Stainless Steel Sand Casting Foundry An Overview
Stainless steel sand casting is a vital manufacturing process that combines the ancient technique of sand casting with the modern requirements of producing high-quality stainless steel components. This method is widely utilized in various industries due to its versatility, cost-effectiveness, and ability to produce complex geometries that might be difficult to achieve with other casting techniques.
The Process of Stainless Steel Sand Casting
The stainless steel sand casting process involves several key steps. First, a mold is created from a mixture of sand, clay, and water. The sand is compacted around a pattern that reflects the desired shape of the final product. Once the pattern is removed, two halves of the mold are assembled, ready to receive molten stainless steel.
Next, high-grade stainless steel is melted in a furnace. The melting temperature required for stainless steel can exceed 1400°C (2552°F), emphasizing the need for specialized equipment and safety measures in the foundry. Once the steel is adequately molten, it is poured into the mold, where it fills the cavity and takes on the shape of the pattern.
After a cooling period, the mold is broken away, revealing the cast stainless steel part. The final step involves cleaning and finishing the cast piece, which may include processes like grinding, sanding, or polishing to achieve the desired surface finish and dimensional accuracy.
Advantages of Stainless Steel Sand Casting
stainless steel sand casting foundry
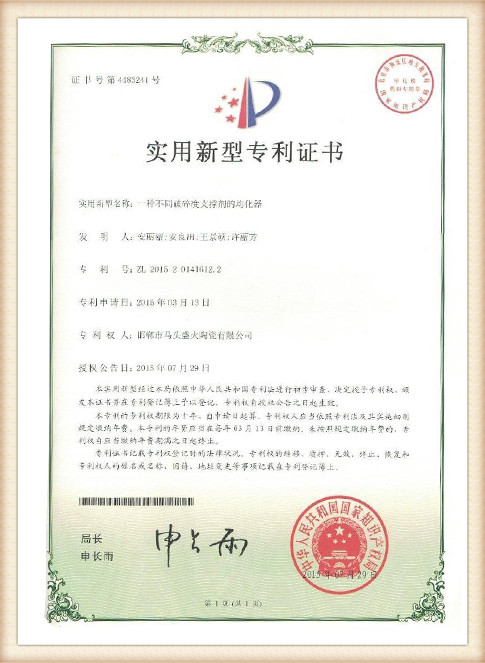
Stainless steel sand casting offers several advantages that make it a preferred choice in many applications. One of the primary benefits is its ability to produce complex shapes that would be challenging to manufacture using other methods. The flexibility of sand molds allows for intricate designs and features, catering to the specific needs of various industries, including aerospace, automotive, and marine sectors.
Another significant advantage is the cost-effectiveness of the process, particularly for low to moderate production volumes. The materials required for sand casting are relatively inexpensive compared to other casting methods, and the time taken to create molds is shorter, which helps reduce overall production costs.
Additionally, stainless steel is renowned for its durability, corrosion resistance, and aesthetic appeal. These properties are particularly beneficial in applications where strength and resistance to harsh environmental conditions are paramount. The ability to create parts with excellent surface finishes further enhances the appeal of stainless steel sand castings.
Applications of Stainless Steel Sand Castings
Due to its myriad benefits, stainless steel sand casting finds applications in numerous fields. Common uses include manufacturing valve bodies, pump housings, and various structural components. In the aerospace industry, precision-engineered components that can withstand extreme conditions are frequently produced using this method. The marine industry also relies on stainless steel sand casting for creating components subjected to harsh saltwater environments.
Conclusion
In conclusion, stainless steel sand casting is a dynamic and effective manufacturing process that has stood the test of time. Its ability to produce complex shapes efficiently and cost-effectively, combined with the inherent benefits of stainless steel, makes it a cornerstone of modern manufacturing. As industries continue to evolve, the demand for innovative casting solutions will likely increase, ensuring that stainless steel sand casting remains a critical player in the foundry landscape.
Post time:ruj . 25, 2024 17:32
Next:sand casting techniques