Sand Casting Technology An Overview
Sand casting, one of the oldest and most versatile manufacturing processes in metalworking, has remained a fundamental technique for creating complex metal parts. Its simplicity and adaptability to a wide range of metals make it a preferred choice in various industries, including automotive, aerospace, and art.
The Process of Sand Casting
The sand casting process begins with the creation of a mold. Typically, a mixture of sand, clay, and water is used to produce a mold that can withstand the high temperatures of molten metal. The first step involves creating a pattern, usually made from metal, wood, or plastic, which mirrors the desired shape of the final product. This pattern is placed in sand to form a cavity, where the molten metal will solidify.
Once the pattern is removed, the mold is assembled and secured. The next step is pouring the molten metal into the mold cavity. After allowing sufficient time for the metal to cool and solidify, the mold is broken apart to reveal the cast metal part. This is followed by a cleaning process to remove any sand residues and imperfections from the surface.
Advantages of Sand Casting
One of the primary advantages of sand casting is its flexibility. It can accommodate a vast range of sizes, from small intricate components to large heavy parts. Additionally, sand casting is compatible with numerous metal alloys, including steel, iron, aluminum, and bronze, allowing manufacturers to select the most suitable material for their applications.
Another significant advantage is cost-effectiveness. The materials used to create molds, mainly sand, are inexpensive and readily available. This makes sand casting an economical option for both small-scale productions and large-scale manufacturing. Moreover, the sand used in the process can often be reused, further reducing costs and waste.
Limitations and Considerations
Despite its advantages, sand casting is not without limitations. One notable concern is the surface finish of the final product. Compared to other casting methods like die casting or investment casting, the surface quality of sand-cast items may require additional finishing treatments, which can add to production time and costs.
sand casting technology
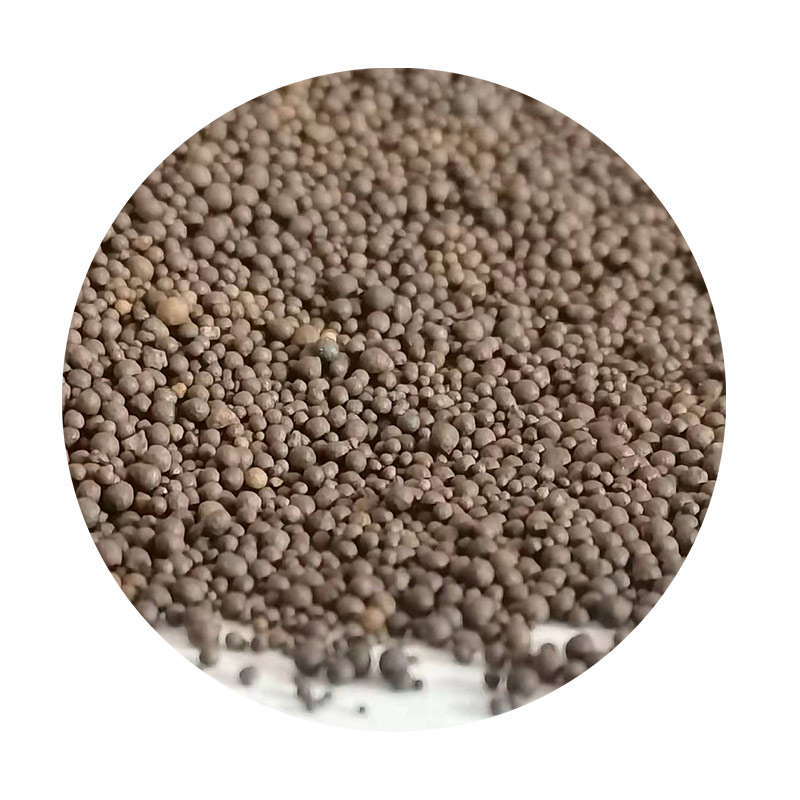
Dimensional accuracy is another challenge. While sand casting can produce parts with acceptable tolerances, it may not achieve the precision of other casting techniques. It is, therefore, crucial to assess the specific requirements of a project before deciding on sand casting as the preferred method.
Technological Advances
In recent years, advancements in technology have significantly improved sand casting processes. The introduction of computer-aided design (CAD) and computer-aided manufacturing (CAM) systems has enhanced the precision with which molds are created. This shift has resulted in better design adaptability, allowing engineers to explore more complex geometries without incurring prohibitive costs.
Moreover, developments in sand conditioning and mold-making techniques, including the use of 3D printing, have streamlined the sand casting process. These technologies enable faster production times, reduced labor costs, and improved mold quality, ultimately leading to better casting outcomes.
Future Perspectives
The future of sand casting appears promising, especially as industries seek more sustainable manufacturing practices. Recycling and reusing materials within the sand casting process aligns with the growing emphasis on environmentally friendly operations. Furthermore, the ongoing exploration of new materials and alloys broadens the scope of applications for sand casting technology.
Additionally, as the Internet of Things (IoT) and smart manufacturing continue to integrate into the industry, real-time monitoring and data analysis can further optimize sand casting operations. This transformation could lead to improved efficiency, reduced errors, and enhanced product quality.
Conclusion
In summary, sand casting technology remains a cornerstone of metal fabrication due to its versatility, cost-effectiveness, and adaptability. While it has its limitations, ongoing technological advancements are paving the way for a brighter future in sand casting. As industries continue to innovate and evolve, sand casting will undoubtedly hold its ground as a vital method for producing high-quality metal components.
Post time:pro . 15, 2024 04:05
Next:casting sand for sale