Properties of Foundry Sand An Essential Component in Metal Casting
Foundry sand is a critical material used in the metal casting industry, playing an integral role in the production of various metallic components. It is primarily silica sand that is specifically chosen and treated to ensure high-performance characteristics during the casting process. Understanding the properties of foundry sand is crucial for foundries to optimize their operations and improve the quality of the final products. This article will delve into the key properties of foundry sand that make it an indispensable asset in metal casting.
1. Grain Size Distribution
One of the foremost properties of foundry sand is its grain size distribution. The shape and size of the individual sand grains affect the mold's permeability and the surface finish of castings. Foundry sands typically have a grain size ranging from 0.1 mm to 0.55 mm. A well-graded sand will have a mixture of coarse and fine grains, which helps to achieve optimal packing density and produces molds that can withstand the thermal and mechanical stresses during casting. A finer grain size may enhance surface finish but could also lead to issues with mold strength and gas venting.
The strength of foundry sand is paramount to maintaining the integrity of the mold during the casting process. Mold strength refers to the ability of the sand mold to hold its shape under the pressure of molten metal. Foundry sands exhibit good compressive and tensile strength due to the bonding additives mixed with them, commonly composed of clay and resin. These additives enhance the sand’s structural integrity, enabling it to withstand high temperatures and mechanical stress without collapsing or deforming.
3. Thermal Conductivity
Thermal conductivity is another essential property of foundry sand. Good thermal conductivity is crucial for the efficient cooling of cast parts and the prevention of defects such as hot tears and shrinkage cavities. Foundry sand should be able to absorb and dissipate heat effectively to avoid thermal shock during the casting process. Silica sand has relatively high thermal resistance, which contributes to its ability to maintain mold stability at high temperatures.
properties of foundry sand
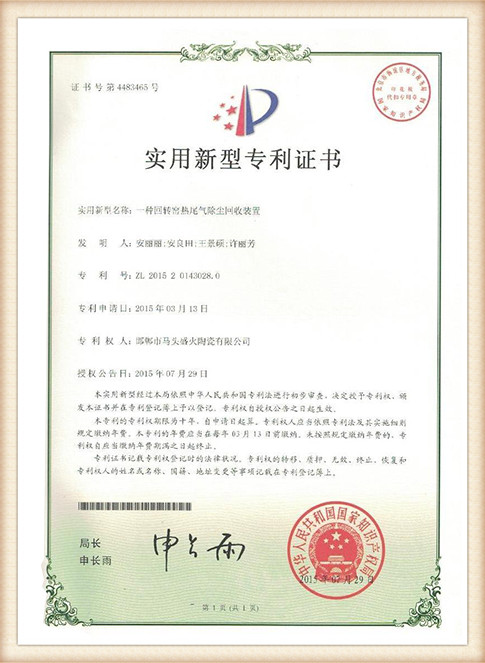
4. Permeability
Permeability is the property that allows gases generated during the casting process to escape from the mold. A high permeability ensures that any gases produced from the molten metal, as well as moisture from the sand, can escape without causing defects such as inclusions or blowholes in the casting. Foundry sands are typically treated to enhance their permeability while maintaining sufficient strength. The balance between strength and permeability is vital to achieving high-quality castings.
5. Reusability
An attractive property of foundry sand is its reusability. After casting, the sand can often be reclaimed and reused in the mold-making process. The reclamation process involves mechanically or thermally treating the used sand to remove any impurities and restore its desirable properties. Reusing foundry sand reduces the demand for virgin sand, thus lowering material costs and minimizing environmental impacts associated with sand extraction. This sustainability aspect is increasingly important in modern foundries.
6. Chemical Composition
The chemical composition of foundry sand, primarily consisting of silica (SiO2), can vary based on its source. However, the presence of impurities such as iron oxide, clay, and other minerals can significantly affect the casting quality. Foundry sands must be selected based on their chemical purity to ensure that they do not react adversely with the molten metal. High purity silica sands are preferred for many applications to minimize defects and achieve the desired metallurgical properties in the final product.
Conclusion
In summary, foundry sand possesses unique properties that are vital to the metal casting industry. Its grain size, strength, thermal conductivity, permeability, reusability, and chemical composition all contribute to the overall performance of casting molds. Understanding these properties allows foundries to optimize their processes, ensuring the production of high-quality metallic components while also promoting sustainable practices. As the industry continues to evolve, the role of foundry sand will undoubtedly remain critical in meeting the demands of modern metal casting applications.
Post time:lis . 16, 2024 23:09
Next:hydro super sand