The Role of Foundry Sand Suppliers in the Manufacturing Industry
Foundry sand is a crucial material in the casting process within the manufacturing industry. It plays an integral role in creating metal components by providing a mold material that can withstand high temperatures and pressures. The suppliers of foundry sand are vital to ensuring that the production processes in various industries run smoothly, efficiently, and effectively. This article will explore the significance of foundry sand suppliers, the types of foundry sands available, and the challenges they face in the industry.
Importance of Foundry Sand Suppliers
Foundry sand suppliers serve as the backbone of the foundry industry. They are responsible for providing the high-quality sands essential for producing various metal parts used in automotive, aerospace, construction, and various other sectors. The quality of the sand directly impacts the final product's durability, precision, and cost-effectiveness. Suppliers must understand the specific requirements of their clients and deliver sand that meets strict industry standards.
Moreover, foundry sand suppliers must be adaptable, as the demand for different types of sands can fluctuate according to market needs. They often work closely with foundries to ensure a steady supply of materials and help streamline operations. By maintaining a close relationship with their clients, suppliers can better anticipate trends in production and adjust their sourcing strategies accordingly.
Types of Foundry Sands
Foundry sand can be categorized into several types based on its composition and characteristics
. The most commonly used types include1. Silica Sand This is the most prevalent type of foundry sand, valued for its high melting point and ability to retain shape during the pouring of molten metal. Silica sand is used in ferrous and non-ferrous metal casting and is prized for its availability and low cost.
2. Chromite Sand Known for its high thermal conductivity and resistance to metal penetration, chromite sand is often used for casting high-performance alloys. It is particularly suited for applications involving heavy steel casting and high-temperature conditions.
foundry sand suppliers
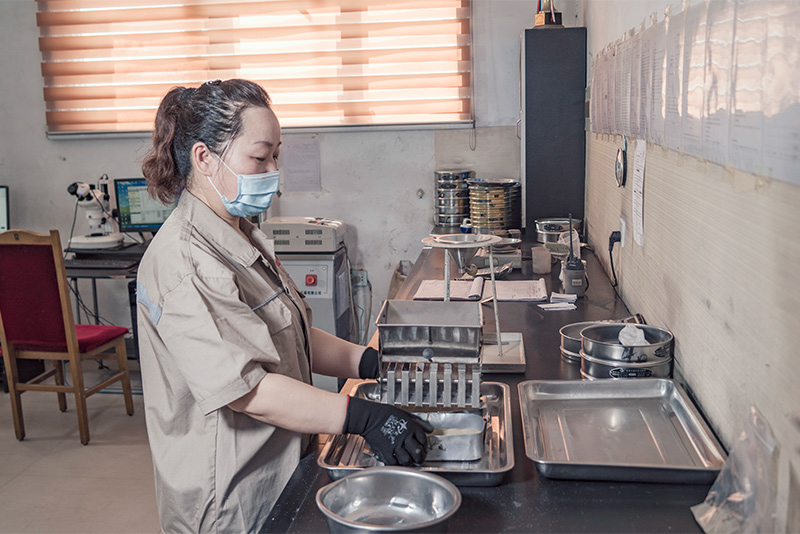
3. Zircon Sand Zircon sand is less common than silica but is utilized in specialty applications due to its high thermal stability and low thermal expansion. It is frequently used in industries where precision is crucial, such as aerospace and medical equipment manufacturing.
4. Green Sand This type of sand is a mixture of silica sand, clay, and water. It is used primarily in the production of ferrous castings and is valued for its ability to create complex molds.
5. Synthetic Sands Some suppliers offer synthetic alternatives that are specifically engineered to meet the unique requirements of modern foundries. These sands can provide superior mold characteristics and improved casting quality.
Challenges Faced by Foundry Sand Suppliers
Despite their integral role in the industry, foundry sand suppliers encounter several challenges. One significant issue is the volatility of raw material costs. Fluctuations in available resources like silica or chromite can lead to unpredictable pricing, impacting both suppliers and foundries. Suppliers must develop effective sourcing strategies to mitigate these risks and ensure that they can deliver materials at stable prices.
Environmental regulations are another challenge faced by foundry sand suppliers. The extraction and processing of sands can have a significant environmental impact, leading to stringent regulations that suppliers must adhere to. Many suppliers are now investing in sustainable practices, including the recycling of foundry sands to minimize waste and reduce environmental footprint.
Lastly, the advancements in technology and the demand for improved casting processes require suppliers to continually adapt their product offerings. Investing in research and development is essential for suppliers to stay competitive in a rapidly evolving market. Collaborating with research institutions and foundries can lead to innovative solutions that benefit both parties.
Conclusion
In conclusion, foundry sand suppliers play a critical role in the manufacturing industry by providing essential materials for metal casting processes. Their ability to supply various types of sand, adapt to changing market demands, and overcome challenges is crucial for the success of foundries. As the industry continues to evolve, the importance of reliable and innovative foundry sand suppliers will undoubtedly grow, shaping the future of metal manufacturing.
Post time:Հկտ . 05, 2024 07:38
Next:Cast of the Desert Sands