Understanding Industrial Sand Casting A Fundamental Process in Manufacturing
Industrial sand casting, an ancient method of forming metal into precise shapes, has remained a cornerstone of modern manufacturing due to its versatility and cost-effectiveness. As industries continue to evolve, the importance of this process becomes increasingly clear. This article delves into the sand casting process, its applications, advantages, and future potential in the manufacturing landscape.
The Sand Casting Process
At its core, sand casting involves creating a mold for metal casting using sand as the main material. The process begins with designing a pattern, which mirrors the desired end product. Typically made from metal, plastic, or wood, the pattern is then used to form the mold.
1. Mold Creation The first step in sand casting is the preparation of the mold. The pattern is pressed into a mixture of sand and a binding agent, which compacts the sand to retain the shape of the pattern. This mixture is often made up of silica sand, clay, and water, although other additives can enhance specific properties.
2. Melting and Pouring Once the mold is ready, a metal alloy is melted in a furnace. The choice of metal varies based on the application and desired properties of the final product—common choices include aluminum, iron, and bronze. After reaching the appropriate temperature, the molten metal is poured into the prepared mold.
3. Cooling and Finishing After the metal fills the mold, it is left to cool and solidify. Once cooled, the sand mold is broken away to reveal the cast piece. Final finishing treatments such as grinding, polishing, or machining may be applied to achieve the required surface finish and dimensions.
Applications of Sand Casting
Sand casting is widely utilized across various industries due to its flexibility and ability to produce complex geometries. Key applications include
- Automotive Parts Many components of vehicles, such as engine blocks, gears, and housings, are manufactured using sand casting due to the high strength and durability of cast metals.
- Aerospace Components The aerospace industry relies on sand casting to produce intricate parts that must withstand extreme conditions while minimizing weight.
- Industrial Machinery Equipment used in heavy industries often requires robust components that can be reliably produced through sand casting.
industrial sand casting
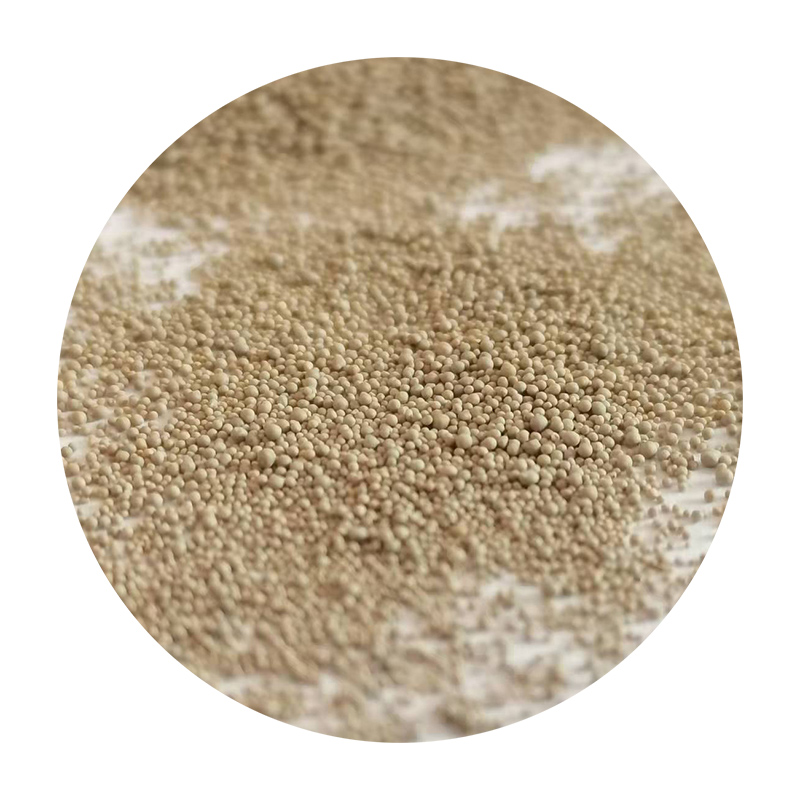
- Artistic and Architectural Elements Beyond industrial applications, sand casting is also employed in creating sculptures, decorative elements, and architectural features, showcasing the artistic potential of this method
.Advantages of Sand Casting
The popularity of sand casting can be attributed to several advantages it offers
1. Cost-Effectiveness The materials used (sand and basic binding agents) are inexpensive compared to alternative casting methods. This makes sand casting an economical choice, especially for large production runs or one-off pieces.
2. Versatility Sand casting can accommodate a wide range of sizes, from small components to large industrial parts. Additionally, it can work with various metals, providing immense flexibility to manufacturers.
3. Design Freedom The process allows for the production of complex shapes that may be challenging to achieve with other methods. This is particularly beneficial for applications requiring intricate designs.
4. Scalability Sand casting can be easily scaled from prototyping to mass production without substantial changes to the process or equipment.
Future Potential
As the manufacturing landscape continues to change, so too does the sand casting process. Innovations in technology are paving the way for more efficient production methods. For instance, the integration of computer-aided design (CAD) systems allows for greater precision in mold design. Additionally, advancements in materials science may lead to the development of new binding agents and sand mixtures that enhance the casting process.
Moreover, digital technologies such as 3D printing are beginning to influence the sand casting process by creating more intricate patterns and molds, increasing communication and flexibility in design while reducing lead times.
In conclusion, industrial sand casting remains an essential process in manufacturing due to its versatility, cost-effectiveness, and capability to produce complex shapes. As industries advance and embrace new technologies, sand casting will likely continue to play a vital role in recent developments and innovations in manufacturing practices.
Post time:stu . 27, 2024 14:25
Next:Understanding the Process and Benefits of Sand Casting in Modern Foundries