Steps in Sand Casting
Sand casting, also known as sand mold casting, is one of the oldest and most widely used metal casting processes. It involves creating a mold out of sand to produce metal parts. This method is cost-effective and versatile, making it popular in various industries, from automotive to aerospace. Understanding the steps involved in sand casting is crucial for anyone interested in metalworking or manufacturing. Here, we will outline the primary steps involved in the sand casting process.
1. Pattern Making
The first step in the sand casting process is creating a pattern. A pattern is a replica of the object to be cast and is typically made from materials such as wood, metal, or plastic. The size of the pattern must account for shrinkage that occurs as the metal cools. Patterns can be one-piece or multi-part, depending on the complexity of the final product. Proper design and dimensional accuracy in pattern making are crucial, as they directly affect the quality of the final casting.
2. Sand Preparation
Once the pattern is ready, the next step involves preparing the sand mixture used to create the mold. Sand used in casting must have specific properties, including grain size, shape, and moisture content. A common mixture includes silica sand, clay, and water. The clay binds the sand particles together, while water helps to reduce dust and improve mold stability. The mixture must be carefully measured and mixed to ensure the production of a strong mold that can withstand the molten metal's pressure.
3
. MoldingAfter preparing the sand, the molding process begins. The pattern is first placed in a molding box or flask, and the sand mixture is packed around it to create a mold. This is often done in two halves, allowing the mold to be removed easily after it has formed. During this step, the sand must be tightly compacted around the pattern to ensure it retains its shape. After the sand is packed, any excess is removed, and the two halves of the mold are joined together. If necessary, additional features such as cores can be added to create internal cavities in the final casting.
4. Pouring
steps in sand casting
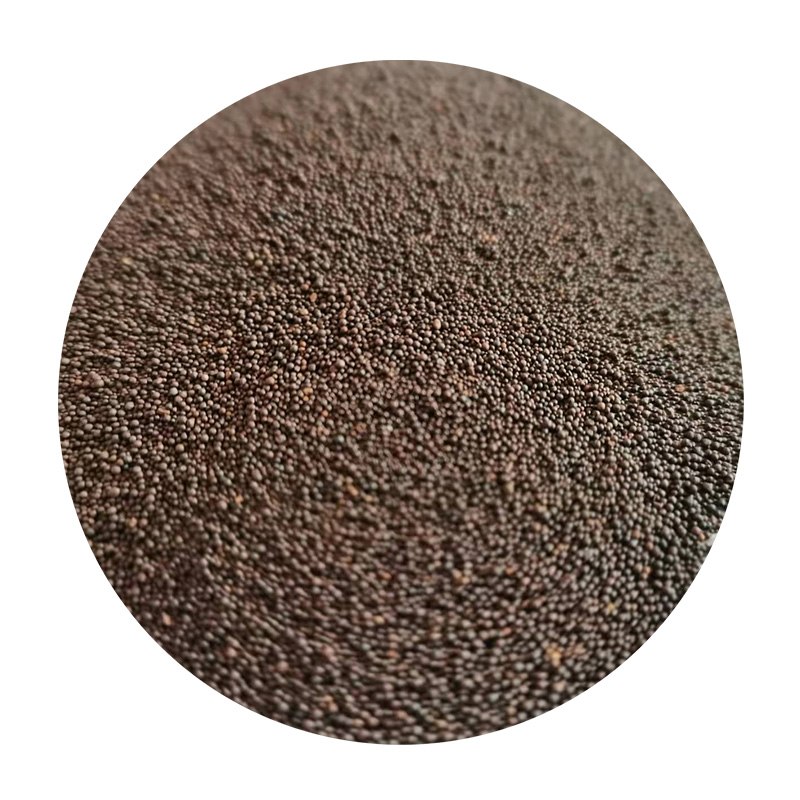
Once the mold is prepared and secured, the next step is pouring the molten metal into the mold cavity. The metal must be heated to a temperature high enough to ensure that it is in a liquid state, allowing it to flow easily into the mold. Pouring can be done by hand or with the help of automated machinery, depending on the production scale. It’s crucial to pour the metal steadily and in the correct direction to minimize turbulence, which can lead to defects in the final product.
5. Cooling
After the metal has been poured, it gradually cools and solidifies within the mold. The cooling time will vary depending on the part’s size, shape, and the type of metal used. Proper cooling is essential to ensure that the casting achieves the desired mechanical properties. Although the metal solidifies relatively quickly on the surface, the inner sections take longer, and care should be taken to allow the entire cast to cool uniformly to prevent warping and cracking.
6. Molding Removal
Once the metal has fully cooled and solidified, the mold can be broken open to reveal the casting. This step requires careful handling to avoid damaging the newly formed product. The sand is usually reusable, making sand casting environmentally friendly and cost-effective. Any sand or mold remnants stuck to the casting are cleaned off during this stage.
7. Finishing Touches
After the casting is removed, it often requires additional finishing work, such as grinding, sandblasting, or machining, to achieve the desired surface finish and dimensions. This final step helps remove any imperfections, ensure tight tolerances, and prepare the part for its intended application.
Conclusion
Sand casting is a fascinating and historical manufacturing process that continues to be relevant today. From creating patterns to finishing the final product, each step is critical for achieving high-quality castings. The versatility and cost-effectiveness of sand casting ensure its continued use in various industries, solidifying its significant place in modern manufacturing. Whether you are a hobbyist or a professional, understanding these steps can enhance your capabilities in metalworking and casting projects.
Post time:lis . 08, 2024 17:44
Next:Tips for Sanding Your 3D Prints to Achieve a Smooth Finish