Understanding the Sand Casting Foundry Process
Sand casting, one of the oldest and most versatile metal casting processes, is widely used in foundries to create complex shapes from molten metal
. This process utilizes sand, which is inexpensive and easy to mold, making it a popular choice in various industries, including automotive, aerospace, and art. In this article, we will delve into the sand casting foundry process, exploring its stages, advantages, and applications.The sand casting process begins with the preparation of a pattern, which is a replica of the final product to be manufactured. Patterns are typically made from materials such as wood, metal, or plastic. The choice of material depends on factors like the size of the cast, the production volume, and the required precision. The pattern is designed slightly larger than the final product to account for the shrinkage of the metal as it cools.
Once the pattern is ready, the next step involves creating a mold. This is done by tightly packing sand around the pattern in a mold box. The sand mixture usually contains silica sand, clay, and water to enhance its binding properties. After packing, the mold halves are carefully separated, and the pattern is removed, leaving a cavity that mirrors the shape of the intended casting. In more complex designs, cores made of sand may be added to create internal features.
After the mold is prepared, it undergoes a process called mold baking to improve strength and surface finish. This involves applying heat or adding resin to the sand to bind the grains together more effectively. Once the mold has hardened, it is ready for the pouring operation.
sand casting foundry process
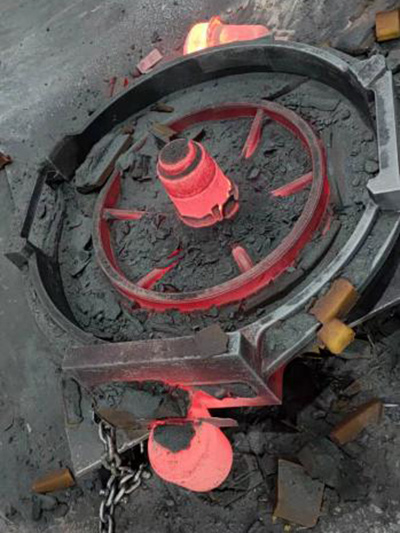
The next critical stage in the sand casting process is pouring the molten metal into the mold. The metal is typically heated in a furnace until it reaches a liquid state. Different types of metals can be used in sand casting, including aluminum, iron, and bronze. The choice of metal depends on the specific requirements of the casting, such as strength, weight, and corrosion resistance.
The molten metal is carefully poured through a pouring basin into the mold cavity. It is essential to control the pouring rate and temperature to avoid defects like porosity or misalignment. Once the mold is filled, the metal is allowed to cool and solidify. Cooling times vary depending on the size and thickness of the casting, but it is crucial for the integrity of the final product.
After the metal has cooled sufficiently, the next step is to break open the mold, a procedure that demands careful handling to prevent damage to the cast part. The casting is then removed, and any remaining sand is cleaned off. This stage often involves additional processes, such as grinding, sanding, or machining, to achieve the desired surface finish and dimensions.
The advantages of sand casting are numerous. It can accommodate large and heavy parts, offers excellent flexibility in design, and is cost-effective for low to medium production runs. Moreover, sand casting allows for the use of a variety of metals and alloys, making it suitable for a wide range of applications.
In conclusion, the sand casting foundry process epitomizes a combination of art and engineering. From pattern making to pouring molten metal, each step requires precision and expertise. With its adaptability and cost efficiency, sand casting continues to be a foundational method in manufacturing, underpinning the production of everything from intricate automotive components to artistic sculptures. As technology advances and new materials are developed, the sand casting process will likely evolve, remaining a vital part of the foundry industry for years to come.
Post time:lis . 10, 2024 14:41
Next:foundry sand meaning