Industrial Sand Casting An Essential Manufacturing Process
Industrial sand casting, also known simply as sand casting, is a widely used manufacturing process that has been instrumental in the production of complex metal components across various industries. This method, which involves pouring molten metal into a sand mold to create solid parts, combines both tradition and innovation, making it a favored choice for manufacturers worldwide.
The Sand Casting Process
The sand casting process begins with the creation of a sand mold. This involves tightly packing sand, usually mixed with a binding agent, around a pattern that represents the final product. The pattern is often made from metal, wood, or plastic and is critical in determining the shape and dimensions of the finished piece. Once the mold is prepared, the pattern is removed, leaving a hollow cavity that mirrors the desired object.
After the mold is formed, molten metal is poured into the cavity. The metal used can vary widely, including aluminum, iron, steel, and bronze, depending on the application and desired properties of the final product. Once the molten metal fills the mold, it is allowed to cool and solidify. After cooling, the mold is broken apart, and the cast part is removed, completing the casting process.
Advantages of Sand Casting
One of the significant advantages of sand casting is its versatility. It can accommodate a broad range of sizes, from small precision parts to large components such as engine blocks and machine bases. Sand molds can be reused to a certain extent, which contributes to cost-efficiency in large production runs. Additionally, the sand casting process allows for the incorporation of intricate designs and features, making it suitable for both low and high-volume manufacturing needs.
Another major benefit is the ability to cast a variety of metals. Different alloys can be used to achieve specific mechanical properties, such as strength, ductility, and resistance to wear and corrosion. This flexibility is crucial in industries such as automotive, aerospace, and heavy machinery, where the performance of components is paramount.
industrial sand casting
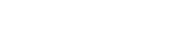
Challenges in Sand Casting
Despite its many advantages, sand casting does face some challenges. One major concern is the potential for defects in the final product, such as porosity, shrinkage, or surface imperfections. These defects can arise from various factors, including improper mold design, inadequate melting techniques, or insufficient cooling time. Manufacturers must carefully control each aspect of the process to minimize these issues and ensure high-quality outputs.
Furthermore, the sand casting process can be labor-intensive, requiring skilled technicians to manage the intricate steps involved in mold making, metal pouring, and finishing. Automation and advancements in technology are beginning to alleviate some of these challenges, yet the need for human oversight remains vital, particularly in more complex operations.
Future Trends in Sand Casting
The future of industrial sand casting looks promising, driven by technological advances and evolving industry demands. Innovative techniques, such as 3D printing for mold production, are revolutionizing the process, allowing for faster prototypes and reduced lead times. This shift not only streamlines production but also enhances design flexibility, enabling manufacturers to create more intricate and lightweight components.
Additionally, there is a growing emphasis on sustainability within the sand casting industry. Efforts are underway to develop more environmentally friendly materials, recycle sand, and reduce waste during the casting process. Such initiatives not only meet regulatory demands but also align with global trends towards sustainable manufacturing practices.
Conclusion
Industrial sand casting is an integral part of modern manufacturing, offering a blend of versatility, cost-effectiveness, and the ability to produce high-quality metal components. While challenges persist, ongoing advancements in technology and a focus on sustainability promise to propel this age-old technique into the future. As industries continue to demand more complex and efficient parts, sand casting will undoubtedly remain a cornerstone of metal fabrication, driving innovation and supporting the global economy.
Post time:stu . 09, 2024 04:16
Next:Understanding the Process for Successful Sand Casting in Metal Fabrication Techniques