wear resistance, which can vary significantly between different alloys. - Cost Alloy cost can vary widely. Generally, aluminum is cheaper than copper alloys while providing a good balance of properties. - Post-Casting Treatments Some alloys may require additional heat treatments or surface finishing processes to achieve desired mechanical properties and surface quality.
Applications of Sand Casting Alloys
The versatility of sand casting alloys allows for a broad range of applications across multiple industries. In the automotive sector, aluminum and iron alloys are commonly used for engine parts, transmission cases, and structural components. The marine industry often utilizes bronze for propellers and fittings, while electrical components frequently use brass for switches and connectors.
In conclusion, sand casting remains a vital manufacturing process, thanks to its adaptability and the variety of alloys available. By understanding the properties and applications of different sand casting alloys, manufacturers can make informed decisions that lead to better product performance and efficiency.
Post time:Նյմ . 28, 2024 02:13
Next:Innovative Techniques for Using Foundry Casting Sand in Metal Manufacturing