The World of Sand Casting An Overview of the Sand Casting Factory
In the realm of manufacturing, one of the most ancient yet highly effective methods is sand casting. This process has been utilized for centuries to create complex metal shapes and structures, ranging from intricate engine components to robust industrial parts. A sand casting factory embodies the heart of this process, where skill, technology, and craftsmanship converge to produce high-quality castings.
Understanding Sand Casting
Sand casting, as the name suggests, utilizes sand as the primary molding material. The process begins with the creation of a mold, which is formed by packing a mixture of sand and a binding agent around a pattern. The pattern, typically made of metal or plastic, represents the final product to be cast. Once the mold is prepared, it is removed from the pattern, leaving a cavity that mirrors the desired shape of the component.
The next step involves pouring molten metal into the prepared mold. The metal, when cooled and solidified, takes on the shape of the cavity, resulting in a new cast piece. After the metal cools sufficiently, the sand mold is broken apart to retrieve the finished casting. This method offers a range of advantages, including versatility in material selection, the ability to create large or small parts, and a relatively low-cost production process.
Key Features of a Sand Casting Factory
A modern sand casting factory is equipped with advanced machinery and tools designed to streamline the casting process. From automated sand mixers to sophisticated pouring systems, technology plays a crucial role in enhancing efficiency and precision.
1. Molding Equipment High-quality molding machines are essential for creating consistent and accurate molds. These machines can automate the packing process, ensuring that the sand mixture is tightly compacted around the pattern. Advanced machines can even utilize computerized controls for improved precision.
sand casting factory
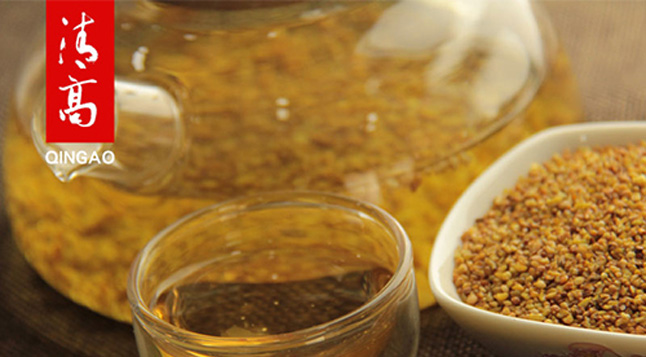
2. Melting Furnaces The melting process is a critical stage in sand casting. Factories employ various types of furnaces, such as induction or electric arc furnaces, which allow for precise temperature control and efficient metal melting. This ensures that the metal is poured at optimal temperatures, reducing defects and enhancing the quality of the casting.
3. Quality Control Quality assurance is paramount in a sand casting factory. After the casting is removed from the mold, it undergoes rigorous inspection processes. This may involve visual inspections, dimensional checks, and non-destructive testing methods to identify any flaws or weaknesses in the casting. Consistent quality is vital for maintaining customer trust and satisfaction.
4. Finishing Processes Once the casting has been validated, additional finishing processes are undertaken to achieve the desired surface quality. This might include grinding, sandblasting, or machining to remove any rough edges or imperfections. The finishing stage is critical not only for aesthetic purposes but also for ensuring that the component meets its functional requirements.
Environmental Considerations
In recent years, there has been a growing emphasis on sustainability within manufacturing industries, including sand casting. Modern sand casting factories are adopting eco-friendly practices, such as recycling sand molds and using environmentally friendly binders. These initiatives help minimize waste and reduce the environmental impact of casting operations.
Conclusion
The sand casting factory stands as a testament to human ingenuity and adaptability in the manufacturing sector. By blending traditional techniques with modern advancements, these factories continue to produce high-quality castings that support a diverse range of industries. As the demand for precision and efficiency grows in manufacturing, the role of sand casting factories is more crucial than ever. With ongoing innovations and a commitment to quality, the future of sand casting remains bright, promising new opportunities and advancements for the industry.
Post time:lis . 16, 2024 00:36
Next:buy sand casting