Investment Casting vs. Sand Casting A Comprehensive Comparison
When it comes to metal casting techniques, two of the most widely utilized methods are investment casting and sand casting. While both methods serve the fundamental purpose of producing metal components, they differ significantly in terms of precision, cost, applications, and production volume. This article will delve into the key differences between these two casting methods to help manufacturers choose the most appropriate technique for their specific needs.
1. Overview of Casting Techniques
Investment casting, also known as lost-wax casting, is a process where a wax pattern is coated with a ceramic material to create a mold. Once the mold is hardened, the wax is melted away, leaving a cavity into which molten metal is poured. This method is renowned for its ability to produce complex shapes with high precision and excellent surface finish.
On the other hand, sand casting involves creating molds using sand mixed with a binder. The sand mold is formed around a pattern of the desired object, and once the mold is ready, molten metal is poured into the cavity. After the metal cools and solidifies, the sand mold is broken away to reveal the cast part. Sand casting is one of the oldest casting methods and is frequently used for larger parts and simpler geometries.
2. Precision and Surface Finish
One of the most significant advantages of investment casting is its precision. This method can achieve tolerances as tight as ±0.005 inches, making it suitable for intricate components that require detailed features. The surface finish produced by investment casting is also superior, often eliminating the need for additional machining.
In contrast, sand casting typically has a rougher surface finish and may require further machining to achieve the desired tolerances. While it can be precise, sand casting is generally more suited for less intricate designs. However, advancements in sand casting techniques have improved its precision and surface finish in recent years.
investment vs sand casting
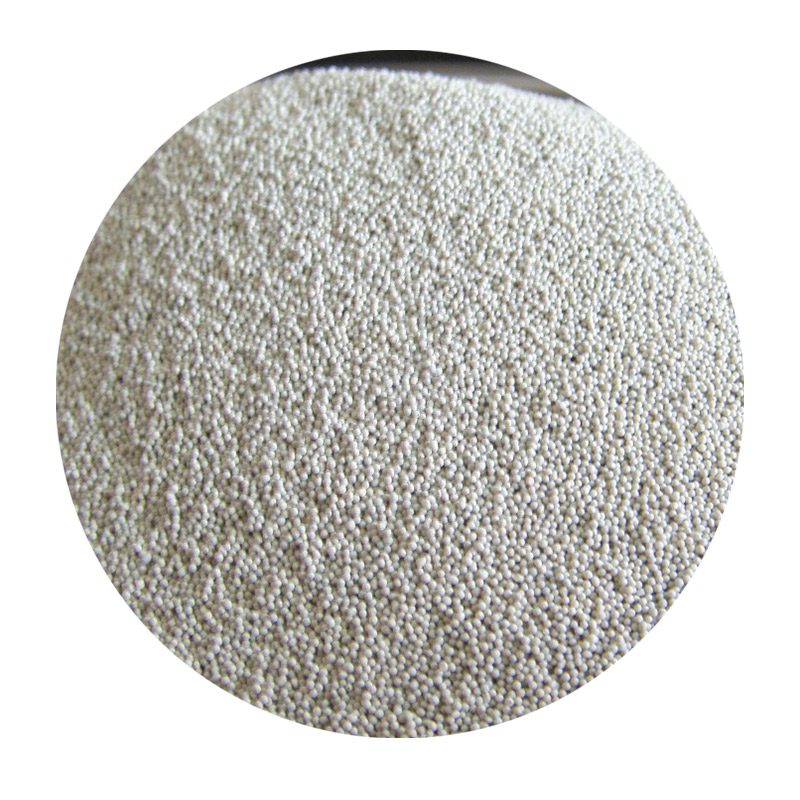
3. Cost and Production Volume
In terms of cost, investment casting tends to be more expensive than sand casting due to higher material costs and the complex processes involved. The initial setup for investment casting, including the production of wax patterns and ceramic molds, can be significant. However, investment casting becomes cost-effective for high-volume production runs, as the per-unit cost decreases dramatically with increased quantities.
Sand casting is more economical for both small and large production runs. The materials required for sand casting are less expensive, and the process allows for quicker mold production. Additionally, the flexibility of sand casting enables manufacturers to produce a wide variety of parts with different sizes and shapes without extensive retooling.
4. Materials and Applications
Both investment and sand casting can accommodate a range of materials, including ferrous and non-ferrous metals. However, investment casting is particularly suited for high-performance alloys, exotic materials, and parts requiring high strength and ductility. Common applications include aerospace components, dental and medical devices, and intricate automotive parts.
Sand casting is favored for larger components and less critical applications, often used in industries such as construction, marine, and general manufacturing. It is ideal for creating large parts, like engine blocks and frames, that do not require the same level of precision as investment cast components.
Conclusion
Choosing between investment casting and sand casting ultimately depends on the specific requirements of the project. If precision, surface finish, and complex geometries are paramount, investment casting is the better choice despite its higher costs. Conversely, for larger, simpler parts where cost efficiency is a priority, sand casting offers a practical solution. Understanding the strengths and limitations of each method allows manufacturers to make informed decisions that can enhance productivity and reduce costs in their operations. Regardless of the method chosen, both investment and sand casting remain integral to the metalworking industry, providing versatile solutions for a wide range of applications.
Post time:lis . 14, 2024 04:56
Next:how to sand small 3d prints