The Importance of Foundry Sands in Metal Casting
Foundry sands play a crucial role in the metal casting industry, serving as the primary material used to create molds for metal casting processes. The demand for high-quality castings in automotive, aerospace, and construction industries has spurred significant advancements in foundry sand technology and its effective utilization. This article explores the types of foundry sands, their properties, applications, and the environmental considerations surrounding their use.
Types of Foundry Sands
The two most commonly used types of foundry sands are silica sand and synthetic sand. Silica sand, comprising primarily silica (SiO2), is valued for its high melting point, thermal stability, and ability to retain fine details in castings. It is mined from naturally occurring deposits and is processed to achieve the desired grain size and shape. On the other hand, synthetic sands are engineered materials, often made from minerals like zircon, olivine, or ceramic materials. These sands are designed to meet specific performance characteristics, such as improved thermal stability or reduced environmental impact.
Another category worth mentioning is reclaimed foundry sand, which is sand that has been used in previous casting processes and has been treated for reuse. The recycling of foundry sands not only reduces production costs but also minimizes environmental impact, making it an increasingly attractive option for foundries.
Properties of Foundry Sands
The efficiency of foundry sands is determined by several key properties, including grain size, shape, and purity. Grain size affects the mold's ability to withstand heat and pressure during the casting process. Smaller grain sizes provide finer details, while larger grains tend to improve the sand's strength and durability. The shape of the grains—round, angular, or irregular—also influences the mold's performance, with round grains generally providing better flowability and compactability.
Purity is another critical property, as impurities can adversely affect the final casting quality. High-purity sands are essential to produce castings with optimal surface finish and dimensional accuracy. Moreover, the chemical composition of the sand can impact the casting's physical properties, necessitating careful selection based on the specific requirements of the metal being cast.
foundry sands
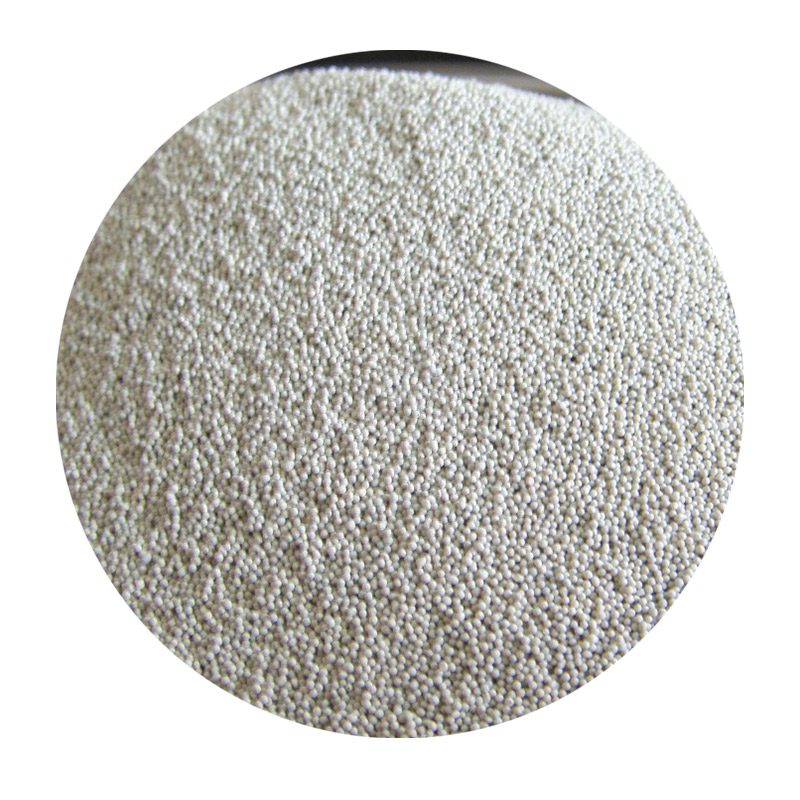
Applications of Foundry Sands
Foundry sands are predominantly used in the production of ferrous and non-ferrous castings. In iron and steel casting, silica sand provides excellent strength and thermal stability, making it ideal for producing heavy machinery components and automotive parts. In the aerospace industry, where precision is paramount, the use of high-quality synthetic sands ensures that castings meet strict tolerances and performance standards.
Additionally, foundry sands are employed in various casting methodologies, such as green sand casting, resin-bonded sand casting, and lost foam casting. Each method has its own advantages, and the choice of foundry sand greatly influences the overall efficiency and success of the casting process.
Environmental Considerations
With growing concerns over environmental sustainability, the foundry industry has been exploring ways to minimize the ecological impact of sand extraction and usage. The reclamation and reuse of foundry sand have become prominent practices, aiming to divert waste from landfills and reduce the demand for virgin sand.
Furthermore, the industry is actively researching eco-friendly alternatives to traditional foundry sands. For instance, the use of waste materials, such as crushed glass or recycled ceramics, is gaining traction as potential substitutes. These innovations not only help reduce the environmental footprint but also promote a circular economy within the casting industry.
Conclusion
Foundry sands are indispensable to the metal casting process, influencing the quality and efficiency of produced castings. As industries evolve, so too will the materials and methods used in casting, with a focus on sustainable practices that support environmental stewardship while meeting the high demands of modern manufacturing. Through technological advancements and innovative applications, foundry sands will continue to play a pivotal role in the future of the casting industry.
Post time:szept . 29, 2024 05:36
Next:Utilization of Foundry Sand as a Sustainable Material in Concrete Applications