Understanding Sand Casting A Key Process in Manufacturing
Sand casting is one of the oldest and most versatile manufacturing processes used in the metalworking industry today. This age-old technique can produce intricate shapes and components by pouring molten metal into a mold made of sand. In this article, we will explore the sand casting process, its advantages, applications, and the role of a sand casting factory in modern manufacturing.
The Sand Casting Process
The primary steps involved in sand casting include pattern making, mold preparation, pouring, and finishing. It begins with creating a pattern, which is a replica of the object to be cast. Patterns are typically made from materials like wood, metal, or plastic and are designed to be slightly larger than the final product to allow for metal shrinkage upon cooling.
Once the pattern is made, it is used to create a mold. This involves packing sand around the pattern to form a cavity that reflects the shape of the component. The sand used in this process is mixed with a binding agent and water to ensure that it retains its shape when the pattern is removed. After the mold is prepared, the pattern is taken out, and the two halves of the mold are put together.
Now, it's time to pour the molten metal into the mold cavity. The metal is heated in a furnace until it reaches a liquid state and is then poured through a gating system into the mold. After the metal cools and solidifies, the mold is broken apart to reveal the finished casting. The final step involves cleaning and finishing the part, which may include machining, grinding, or polishing to achieve the desired surface finish.
Advantages of Sand Casting
Sand casting offers several advantages that make it a popular choice for manufacturers. First and foremost, it can accommodate a wide range of metals and alloys, including iron, aluminum, and copper, making it adaptable for various applications. Additionally, it’s an economical process for producing both small and large quantities of parts, especially for complex shapes that might be challenging to create through other methods.
Another significant advantage of sand casting is its ability to create large components. Many industrial applications require parts that are large and robust, and sand casting can easily produce these while maintaining a high level of accuracy and surface detail. Furthermore, the sand used in casting can be reused multiple times, which helps reduce waste and lower production costs.
sand casting factory
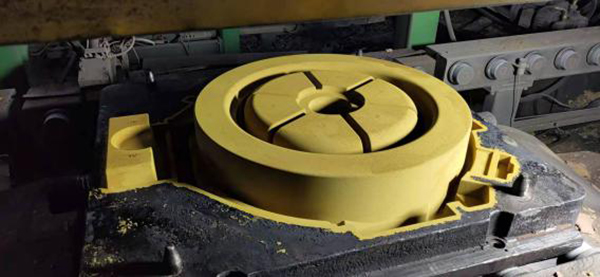
Applications of Sand Casting
Sand casting is utilized across a variety of industries. Automotive manufacturing, for instance, relies heavily on sand casting for engine blocks, transmission cases, and other critical components. Aerospace, military, and agricultural sectors also benefit from sand castings for their machinery and equipment. The marine industry frequently employs sand casting to produce durable components for ships and submarines, showcasing the versatility of this method.
Additionally, sand casting is used in the creation of art and sculptures. Artists often use sand molds to cast unique pieces that showcase intricate designs and details, reflecting the creativity and potential of this manufacturing method.
The Role of a Sand Casting Factory
A sand casting factory specializes in conducting the entire casting process efficiently. These factories are equipped with advanced technologies and skilled personnel trained to handle each stage of production. From initial pattern making to final finishing processes, a professional sand casting factory ensures consistency and quality in their products.
Moreover, modern sand casting factories employ innovative techniques and materials to enhance the efficiency and sustainability of their operations. Automation and computer-aided design (CAD) have significantly improved precision and reduced lead times, allowing for quicker production cycles. Additionally, factories are increasingly focusing on environmentally friendly practices, such as using biodegradable binders in sand mixtures and recycling materials to minimize waste.
Conclusion
In conclusion, sand casting remains a vital process in the manufacturing industry due to its flexibility, cost-effectiveness, and ability to produce complex shapes. As industries evolve and demand for efficient production methods increases, sand casting factories are adapting by embracing new technologies and sustainable practices. This timeless technique not only holds historical significance but continues to play a crucial role in modern manufacturing, producing high-quality components essential for various applications.
Post time:Dec . 25, 2024 23:43
Next:Evolution and Significance of Sand Casting in Industrial Applications Throughout History