Understanding Sand Casting Technology
Sand casting, a versatile and widely used manufacturing process, has been pivotal in metalworking for centuries. This technique involves creating a mold from a sand mixture to produce metal components. As industries evolve, sand casting technology continues to adapt, making it an essential part of modern manufacturing.
At its core, sand casting begins with the creation of a mold. The most common material used is silica sand, which is mixed with a binding agent like clay to enhance its cohesiveness. The sand is compacted around a pattern, typically made from metal or plastic, that represents the final part’s shape. Once the mold is formed, it is split to remove the pattern, creating a cavity into which molten metal will be poured.
One of the significant advantages of sand casting is its flexibility. It can accommodate a wide range of metals, including aluminum, iron, and brass, making it suitable for various applications across different industries. This adaptability allows manufacturers to produce both simple and complex shapes efficiently. Additionally, large castings—often weighing several tons—can be produced, making sand casting a preferred choice for heavy machinery and automotive components.
sand casting technology
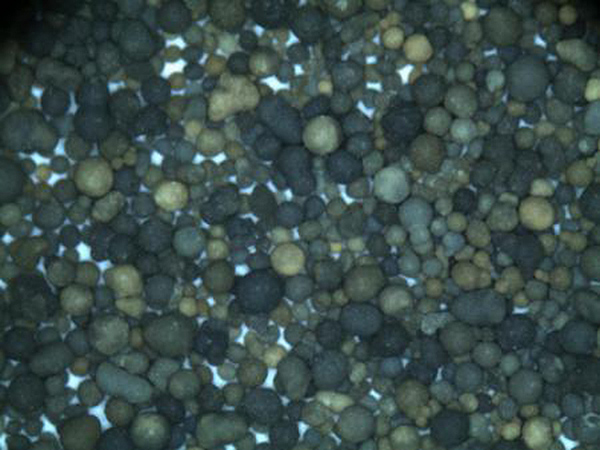
Another benefit of sand casting technology is its cost-effectiveness, especially for low-volume production. The initial investment in patterns and molds is relatively low compared to other manufacturing processes, such as injection molding. This aspect is particularly advantageous for startups or businesses looking to test new designs without committing significant resources upfront. Furthermore, the sand used in the process can often be reused, which contributes to a more sustainable production cycle.
Despite its many benefits, sand casting does have some limitations. The surface finish of sand-cast components may not be as smooth as parts produced through other processes like investment casting. This characteristic can be mitigated by additional machining or finishing processes, but it adds to the overall manufacturing time and cost. Additionally, achieving tight tolerances can be challenging in sand casting, making it less suitable for applications that require precision.
To address these challenges and enhance efficiency, advancements in technology have been integrated into the sand casting process. For instance, the introduction of computer-aided design (CAD) and computer-aided manufacturing (CAM) has streamlined the design and production phases, allowing for more precise mold designs and improved quality control. Moreover, automation in the sand preparation and mold-making processes has increased the repeatability and accuracy of castings, reducing human error and enhancing output.
In conclusion, sand casting technology remains a cornerstone of the metal casting industry due to its versatility, cost-effectiveness, and ability to produce large components. As technology continues to advance, sand casting is likely to retain its relevance by evolving with new methodologies that improve efficiency and product quality. Industries that harness the capabilities of sand casting can expect to see continued innovation and development, ensuring that this traditional technique remains vital in the modern manufacturing landscape.
Post time:lis . 01, 2024 18:44
Next:A Beginner's Guide to Sand Casting Techniques and Best Practices