The Difference Between Sand Casting and Permanent Mold Casting
Casting is a fundamental manufacturing process used to create complex metal parts and shapes by pouring molten metal into molds. Among various casting methods, sand casting and permanent mold casting are two of the most widely used techniques. While both processes aim to produce high-quality metal components, they differ significantly in terms of materials used, production methodologies, cost implications, and typical applications. Understanding these differences can help manufacturers choose the most suitable casting technique for their specific needs.
Sand Casting Overview
Sand casting, as the name implies, utilizes sand as the mold material. This technique involves creating a mold by compacting sand around a pattern that reflects the shape of the desired part. Once the pattern is removed, molten metal is poured into the sand mold, where it solidifies and takes the shape of the cavity.
One of the main advantages of sand casting is its versatility. It can accommodate a variety of metals, including iron, aluminum, and bronze, making it suitable for producing intricate shapes and large parts. Moreover, sand casting molds can be created quickly and inexpensively, especially for low to medium production runs.
However, sand casting also has some disadvantages. The surface finish of sand-cast parts is typically rough and may require additional machining to achieve a smoother finish. Additionally, the tolerance levels in sand casting are not as tight as those achievable with other casting methods, leading to potential variances in dimensional accuracy.
Permanent Mold Casting Overview
In contrast, permanent mold casting involves the use of reusable metal molds, typically made from alloys like aluminum or steel. This method starts with pre-made molds that are precisely machined to create a specific shape. The molds are then coated with a release agent to facilitate the easy removal of the cast part. Afterward, molten metal is poured into the mold cavity, where it cools and solidifies to form the desired piece.
Permanent mold casting offers significant advantages over sand casting, particularly in terms of surface finish and dimensional accuracy. The molds can produce parts with smoother surfaces and tighter tolerances, significantly reducing the need for further machining. Additionally, because the molds are reusable, this method is more cost-effective in high-volume production scenarios, leading to reduced per-unit costs over time.
difference between sand casting and permanent mold casting
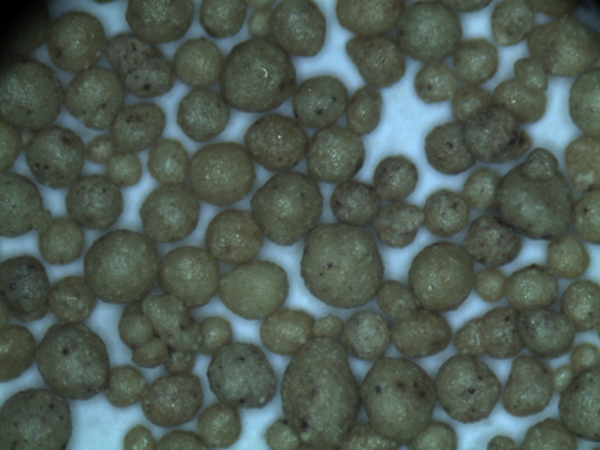
However, there are certain limitations to permanent mold casting. The initial cost of creating metal molds is generally higher compared to sand molds, making this method less economical for small production runs. Furthermore, the types of materials that can be used are more limited; permanent mold casting is mostly suitable for aluminum, zinc, and magnesium, which may restrict its use in applications requiring diverse metals.
Key Differences
1. Mold Material Sand casting utilizes expendable sand molds, while permanent mold casting uses durable metal molds that can be reused multiple times.
2. Surface Finish and Accuracy Parts produced through permanent mold casting typically have a better surface finish and more precise tolerances compared to those made via sand casting.
3. Production Volume Sand casting is more advantageous for low to medium production runs due to its lower initial costs, whereas permanent mold casting is more suitable for high-volume production because of the longevity of the molds.
4. Material Compatibility Sand casting is versatile in terms of materials, allowing a wide array of metals to be used, whereas permanent mold casting is generally confined to non-ferrous metals.
5. Cost Implications The initial cost of setting up a permanent mold casting operation is higher due to the need for creating metal molds, while sand casting can be more cost-effective for shorter runs.
Conclusion
In summary, both sand casting and permanent mold casting are valuable techniques in the field of manufacturing, each with its own set of advantages and limitations. Sand casting is ideal for producing large parts and complex geometries with a variety of metals, particularly when lower production volumes are required. On the other hand, permanent mold casting shines in high-volume production scenarios where surface quality and dimensional accuracy are critical. Understanding these differences allows manufacturers to make informed decisions that best meet their production requirements and budget constraints, ultimately leading to more efficient and effective manufacturing processes.
Post time:Սպտ . 28, 2024 16:30
Next:The Evolution and Significance of Sand Casting in Metalworking History