Differences Between Sand Casting and Permanent Mold Casting
Casting is a fundamental manufacturing process used to create metal parts and components with complex shapes. Among the various casting techniques, sand casting and permanent mold casting are two of the most commonly utilized methods. While both processes serve the same purpose of shaping molten metal, they have distinct characteristics, advantages, and drawbacks that make them suitable for different applications. This article will explore the key differences between sand casting and permanent mold casting.
Process Overview
Sand casting is a versatile method that involves creating a mold out of sand and a bonding agent, usually clay. The sand is packed around a pattern, which is a replica of the object to be cast. Once the mold is formed, the pattern is removed, and molten metal is poured into the cavity. After cooling, the mold is broken away to reveal the finished part. Sand casting is often favored for its ability to produce large and complex shapes, and it can accommodate a variety of metal types.
In contrast, permanent mold casting utilizes metal molds, typically made of iron or steel. These molds are designed to be reusable, making the process more efficient for producing high-volume parts. The metal mold is preheated and coated with a release agent to facilitate the removal of the cast part. Molten metal is then poured into the mold, and after solidification, the mold is opened to extract the finished product. This method is particularly advantageous for producing parts with good surface finish and dimensional accuracy.
Material and Cost Considerations
One significant difference between the two processes lies in the materials used. Sand casting is often more economical for lower production volumes, as the sand molds are relatively inexpensive and can be created quickly. However, the sand molds have limitations in terms of surface finish and durability, as they are suitable for only a limited number of pours before needing replacement.
difference between sand casting and permanent mold casting
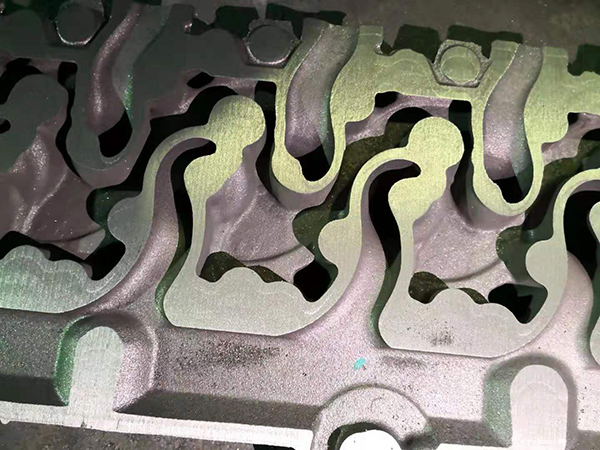
Permanent mold casting, on the other hand, involves higher upfront costs due to the fabrication of the metal molds. However, since these molds can be used repeatedly, the cost per part decreases with higher production volumes. Additionally, permanent molds can produce components with a smooth surface finish and tighter tolerances compared to sand casting, making them ideal for applications where precision is critical.
Applications and Suitability
The choice between sand casting and permanent mold casting also depends on the specific application requirements. Sand casting is widely used in industries such as automotive, aerospace, and art, where complex shapes and larger sizes are often required. It is especially effective for low to medium production runs where design adaptability is paramount.
Permanent mold casting is typically employed in industries needing consistent quality and precision, such as in the production of small to medium-sized components for appliances, automotive parts, and various machinery. Its ability to produce identical parts in large quantities makes it ideal for mass production.
Conclusion
In summary, both sand casting and permanent mold casting have unique advantages and are suited for different manufacturing needs. Sand casting offers flexibility and cost-effectiveness for low-volume and complex designs, while permanent mold casting excels in producing high-quality, precise parts in larger volumes. Understanding these differences helps manufacturers select the appropriate method for their specific applications, ensuring optimal performance and cost-efficiency.
Post time:Հկտ . 31, 2024 11:02
Next:rapid sand casting