Low Volume Sand Casting An Efficient Approach for Custom Metal Components
In the dynamic world of manufacturing, industries are consistently seeking innovative methods to produce high-quality metal components while minimizing costs and lead times. One such method gaining popularity is low volume sand casting. This technique offers significant advantages for businesses looking to produce customized parts without the need for large-scale production runs. This article explores the concept of low volume sand casting, its process, benefits, and applications in various industries.
Understanding Low Volume Sand Casting
Low volume sand casting is a manufacturing process used to create metal parts through the use of sand molds. Unlike traditional sand casting, which typically involves large production runs, low volume sand casting focuses on producing smaller quantities of parts, often ranging from a handful to a few hundred units. This approach is particularly beneficial for prototypes, specialized components, and customized designs.
The Sand Casting Process
The sand casting process involves several critical steps
1. Pattern Creation The first step is to create a pattern, which is a replica of the final product. Patterns can be made from various materials, including wood, metal, or plastic. The key here is that the pattern is designed to accommodate any shrinkage that may occur when the metal cools.
2. Mold Preparation Once the pattern is ready, it is used to form a mold by packing sand around it. The mold consists of two halves (cope and drag) that are joined together. The sand used in molds is often mixed with a binding agent to enhance its strength and ability to hold shape.
3. Metal Melting The next step is melting the metal that will be poured into the mold. Common metals used in sand casting include aluminum, bronze, and iron. The molten metal is heated to a specific temperature to ensure it flows easily into the mold cavities.
4. Pouring Once the metal is ready, it is poured into the mold. The process must be done carefully to prevent defects such as air bubbles or premature hardening.
5. Cooling and Solidification After pouring, the metal cools and solidifies within the mold. This process can take anywhere from a few minutes to several hours, depending on the metal used and the thickness of the casting.
low volume sand casting
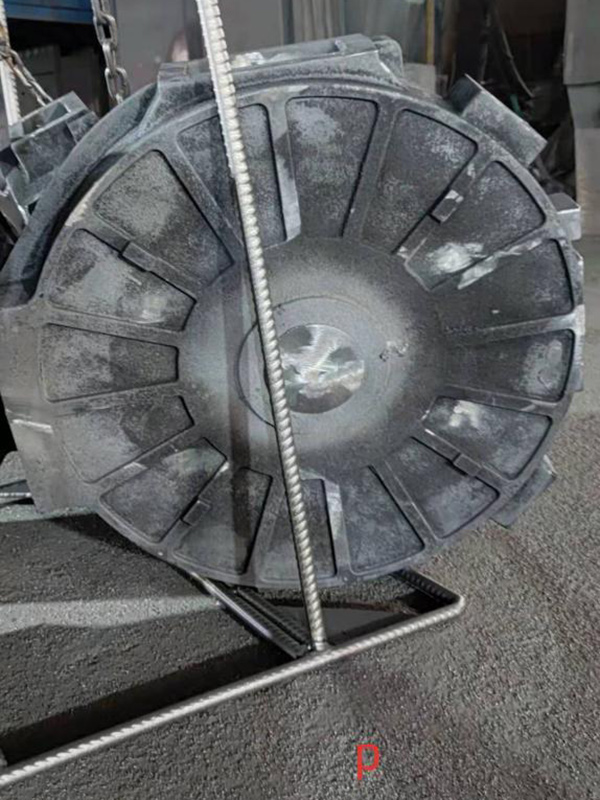
6. Mold Removal and Finishing Once the metal has cooled, the mold is broken apart, and the casting is removed. This step is followed by various finishing processes, such as grinding, machining, and surface treatment, to achieve the final specifications.
Benefits of Low Volume Sand Casting
1. Cost-Effective One of the most significant advantages of low volume sand casting is its cost-effectiveness. Traditional manufacturing methods may require expensive tooling and setup costs for large production runs. Low volume sand casting reduces these costs, making it feasible for small batches.
2. Quick Turnaround With shorter lead times compared to high-volume production methods, low volume sand casting allows manufacturers to respond quickly to market demands and customer specifications.
3. Design Flexibility The sand casting process accommodates complex geometries and intricate designs. Changes and modifications can be easily integrated into the pattern, facilitating customization.
4. Material Versatility This method supports a wide range of metals and alloys, providing manufacturers with various material options to suit specific applications.
5. Post-Casting Modifications After casting, parts can be easily machined or treated to meet specific requirements, enhancing their functionality and performance.
Applications in Various Industries
Low volume sand casting serves various industries, including aerospace, automotive, medical, and consumer goods. In aerospace, for example, lightweight aluminum castings are often needed for aircraft components. Similarly, automotive manufacturers may require specialized parts for prototypes or low-production models. The medical industry also benefits from custom tools and equipment created through low volume sand casting, ensuring precision and quality while adhering to regulatory standards.
Conclusion
In conclusion, low volume sand casting is a valuable manufacturing process that strikes a balance between flexibility and cost-effectiveness. Its ability to produce customized metal components quickly and efficiently makes it an attractive option for industries seeking to innovate while minimizing investment risks. As technology continues to advance, low volume sand casting will likely evolve, further enhancing its capabilities and applications. Whether for prototyping or specialized production, this technique has firmly established itself as a reliable choice in the manufacturing landscape.
Post time:Նյմ . 08, 2024 16:28
Next:what is a sand casting