Lost Foam Sand Casting An Innovative Approach to Metal Casting
Lost foam sand casting is a modern manufacturing process that combines the traditional methods of sand casting with a more innovative approach to increasing precision and reducing waste. This technique employs a foam pattern, typically made from expanded polystyrene (EPS), which is coated with sand and then used to create metal parts. The process offers various advantages over conventional casting methods, making it an attractive option for a wide range of applications.
At the heart of lost foam sand casting is its unique pattern-making process. Unlike traditional methods where metal patterns are created, lost foam utilizes a foam replica of the final product. The foam pattern is first coated with a fine layer of sand that is mixed with a bonding agent. This mixture is needed to ensure that the sand maintains its shape during the casting process. Once the foam pattern is coated and placed in a molding box, molten metal is poured directly into the mold. As the metal fills the cavity, the heat causes the foam pattern to vaporize and escape, leaving behind a precise metal replica of the original foam form.
One of the primary benefits of lost foam sand casting is its ability to produce complex shapes with intricate details. The foam patterns can be easily manufactured to meet specific design requirements, allowing for greater flexibility in product design. This capability is particularly advantageous for industries that demand high precision, such as automotive, aerospace, and intricate machinery manufacturing. Additionally, because there is no need for additional cores or extensive machining, the process streamlines production, which can result in shorter lead times.
Another significant advantage of lost foam sand casting is its waste reduction potential. Traditional casting methods may require substantial amounts of material to be machined away from the final product, leading to increased waste. In contrast, the lost foam process minimizes material waste because the only material that is lost during the process is the foam pattern itself. Additionally, any excess metal can often be recycled and reused, further enhancing the sustainability of this manufacturing approach.
lost foam sand casting
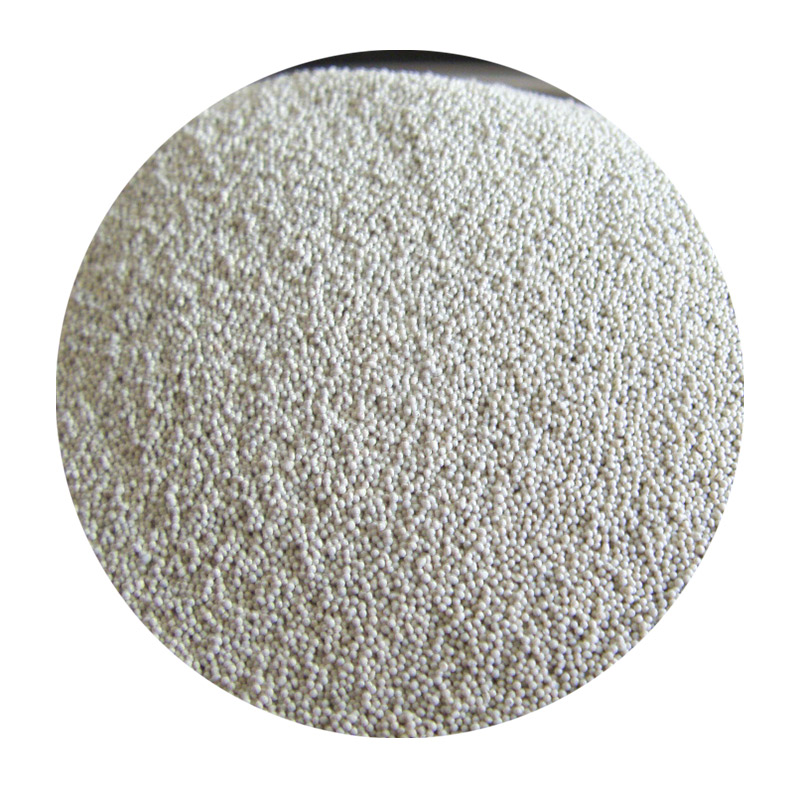
The lost foam sand casting process also boasts high dimensional accuracy. The vaporization of the foam ensures that the metal takes the exact shape of the pattern, resulting in a high-quality finish and reduced need for post-casting machining. This accuracy not only improves the mechanical properties of the cast product but also enhances the aesthetic quality, making it suitable for visible components in various applications.
Chemically, the process is also less harmful compared to some traditional methods. The use of EPS patterns minimizes harmful emissions typical of polymer or metal pattern manufacturing. However, it is important to manage the casting environment to ensure any potential fumes produced during the vaporization of the foam are adequately controlled.
Despite its numerous advantages, there are some challenges associated with lost foam sand casting. The initial setup, including the creation of foam patterns and molds, can be more expensive than traditional methods, particularly for small batch productions. Additionally, not all foundries may be equipped to handle the specific requirements of this technique, which can limit its adoption in certain regions or industries.
In conclusion, lost foam sand casting represents a significant advancement in the field of metal casting. By utilizing foam patterns, this process offers several benefits, including the ability to produce complex geometries, minimize waste, and achieve high dimensional accuracy. While there are challenges to overcome, the potential advantages make lost foam sand casting a compelling choice for manufacturers seeking a modern solution to their casting needs. As industries continue to seek out efficient and sustainable manufacturing practices, lost foam sand casting is likely to gain even greater traction in the years to come.
Post time:Նյմ . 27, 2024 23:20
Next:Quality Metal Casting Sand Available for Purchase at Competitive Prices Online