Understanding the Cost of Sand Casting
Sand casting is a widely used manufacturing process that involves pouring molten metal into a sand mold to create a desired shape. This versatile method is popular in industries such as automotive, aerospace, and construction due to its ability to produce complex and large-sized components. However, like any manufacturing process, the cost associated with sand casting can vary significantly based on several factors. In this article, we will explore the various elements that contribute to the overall cost of sand casting.
1. Material Costs
One of the most significant factors influencing the cost of sand casting is the cost of raw materials. The type of metal being used—such as aluminum, steel, or iron—will greatly affect the price. For instance, aluminum is generally more expensive than iron, which can increase the overall cost of the casting. Additionally, the quality of the sand and any additives used (such as binders or coatings) also play a significant role in material costs. Higher-quality materials may lead to better surface finishes and dimensional accuracy, but they come at a price.
2. Pattern Costs
The creation of patterns, which are replicas of the final product used in the sand mold, is another critical cost element in sand casting. Patterns can be made from various materials, including wood, metal, or plastic, and their complexity can significantly affect costs. A simple pattern may be relatively inexpensive, while more complex designs may require advanced fabrication techniques and therefore incur higher costs. Additionally, the number of patterns needed for mass production will also impact the overall costs; for lower production volumes, the cost per unit can be much higher.
3. Labor Costs
Labor is another prominent factor in the cost of sand casting. This includes not only the wages of the workers who will construct the molds and operate the castings but also the skilled labor required for pattern making and finishing processes. Higher labor wages in certain regions or countries can contribute to increased overall costs. Moreover, if the sand casting process involves specialized skills or techniques, the labor costs may further escalate.
how much does sand casting cost
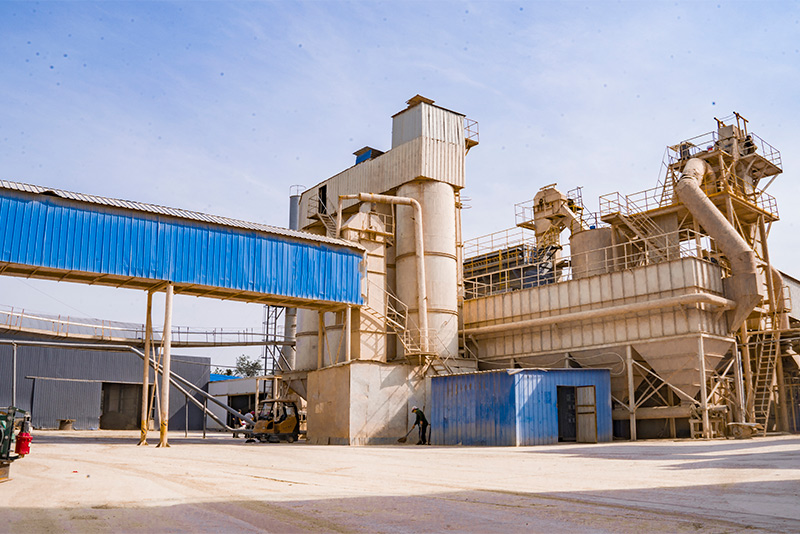
4. Equipment and Overhead Costs
The investment in equipment required for sand casting also contributes to the final cost. This includes melt furnaces, sand mixers, molding machines, and finishing equipment. For foundries, overhead costs like maintenance, utilities, and facility rent can add to the expense of the casting process, further influencing the price of the final product. Foundries with state-of-the-art technologies may charge higher prices due to lower production times and improved quality, which can lead to greater efficiencies overall.
5. Production Volume
The scale of production significantly impacts the cost of sand casting. For larger production runs, the cost per unit typically decreases due to economies of scale. This means that while the initial costs of pattern making and setup may be high, the overall cost per piece can be much lower when producing large quantities. On the contrary, small production runs may lead to a higher cost per part due to the fixed costs being spread over fewer units.
6. Post-Casting Operations
Finally, post-casting operations such as machining, surface finishing, and quality control can add to the overall costs. Depending on the specifications of the final product, these processes can be labor-intensive and require additional materials or equipment, which will increase the final price.
Conclusion
In summary, the cost of sand casting can vary widely based on various factors, including material costs, pattern complexity, labor rates, equipment investments, production volume, and post-casting processes. Understanding these elements is crucial for manufacturers seeking to optimize their sand casting operations and manage costs effectively. Whether you are an industry professional, a business owner, or simply curious about manufacturing processes, grasping the intricacies of sand casting costs can provide valuable insights into budgeting and production planning.
Post time:dec . 05, 2024 16:47
Next:Sanding Techniques for Optimal Resin Casting Finishes