Materials Used in Sand Casting
Sand casting is one of the oldest and most widely used metal casting processes, which involves the use of sand as the primary mold material. The versatility of sand casting allows for the production of complex shapes and large metal parts, making it a popular choice in industries like automotive, aerospace, and manufacturing. The effectiveness of the sand casting process largely depends on the careful selection of materials used in each step.
1. Sand as the Mold Material
The primary material used in sand casting is sand, typically a mixture of silica (SiO2) with different additives to improve performance. The two main types of sand used are green sand and resin-bonded sand. Green sand is a mixture of silica sand, clay, and water, which retains moisture. It allows for good moldability and collapsibility, making it easier to remove castings. On the other hand, resin-bonded sand involves mixing silica sand with a resin bonding agent, which hardens when heated. This type of sand allows for more precise molds and is particularly useful for intricate designs.
2. Additives and Binders
To enhance the properties of sand molds, a variety of additives and binders are used. Clay is the most common binder, particularly in green sand systems, as it helps the sand grains stick together and maintain the shape of the mold. Other additives like starch or resin may also be employed to enhance strength and improve casting quality. For instance, bentonite clay is frequently added to increase the plasticity of the sand mixture, providing better adaptability to complex shapes.
3. Metal Alloys
materials used in sand casting
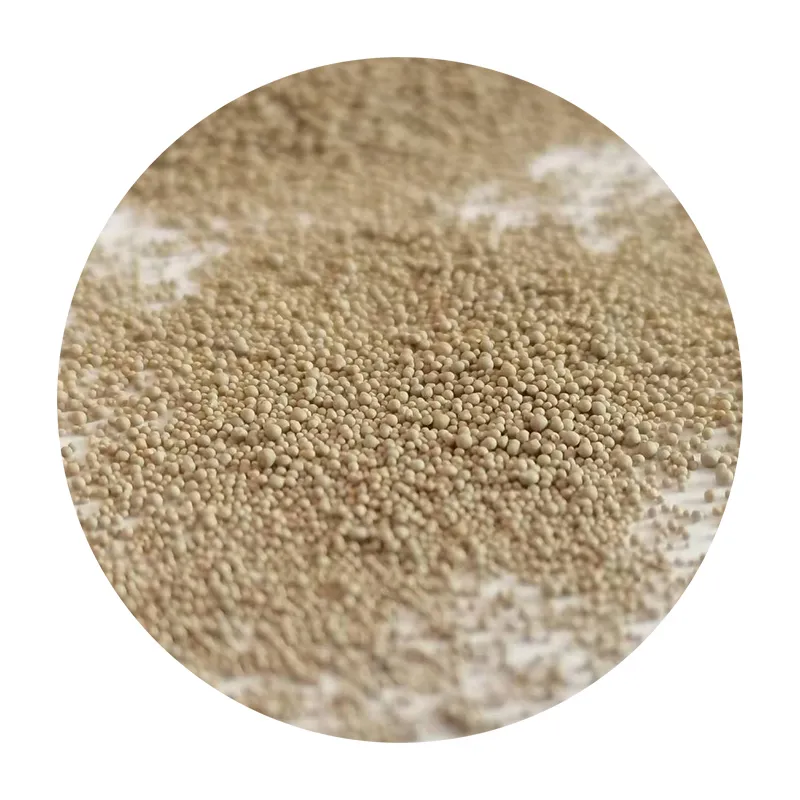
The choice of metal alloy is critical in sand casting. Common alloys include aluminum, iron, and bronze. Each metal has specific properties that make it suitable for different applications. Aluminum is lightweight, corrosion-resistant, and has excellent fluidity when molten, making it ideal for intricate castings. Cast iron, particularly gray cast iron, is known for its excellent wear resistance and machinability, which makes it a favorite in automotive applications. Bronze offers high strength and resistance to corrosion, making it suitable for parts exposed to harsh environments.
4. Coatings and Release Agents
To ensure smooth casting and easy removal of the finished product, coatings and release agents are applied to sand molds. These materials help prevent the molten metal from sticking to the mold, ensuring a clean release after cooling. Common release agents include oils and waxes, while coatings often contain ceramic materials that provide thermal insulation and reduce oxidation.
5. Additives for Improvement
In addition to the main components, several additives can be incorporated to modify the thermal conductivity, strength, and surface finish of the molds. For instance, graphite can be added for better thermal resistance, while various surface modifiers can improve the finish of the final product.
Conclusion
The materials used in sand casting play a pivotal role in determining the quality and performance of castings. By carefully selecting sand types, binders, metal alloys, and additional products such as coatings and release agents, manufacturers can optimize the sand casting process to meet specific requirements. This combination of materials ensures that sand casting remains a crucial technique in metalworking, capable of producing durable and complex components.
Post time:lis . 22, 2024 05:51
Next:Exploring the Benefits of Sand and Resin Combinations in Construction Materials