The Iron Sand Casting Process An Overview
Iron sand casting is a vital manufacturing process used to create intricate metal components for various applications, ranging from machinery parts to artistic sculptures. This method harnesses the unique properties of iron sands—grains of iron-rich minerals weathered down by natural forces—transforming them into high-quality cast products. In this article, we will explore the iron sand casting process, its advantages, and applications.
The Basics of Iron Sand Casting
The iron sand casting process begins with the collection of iron sand. This material is typically found along coastal regions or riverbeds, where it has accumulated over time. Once harvested, the iron sand undergoes a purification process to remove impurities and ensure a high percentage of iron content, which is essential for producing durable and reliable casts.
The next step involves creating a mold. Molds can be made from various materials, but in sand casting, they are primarily composed of sand mixed with a binding agent. The mixture is compacted around a pattern, which forms the shape of the final product. The pattern is usually made from metal or plastic and is designed to withstand the heat of molten iron without warping or degrading.
Once the mold is prepared, the next phase is to melt the iron sand. This is done in a furnace capable of reaching temperatures of up to 1500 degrees Celsius (2732 degrees Fahrenheit). The melting process is critical as it converts the solid iron sand into a liquid form that can be poured into the mold. Depending on the desired properties of the final product, additives such as carbon or silicon may be introduced to the molten metal to enhance its characteristics.
Pouring and Cooling
After melting, the molten iron is carefully poured into the mold. This step requires precision to avoid defects like air pockets or incomplete filling, which can compromise the integrity of the final product. Once filled, the mold is allowed to cool, enabling the molten iron to solidify and take on the shape of the mold cavity.
Cooling times can vary depending on the size and complexity of the cast, with larger items requiring more time to solidify than smaller ones. During this phase, the metal undergoes significant changes in its structure, allowing it to achieve the rigidity and strength associated with cast iron components.
Finishing Processes
iron sand casting process
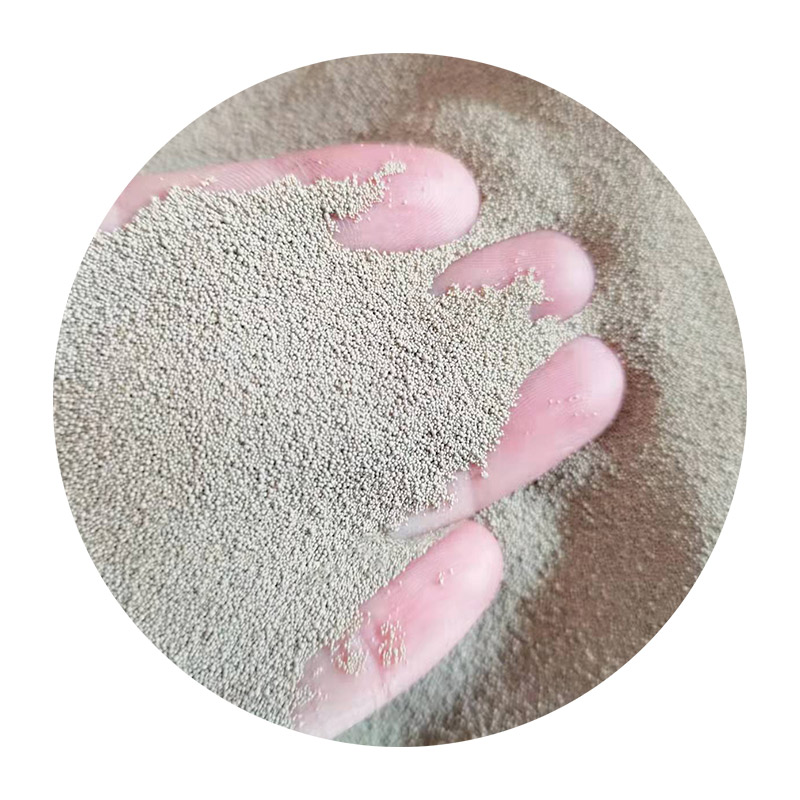
Upon cooling, the mold is broken away to reveal the cast iron object. However, the process does not end here. The newly cast item often requires additional finishing treatments. These treatments can include trimming excess material (known as gates and risers), grinding, polishing, and sometimes heat treatment to enhance mechanical properties.
In some cases, surface treatments such as painting or coating are applied to improve corrosion resistance and aesthetic appeal. Finishing processes are crucial as they determine the final quality and functionality of the cast product.
Advantages of Iron Sand Casting
One of the primary advantages of iron sand casting lies in its versatility. This process can produce complex shapes and intricate details that might be challenging to achieve with other manufacturing methods. Additionally, the use of iron sand, which is often abundant and inexpensive, makes this process economically viable.
Another benefit is the durability of cast iron products, making them suitable for various applications, including automotive components, pipes, machinery, and decorative items. Moreover, the adaptability of the molds allows for customized production runs, catering to specific customer requirements.
Applications
Iron sand casting has a broad range of applications. In the automotive industry, it is used for manufacturing engine blocks, cylinder heads, and brake components. In construction, cast iron is used for making pipes and fittings. Artistic applications include sculptures and decorative pieces, demonstrating the aesthetic potential of this material.
Conclusion
Iron sand casting is a sophisticated process that combines natural resources with advanced manufacturing techniques. Its ability to produce high-quality, durable components makes it a preferred choice in numerous industries. As technology continues to evolve, iron sand casting remains a reliable method for creating both functional and artistic metal products, demonstrating the enduring value of this traditional manufacturing practice.
Post time:pro . 13, 2024 03:50
Next:3d printed sand casting patterns