Rapid Sand Casting An Innovative Approach to Metal Casting
Rapid sand casting is a cutting-edge manufacturing technique that combines the principles of traditional sand casting with modern advancements in technology and materials. This process allows for quicker turnaround times, increased precision, and lower costs, making it a highly attractive option for various industries, including automotive, aerospace, and consumer products. This article delves into the fundamentals of rapid sand casting, its advantages, and its potential applications.
Understanding Rapid Sand Casting
At its core, rapid sand casting involves the creation of a mold from sand, which is then filled with molten metal to produce intricate parts. The traditional sand casting process is characterized by its use of a mixture of sand, clay, and water to form a mold, typically requiring extensive lead times for mold preparation and production. However, rapid sand casting leverages advanced technologies such as 3D printing to streamline the mold-making process, drastically reducing the time from design to production.
Using computer-aided design (CAD) software, engineers can create highly detailed mold designs that can be instantly printed using a 3D printer. This not only speeds up the preparation of molds but also allows for more complex geometries that would be difficult or impossible to achieve using traditional methods. Once the mold is ready, molten metal is poured into it, where it solidifies and creates the desired part.
Advantages of Rapid Sand Casting
1. Speed The most significant benefit of rapid sand casting is its ability to reduce lead times. Traditional sand casting can take weeks to prepare molds, while rapid sand casting can often produce molds in a matter of days. This is critical for industries that rely on rapid prototyping and short production runs.
2. Cost-Effectiveness In addition to speeding up the process, rapid sand casting can also lower costs. The reduced time for mold creation translates to lower labor and overhead expenses. Moreover, the precision of the molds produced minimizes material waste, further driving down costs.
rapid sand casting
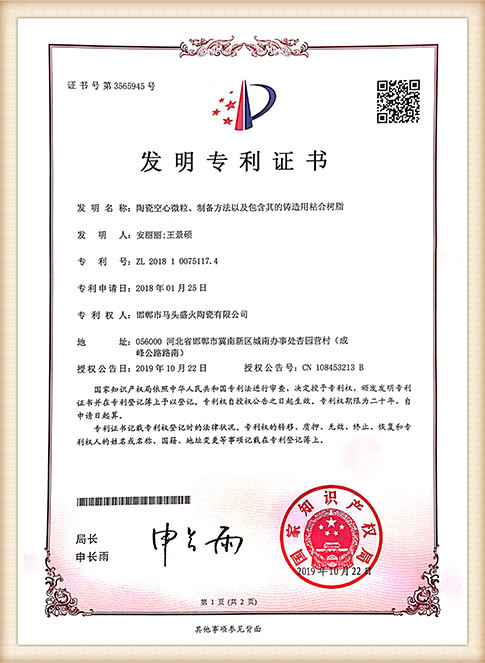
3. Design Flexibility With rapid sand casting, designers are not limited by the constraints of traditional mold-making techniques. The use of 3D printing allows them to create complex designs that may include intricate internal features or delicate external shapes. This flexibility can lead to innovative product designs that enhance functionality and performance.
4. Improved Accuracy and Quality The high precision of 3D printing technology results in molds that fit together perfectly, which helps ensure a more accurate final product. Additionally, the reduced need for post-processing can maintain the integrity and surface quality of the cast parts.
5. Sustainability Rapid sand casting can also be more environmentally friendly than traditional methods. The ability to produce parts quickly and with minimal waste aligns with the growing emphasis on sustainable manufacturing practices. Moreover, advancements in materials mean that sand molds can be reused or recycled, further reducing the environmental impact.
Applications of Rapid Sand Casting
The versatility of rapid sand casting makes it suitable for a wide range of applications across different sectors. In the automotive industry, it is used to create engine components, brackets, and other parts where lightweight and strength are critical. The aerospace sector benefits from the ability to produce complex components that can enhance aircraft performance while reducing weight.
Furthermore, consumer products such as custom jewelry, unique hardware, and specialized tools can be produced through rapid sand casting. The ability to quickly prototype designs means that companies can test and refine their ideas before committing to full-scale production.
Conclusion
As industries continue to seek ways to enhance efficiency and reduce costs, rapid sand casting emerges as a formidable solution. With its ability to produce high-quality, precise molds quickly, this innovative process represents a significant evolution in the manufacturing landscape. By adopting rapid sand casting technology, manufacturers can achieve faster production cycles, greater design freedom, and improved sustainability, positioning themselves to meet the demands of an ever-evolving market.
Post time:Հկտ . 12, 2024 07:48
Next:Materials Utilized in Sand Casting Processes for Enhanced Metal Forming Techniques