Understanding Sand Cast Iron Properties, Applications, and Benefits
Sand casting is a widely used metal casting process that involves the creation of metal parts by pouring molten metal into a sand mold. Among various materials used in this process, cast iron holds a prominent position due to its excellent casting capabilities, mechanical properties, and versatility in applications. This article explores sand cast iron, discussing its composition, properties, applications, and the benefits it offers in various industries.
What is Sand Cast Iron?
Sand cast iron is a type of cast iron produced through the sand casting process, which involves the use of sand as a mold material. Cast iron itself is an alloy predominantly composed of iron, carbon (typically between 2% and 4%), and silicon (around 1% to 3%). The addition of other alloying elements such as manganese, sulfur, and phosphorus can enhance specific properties, tailoring the material for particular applications.
One of the most important types of cast iron is gray cast iron, which is characterized by its graphitic structure. This graphitization gives it a unique combination of strength, machinability, and wear resistance. Sand cast iron can also be found in other forms like ductile iron (also known as nodular iron) and white cast iron, each offering distinct advantages depending on their chemical composition and microstructure.
Properties of Sand Cast Iron
1. Excellent Castability One of the primary advantages of sand cast iron is its excellent fluidity and ability to fill intricate geometries. This property allows manufacturers to create complex shapes that are difficult or impossible to achieve with other manufacturing methods.
2. High Wear Resistance The presence of graphite in gray cast iron enhances its wear resistance. This quality makes sand cast iron particularly suitable for high-friction environments, such as in machinery and industrial applications.
sand cast iron
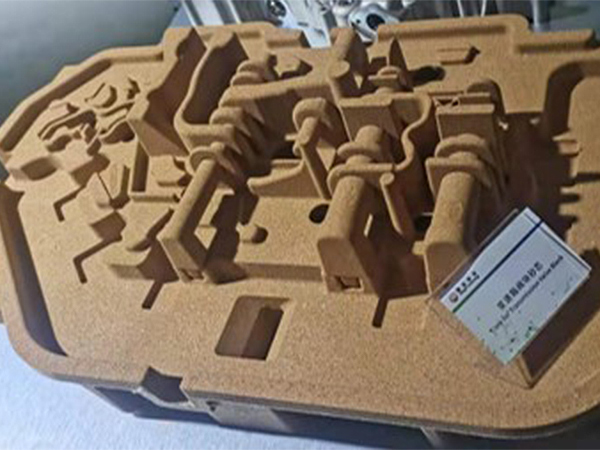
3. Good Damping Capacity Cast iron has superior vibration-damping properties compared to steel. This makes it an ideal material for applications requiring stability and minimal vibration transfer, such as machinery bases and engine blocks.
4. Machinability While it has a relatively high hardness, sand cast iron is also known for its machinability. It can be easily turned, milled, and drilled, enabling the production of high-precision components.
5. Corrosion Resistance Depending on the specific alloying elements present, cast iron can exhibit varying degrees of resistance to corrosion. Ductile iron, for example, has improved corrosion resistance compared to traditional gray cast iron.
Applications of Sand Cast Iron
Sand cast iron plays a critical role in numerous industries, including automotive, aerospace, construction, and manufacturing. Some common applications include
- Automotive Components Engine blocks, cylinder heads, and exhaust manifolds are often made from sand cast iron given its durability and heat resistance. - Pipes and Fittings Due to its strength and corrosion resistance, sand cast iron is commonly used in plumbing and drainage systems. - Machinery Parts Applications in industrial machinery include gears, housings, and base frames where vibration damping is essential. - Art and Sculpture The malleability of cast iron allows it to be used in artistic applications, creating intricate sculptures and decorative elements.
Conclusion
In summary, sand cast iron is a versatile and valuable material in various industries, thanks to its excellent castability, mechanical properties, and specific advantages like wear resistance and machinability. As technology evolves, the applications and benefits of sand cast iron continue to expand, making it an enduring choice for manufacturers worldwide.
Post time:pro . 13, 2024 17:24
Next:different types of foundry sand