The Role of Sand in Foundry Processes
Sand has been a fundamental material in the field of foundry, playing a critical role in metal casting for centuries. Its unique properties make it an ideal medium for molding and shaping molten metal into various forms. This article delves into the significance of sand in foundry operations, detailing its types, properties, and applications.
Types of Sand Used in Foundries
Various types of sand are utilized in foundries, each possessing distinct characteristics suited for specific applications. The most common type is silica sand, primarily composed of silicon dioxide. This type of sand is highly valued for its thermal stability and ability to withstand high temperatures, making it suitable for creating molds that can endure the intense heat of molten metal.
Another popular option is olivine sand, which offers excellent refractoriness and is less prone to the environmental issues associated with silica dust. In addition, chromite sand is utilized for its high thermal conductivity and low expansion rate, making it ideal for high-performance metal casting.
Clay-bound sand, commonly known as green sand, is another type frequently used in foundries. It consists of sand mixed with clay and water, allowing it to retain moisture and providing a binding effect that helps shape the mold. This type of sand is favored for its ease of use and reusability, which significantly enhances production efficiency.
Properties of Foundry Sand
sand used in foundry
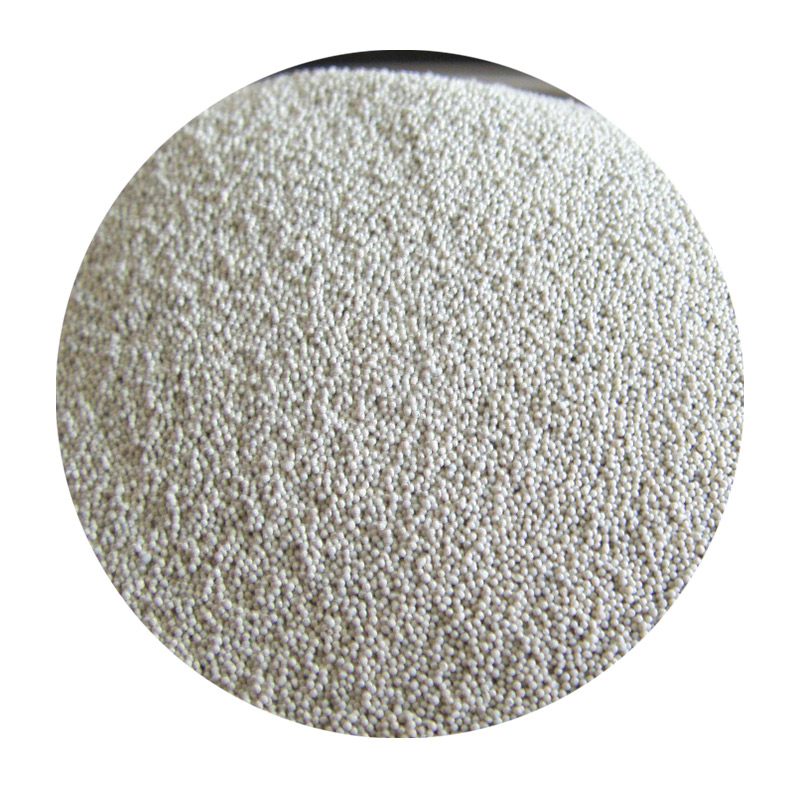
The properties of sand used in foundries are crucial to achieving quality castings. One of the essential properties is grain shape and size, which can influence the mold's strength and the quality of the final product. Angular grains provide better interlock and strength, while round grains offer superior flowability and ease of molding.
Thermal stability is another critical property, as the sand must withstand extreme temperatures without degrading. This characteristic ensures that the mold maintains its integrity during the metal pouring process. Additionally, the sand's permeability is vital to allow gases generated during the casting process to escape, preventing defects such as gas porosity.
The bonding ability of sand, particularly in clay-bound varieties, is also essential. The moisture content of the sand affects its bonding capacity, and maintaining the right balance is key to producing strong molds. Foundries often perform tests to regulate the sand's moisture and clay content to achieve optimal performance.
Applications in Metal Casting
Sand plays a pivotal role in various metalcasting applications, from producing automotive components to intricate artistic pieces. The process typically begins with creating a mold from sand, wherein the molten metal is poured. As the metal cools and solidifies, the mold is removed to reveal the cast object.
One significant advantage of sand molds is their versatility; they can be easily shaped and adapted for both large-scale industrial production and small-scale custom projects. Additionally, the ability to recycle sand after use enhances sustainability in foundry operations, as spent sand can be processed and reused multiple times.
In conclusion, sand is an indispensable element in the foundry industry, offering numerous advantages in metal casting processes. Its various types, unique properties, and applications underscore its importance in producing high-quality castings. As technology advances, the future of sand in foundries will likely evolve, incorporating innovations that enhance its performance and sustainability, ultimately contributing to more efficient and environmentally friendly manufacturing practices.
Post time:pro . 13, 2024 09:43
Next:Understanding the Process and Benefits of Sand Casting in Engineering Applications