Understanding Sand Casting Manufacturers
In the world of manufacturing, sand casting remains one of the oldest and most widely used methods for producing metal components. This process involves creating a mold from sand, which is then filled with molten metal to form a solid object. The versatility of sand casting has made it a preferred choice in various industries, including automotive, aerospace, and construction. As the demand for precise and high-quality components continues to grow, the role of sand casting manufacturers becomes increasingly critical.
The Sand Casting Process
The sand casting process typically begins with the creation of a mold. Manufacturers mix sand with a bonding agent—most commonly clay—and water to form a sand mixture that holds its shape. The mold is shaped to match the specifications of the desired part. This can involve creating cores for hollow sections or intricate designs.
Once the mold is prepared, it is filled with molten metal, usually aluminum, iron, or steel. After the metal cools and solidifies, the mold is broken apart to reveal the finished product. This method allows for the production of complex shapes and sizes, making it incredibly versatile.
Advantages of Sand Casting
One of the primary advantages of sand casting is its cost-effectiveness. The raw materials used, primarily sand and metal, are relatively inexpensive compared to other manufacturing methods. Additionally, the equipment involved, while requiring precise craftsmanship, is generally less costly to acquire and maintain than machinery for processes like die casting or investment casting.
Sand casting also allows for high flexibility in terms of design. Manufacturers can easily adapt their molds to accommodate specific customer requirements or design changes. This adaptability is particularly beneficial for industries that may require low-volume production runs of specialized components.
Additionally, sand casting can produce parts of various sizes, from small components used in electronics to large machine parts or even automotive frames
. This capability ensures that manufacturers can cater to a wide range of industries and applications.Challenges Faced by Sand Casting Manufacturers
sand casting manufacturers
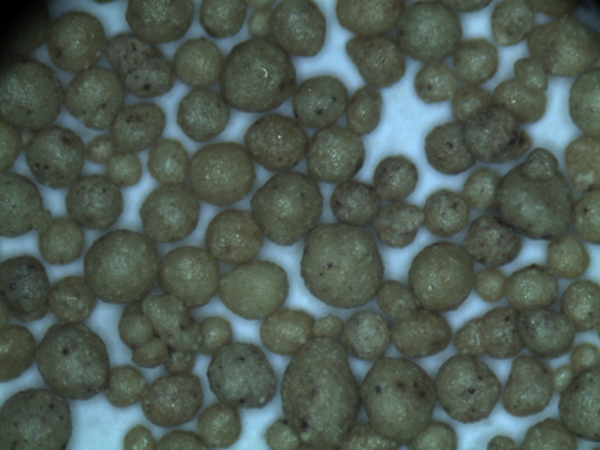
Despite its many advantages, sand casting does present some challenges. One major issue is the surface finish of cast parts. Compared to processes like die casting, sand casting typically results in a rougher surface, which may require additional finishing work, such as grinding or machining. This requirement can increase production time and costs, especially for high-precision applications.
Another challenge is the potential for defects within the cast parts. Issues such as porosity, sand inclusion, and misalignment can occur, affecting the structural integrity and functionality of the finished product. To mitigate these risks, manufacturers must invest in quality control measures and utilize skilled personnel to oversee the casting process.
Technological Advancements in Sand Casting
In response to the challenges faced by traditional sand casting methods, manufacturers are embracing technological advancements. One of the most significant innovations is the incorporation of computer-aided design (CAD) software, which allows for precise modeling of the parts. This technology aids in identifying potential issues before the casting process begins, thereby reducing the risk of defects.
3D printing technology is also making its mark in sand casting. Some manufacturers now use 3D-printed molds made from sand or polymer materials. This method not only speeds up the production process but also allows for the creation of more intricate designs that would be challenging to achieve with traditional methods.
The Future of Sand Casting Manufacturing
As industries continue to evolve, the future of sand casting manufacturing appears promising. The continual push toward sustainable practices is leading manufacturers to explore environmentally-friendly materials and processes. For instance, the development of synthetic sands and biodegradable binders can help reduce the environmental impact of traditional sand casting.
Moreover, the demand for custom, low-volume production will likely continue to grow, resulting in increased reliance on sand casting. Manufacturers who adapt to technological changes and focus on quality control will remain competitive in a continually developing market.
In conclusion, sand casting manufacturers play a vital role in the manufacturing industry, providing a reliable process for creating complex metal components. As challenges persist, the adoption of modern technologies and sustainable practices will not only enhance the efficiency of sand casting but also ensure its relevance in the future industrial landscape.
Post time:nov . 15, 2024 20:32
Next:ceramic sanding discs