Lost Foam Castings An Innovative Approach to Metal Casting
Lost foam casting (LFC) is a highly efficient and innovative casting process that has gained significant traction in various industrial applications. This method, which combines traditional casting techniques with modern technology, offers numerous advantages over conventional sand casting processes. In this article, we explore the principles of lost foam castings, its applications, benefits, and the future of this distinctive method in the manufacturing landscape.
What is Lost Foam Casting?
The lost foam casting process involves creating a foam pattern of the part to be produced and then coating it with a sand mixture. The foam pattern is made from expanded polystyrene (EPS) and is designed to replicate the exact shape of the final metal part. Once the pattern is prepared, it is coated with a mixture of sand and a binding agent, usually a resin, to form a mold. The mold is then heated, causing the foam to evaporate or burn out, leaving a cavity that is filled with molten metal. This method enables intricate designs, precise dimensions, and a smooth surface finish without the need for additional machining.
Applications of Lost Foam Castings
Lost foam casting is widely used across various industries, including automotive, aerospace, and general manufacturing. This versatility stems from its capability to produce complex geometries, lightweight components, and large casting sizes. For the automotive industry, lost foam castings have become increasingly common in the production of engine blocks, cylinder heads, and other critical components. Furthermore, aerospace manufacturers benefit from the weight savings and structural integrity provided by lost foam castings, making it a preferred choice for producing parts like brackets, housings, and structural components.
Benefits of Lost Foam Castings
The lost foam casting process offers several distinct advantages
1. Complex Geometries Lost foam casting allows for the creation of intricate shapes and designs that are challenging to achieve with traditional casting methods. This flexibility opens the door to innovation in product design.
lost foam castings
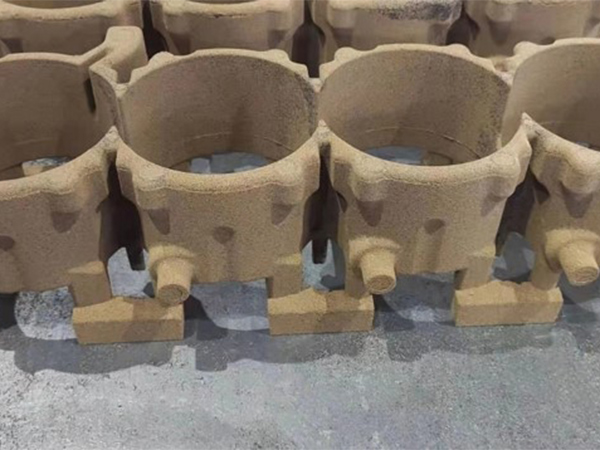
2. Reduced Waste Traditional sand casting can generate significant waste material during machining operations. In contrast, lost foam casting minimizes waste by producing parts to near-net shape, reducing the need for extensive post-processing.
3. Enhanced Surface Finish The process yields a smoother surface finish due to the vaporization of foam, which results in fewer defects and imperfections. This translates to less time and cost spent on finishing operations.
4. Cost-Effectiveness By reducing the need for tooling and machining, lost foam casting can be a cost-effective solution for producing high-quality parts in low to medium production runs.
5. Material Versatility Various metals, including aluminum, iron, and steel, can be used in lost foam casting, making it a flexible option for diverse applications.
The Future of Lost Foam Castings
As industries continue to evolve and demand increasingly complex components, lost foam casting is poised for growth. The amalgamation of advanced manufacturing techniques, such as additive manufacturing and computer-aided design (CAD), with lost foam casting can lead to even greater efficiencies and capabilities. Moreover, the rise of sustainable manufacturing practices supports the adoption of techniques like lost foam casting, which aligns with resource conservation and waste reduction goals.
In addition, ongoing innovations in materials and processes will expand the applications of lost foam casting. Advances in foam materials and binding agents can enhance the performance characteristics of cast parts, making them suitable for even more demanding environments.
Conclusion
Lost foam castings represent a remarkable evolution in the casting industry, offering a unique combination of design freedom, efficiency, and quality. With its ability to produce lightweight, intricate, and high-performance components, lost foam casting is not just a passing trend but a significant player in the future of manufacturing. As industries embrace technological advancements and sustainability, lost foam casting will continue to carve its niche, driving the need for innovation and excellence in metal casting.
Post time:Դկտ . 07, 2024 15:49
Next:coated sand