The Essential Role of Casting Sand Suppliers in the Foundry Industry
Casting sand, a crucial material in the foundry industry, enables the production of metal parts through various casting methods. Foundries rely heavily on the quality and availability of casting sand to ensure the integrity and performance of the products they create. In this context, casting sand suppliers play a vital role in providing the necessary materials and services that meet the specific needs of foundries.
Types of Casting Sand
There are several types of sand used in the casting process, each serving distinct functions based on the requirements of the casting operation. The most common types include
1. Silica Sand This is the most prevalent sand used in the foundry industry due to its high melting point and excellent thermal properties. It is ideal for making molds and cores, as it can withstand the intense heat generated during metal pouring.
2. Green Sand A mixture of silica sand, clay, and water, green sand is used for its ability to retain moisture, which helps in creating molds that can withstand the weight of molten metal. It is popular for its cost-effectiveness and reusability.
3. Resin Sand Unlike traditional green sand, resin sand utilizes a synthetic resin as a bonding agent. This type of sand is suitable for precision casting and provides better surface finishes and dimensional accuracy.
4. Investment Sand This is used in investment casting processes where patterns are coated with sand. The sand is often made from fine silica, which produces smooth finishes and intricate designs.
The Supplier's Influence
casting sand suppliers
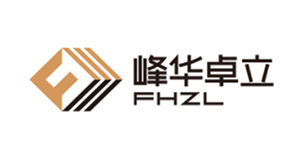
With various types of casting sand available, the role of suppliers is paramount. They are responsible for sourcing high-quality sand, processing it according to specifications, and ensuring it reaches foundries in a timely manner. The relationship between foundries and their suppliers can have a significant impact on the overall quality of the cast products.
Quality Assurance
Quality is fundamental in the casting process, as impurities or inconsistent grain sizes can lead to defects in the final product. A reputable casting sand supplier will conduct rigorous quality assurance tests to ensure that their sand meets industry standards. This includes checking for grain size distribution, purity levels, and moisture content. By ensuring high-quality materials, suppliers help foundries minimize defects and reduce costs associated with rework or scrap metal.
Custom Solutions
Every foundry has unique requirements based on the types of metal being cast, the complexity of the designs, and production volumes. Casting sand suppliers often work closely with foundries to provide tailored solutions that meet specific demands. This can include custom blends of sand, additives to enhance performance, or specialized processing techniques. By offering personalized service, suppliers can help foundries optimize their processes and improve overall efficiency.
Sustainability Concerns
In recent years, the foundry industry has faced increasing pressure to adopt sustainable practices. Casting sand suppliers are also responding to this trend by providing eco-friendly alternatives and promoting recycling of used sand. Initiatives such as sand reclamation processes help reduce environmental impact and minimize waste, showcasing the supplier's commitment to sustainability.
Conclusion
Casting sand suppliers are indispensable partners in the foundry industry, contributing not only high-quality materials but also expertise and customized solutions. As foundries continue to evolve, the demand for improved casting processes and sustainable practices will only grow. Working closely with reliable casting sand suppliers will empower foundries to produce superior metal components while navigating the challenges of a competitive and environmentally conscious market. In a landscape where quality and efficiency are paramount, investing in a strong partnership with a trusted casting sand supplier can make all the difference.
Post time:okt . 14, 2024 01:25
Next:Guide to Properly Sanding Your 3D Prints for a Smooth Finish