Resin Bonded Sand Casting A Comprehensive Overview
Resin bonded sand casting is a modern method in the foundry industry that has gained significant popularity due to its ability to produce high-quality castings with intricate details and excellent surface finishes. This process combines traditional sand casting techniques with the use of synthetic resins to bind sand grains together, creating a mold that retains its shape even at elevated temperatures, thus providing distinct advantages over conventional sand casting.
The primary components of resin bonded sand casting include sand, a synthetic resin (typically phenolic resin), and a hardening agent. The first step in the process involves mixing the sand with the resin in precise ratios. The resin acts as a binder, ensuring that the sand grains adhere to one another. Once the mixture is prepared, it is formed into patterns or molds, often using a process called no-bake or cold-box methods. In the no-bake technique, the hardened sand mold is created by allowing the mixture to cure at room temperature, whereas the cold-box method involves using a chemical reaction initiated by heated air to cure the resin, resulting in faster mold production.
One of the key advantages of resin bonded sand casting is the ability to produce complex geometries. The versatility of the process allows for the manufacturing of intricate shapes that would be challenging to achieve with traditional casting methods. This peculiarity makes it exceptionally suitable for applications in industries ranging from aerospace to automotive, where precision and detail are paramount.
resin bonded sand casting
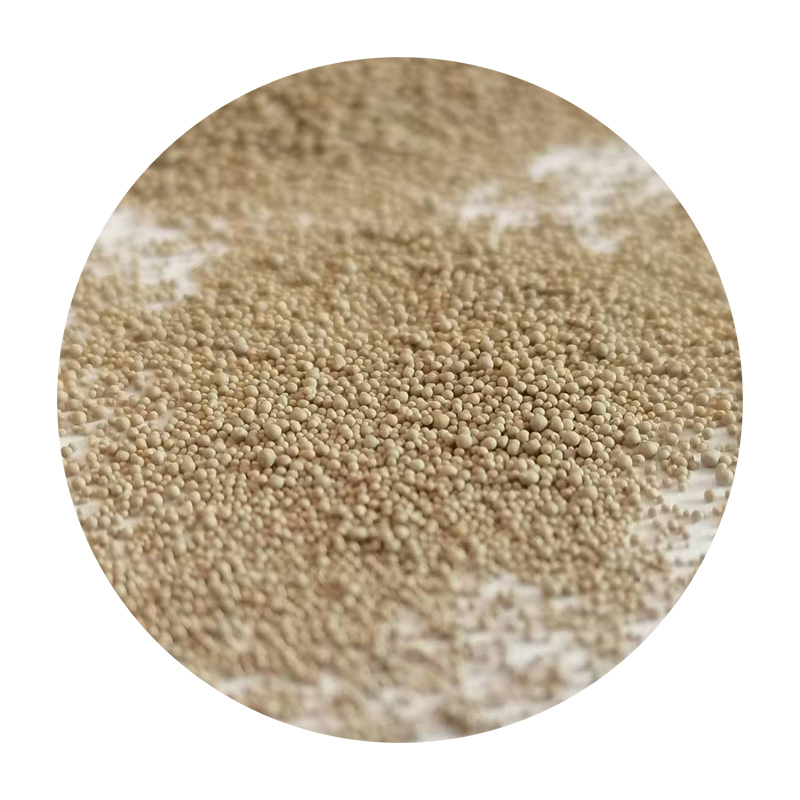
Additionally, the use of resin bonded sand leads to a superior surface finish compared to that obtained from traditional green sand casting. The molds typically have a smoother texture, which reduces the need for extensive post-casting machining. This not only shortens production times but also conveys cost savings by minimizing material waste and labor.
Another benefit of this casting method is its strength and durability. The resin bonded mold can withstand higher temperatures than traditional sand molds, making it suitable for casting a wider variety of metals and alloys, including those with higher melting points. This capability expands the range of potential applications and allows for greater flexibility in material selection.
Despite its advantages, resin bonded sand casting is not without challenges. The process can be more expensive upfront than green sand casting due to the costs associated with synthetic resins and their handling. Additionally, the environmental impact must be considered, as the curing agents and resins can emit volatile organic compounds (VOCs). As a result, many foundries are exploring eco-friendly alternatives and improved waste management practices to mitigate these concerns.
In conclusion, resin bonded sand casting represents a significant advancement in foundry technology. Its ability to produce high-precision and intricate castings makes it a preferred choice in various sectors that require quality and efficiency. As industries continue to evolve and demand more from their manufacturing processes, the resin bonded sand casting method is likely to remain a vital technique, adapting to meet both technological advancements and environmental concerns. By balancing innovation with sustainability, the foundry industry can harness the full potential of this casting method for future applications.
Post time:szept . 04, 2024 14:43
Next:Lost Foam Casting Method