The Art and Science of Sanding Glazed Ceramics
Glazed ceramics are a beautiful expression of artistry and craftsmanship, often used in functional items like tableware, decorative pieces, and tiles. One crucial aspect of working with glazed ceramics is the process of sanding, which although seemingly counterintuitive, serves multiple important functions. This article explores the significance of sanding glazed ceramics, the techniques involved, and the outcomes one can achieve through this process.
Understanding Glazed Ceramics
Before diving into sanding, it’s important to understand what glazed ceramics are. Glazing involves applying a glassy coating to clay objects, which not only enhances their visual appeal but also adds a layer of protection. The glaze can be colored and can come in a variety of finishes, from matte to high gloss. However, glazing can also create a surface that, while visually stunning, may have imperfections, such as bumps, drips, or unevenness.
These imperfections can detract from both aesthetics and functionality. That's where sanding comes into play. It's a method used to smooth out these irregularities, ensuring a more professional finish and enhancing the overall quality of the ceramic piece.
The Sanding Process
Sanding glazed ceramics is a meticulous process that requires the right approach and tools. Here is a step-by-step guide on how to effectively sand glazed ceramics
1. Assess the Surface Begin by examining the glazed surface for imperfections. Look for uneven spots, sharp edges, or drips. This inspection will help you determine which areas require more attention.
2. Choose the Right Tools A variety of sanding tools are available, but the most common for glazed ceramics include fine-grit sandpaper (between 400 to 1200 grit), sanding sponges, and even specialized sanding pads designed for ceramics. It’s essential to use fine-grit paper to avoid scratching or damaging the glaze.
sanding glazed ceramics
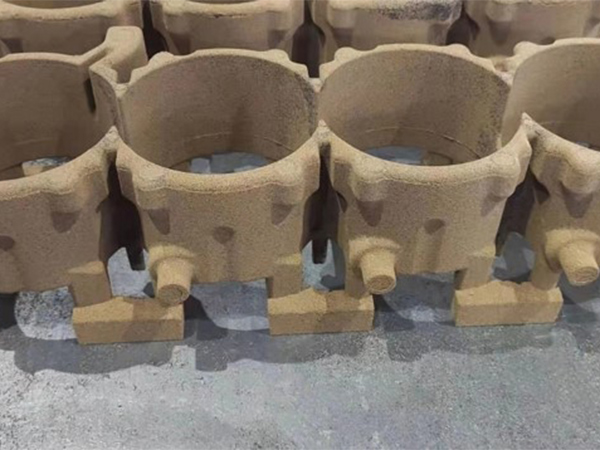
3. Prepare Your Workspace Ensure you’re working in a clean environment to prevent debris from scratching the surface during the sanding process. A steady hand and a well-lit workspace can make a significant difference in the outcome.
4. Begin Sanding Gently sand the glazed surface using circular motions. It’s crucial to apply light pressure, as too much force can break through the glaze and expose the clay body beneath. Sanding lightly allows you to gradually smooth the surface without compromising the integrity of the glaze.
5. Check Your Progress Periodically wipe away any dust created by sanding to assess the smoothness of the surface. This step is essential to avoid over-sanding and to achieve the desired finish.
6. Finishing Touches Once you've achieved the smoothness you desire, finish with an even finer grit sandpaper or a polishing pad to bring out the sheen in the glaze. If required, you may also follow up with a polishing compound suitable for glazed surfaces to enhance gloss.
Benefits of Sanding
Sanding not only improves the aesthetic qualities of glazed ceramics but also enhances practicality. Smoother surfaces are easier to clean, making them more functional for everyday use, especially in items like plates or bowls that may come into contact with food. Additionally, sanding can help prepare a surface for further glazing or painting, allowing for better adhesion and long-lasting results.
Conclusion
Sanding glazed ceramics is an essential practice for any ceramic artist or hobbyist looking to achieve a professional finish. While the process may seem counterproductive at first, the benefits it brings to the overall aesthetic and functional quality of the work are undeniable. With the right tools, techniques, and an eye for detail, sanding can elevate a ceramic piece from ordinary to extraordinary, highlighting the beauty of both the glaze and the underlying craftsmanship. Whether for functional or decorative purposes, understanding the art of sanding glazed ceramics is indispensable for anyone dedicated to this timeless craft.
Post time:Dec . 16, 2024 05:15
Next:Exploring the Sand Casting Foundry Process and Its Applications in Modern Manufacturing