Lost Foam Casting A Modern Approach to Metal Casting
Lost foam casting is an advanced method of metal casting that has gained popularity in various industries due to its unique advantages and efficiencies. This technique stands out for its ability to produce complex shapes and high-quality components, making it a preferred choice for manufacturers looking to optimize their production processes.
The Process of Lost Foam Casting
The lost foam casting process begins with the creation of a foam pattern, typically made from expanded polystyrene (EPS). This foam pattern is an exact replica of the final product to be cast. The pattern is then coated with a fine layer of sand, which usually contains a bonding agent to help it maintain its shape. The coated foam pattern is heated to remove any moisture and to enhance the bond between the sand particles.
Once the pattern is prepped, molten metal is poured directly into the sand mold. The key feature of this method is that as the molten metal enters the mold, it vaporizes the foam pattern, essentially lost in the process, hence the name lost foam. The metal then fills the cavity left behind, taking on the shape of the original foam pattern. After a cooling period, the sand mold is removed, revealing the final casting, which often requires minimal finishing due to its high level of detail.
Advantages of Lost Foam Casting
One of the primary advantages of lost foam casting is its ability to deliver intricate designs with tight tolerances. Traditional casting methods often struggle with complex geometries, requiring additional machining or assembly. In contrast, lost foam casting allows for the creation of highly detailed parts in a one-step process, significantly reducing the need for post-casting work.
Another notable benefit is the reduction in material waste. Since the foam pattern is completely vaporized in the casting process, there is little to no scrap generated. This is in stark contrast to other methods, where excess material can create significant waste. The efficiency of this technique not only benefits the environment but also reduces production costs.
Furthermore, lost foam casting is highly adaptable to various types of metals, including aluminum, iron, and even some stainless steels. This versatility allows manufacturers to choose the right material for their specific application, enhancing performance and durability of the final product.
lost-foam casting
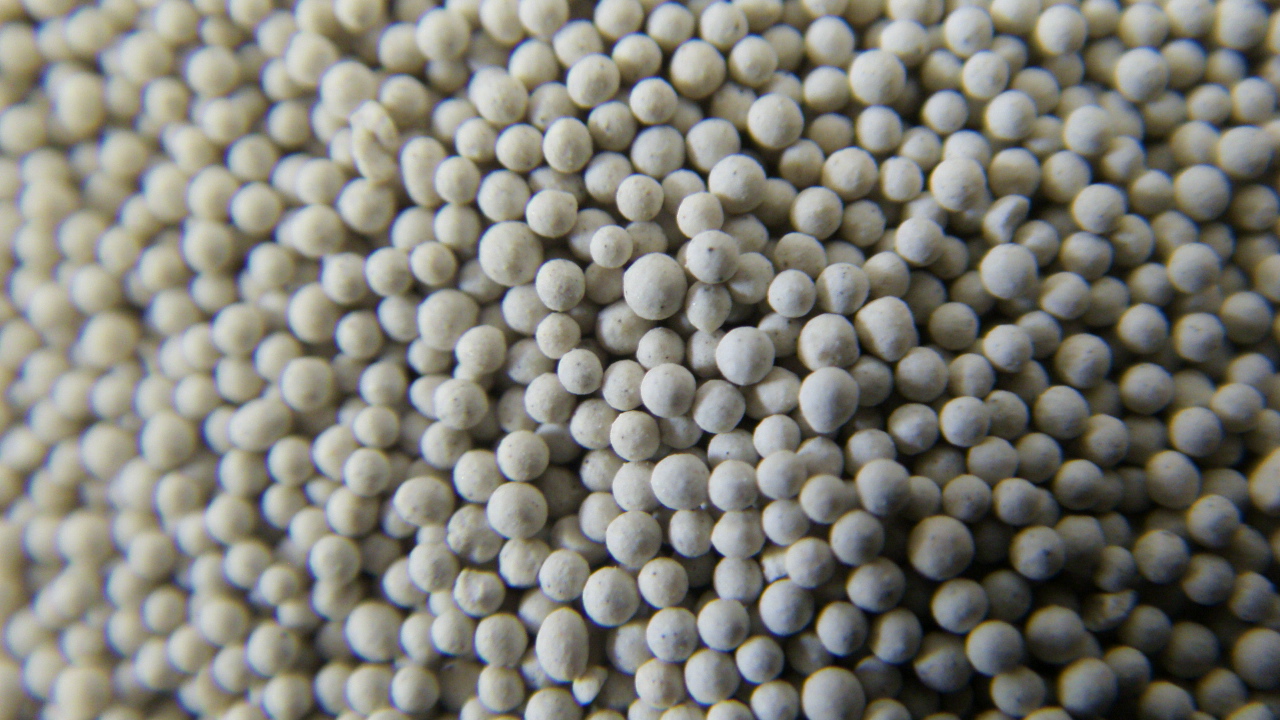
Applications of Lost Foam Casting
Lost foam casting has found its niche in numerous industries, including automotive, aerospace, and heavy machinery. In the automotive sector, for example, it’s commonly used for producing engine components, which require precision and lightweight characteristics. The aerospace industry also leverages this technology for manufacturing intricate parts that must meet rigorous safety and performance standards.
Additionally, the technology can be employed in the production of artistic sculptures and custom-designed products, showcasing its flexibility in both industrial and creative applications. This broad range of applications demonstrates the potential of lost foam casting to revolutionize traditional manufacturing processes.
Challenges and Future Prospects
Despite its many advantages, lost foam casting does come with challenges. The production of foam patterns and the handling of the materials require specialized knowledge and equipment, which can be a barrier for some manufacturers. Additionally, controlling the pour rate of the molten metal is crucial, as any inconsistencies can lead to defects in the final casting.
Looking ahead, advancements in material science and digital manufacturing technologies may further enhance the lost foam casting process. With the integration of computer-aided design (CAD) and additive manufacturing techniques for pattern creation, the potential for customization and production efficiency can be significantly enhanced.
Conclusion
In conclusion, lost foam casting is a sophisticated metal casting technique that offers several benefits, including precision, reduced waste, and versatility in material selection. Its ability to produce complex shapes with tight tolerances makes it an attractive option for various industries. As technology continues to evolve, lost foam casting stands poised to play an even more critical role in the future of manufacturing, paving the way for innovative designs and sustainable practices in metal casting.
Post time:Դկտ . 15, 2024 11:01
Next:parting sand in foundry