Understanding Foundry Sand Properties A Key to Quality Casting
Foundry sand is a crucial material in the metal casting process, playing a vital role in the production of high-quality cast components. This article explores the properties of foundry sand, their significance in metal casting, and how they influence the final product's quality and performance.
Types of Foundry Sand
The primary types of sand used in foundries are silica sand, chromite sand, zircon sand, and olivine sand. Silica sand is the most commonly used due to its abundance and excellent thermal properties. Chromite sand is preferred for its high density and thermal conductivity, making it ideal for steel and iron casting. Zircon sand, known for its low thermal expansion and high melting point, is advantageous for producing intricate molds. Olivine sand, with its superior green strength and thermal stability, is suitable for specific applications where these characteristics are essential.
Key Properties of Foundry Sand
1. Grain Shape and Size The grain shape and size distribution of foundry sand significantly impact the mold's strength and permeability. Ideally, the sand grains should be spherical or sub-angular to promote better packing and strength. The optimal particle size typically ranges from 0.25 mm to 0.50 mm, allowing for adequate flowability and compaction while maintaining sufficient permeability for gas escape during the casting process.
foundry sand properties
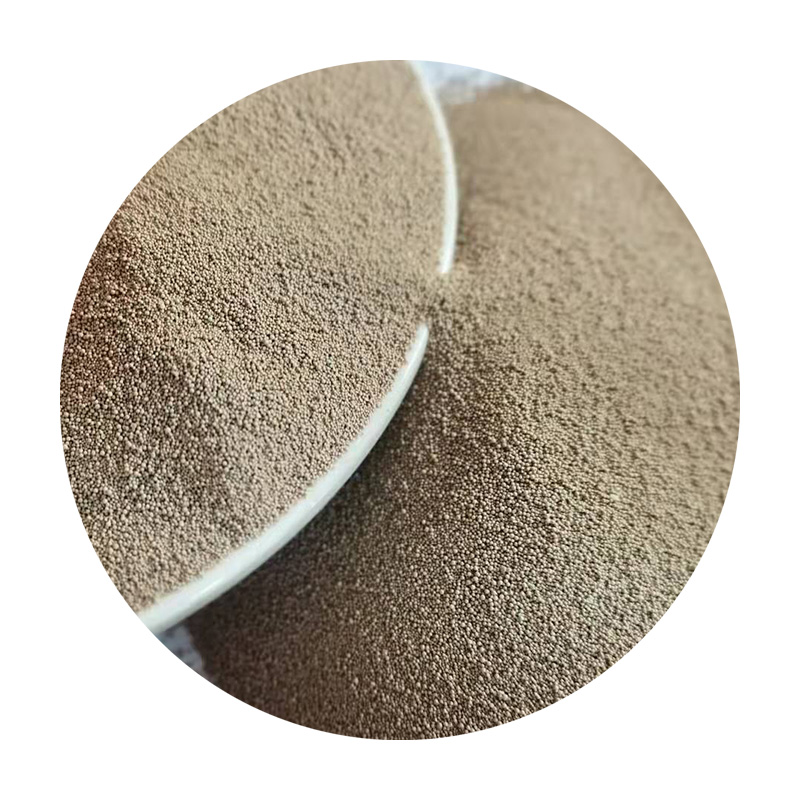
2. Moisture Content The moisture content of foundry sand affects its bonding ability and strength. Too much moisture can lead to mold defects such as gas porosity, while insufficient moisture can result in inadequate mold strength. Maintaining an optimal moisture level is crucial for achieving the right balance between strength and permeability.
3. Thermal Properties Foundry sand must withstand high temperatures during the metal pouring process. Sand with high thermal stability prevents mold deformation and maintains shape integrity. Its thermal conductivity also plays a role in heat dissipation, affecting the cooling rate of the molten metal and consequently the microstructure of the final casting.
4. Bonding Characteristics The bonding properties of foundry sand dictate how well it holds together during the molding process. This is largely influenced by the type of binder used, which can include clay, resin, or chemical binders. A well-bonded sand mix ensures that the mold retains its shape and can withstand the physical stresses encountered during pouring.
5. Permeability Permeability reflects the ability of the sand mold to allow gases produced during casting to escape. High permeability is essential to prevent gas entrapment, which can lead to defects such as blowholes or foamy casts. However, there is a trade-off between permeability and strength; therefore, finding an optimal balance is key.
Conclusion
The properties of foundry sand are fundamental to the success of the casting process. Understanding these properties helps foundry engineers select the appropriate sand type and composition for specific applications, leading to improved casting quality and reduced defects. As the foundry industry continually evolves, advancements in sand treatment and recycling technologies are likely to further enhance the efficiency and sustainability of the casting process. Future innovations may lead to the development of synthetic sands or alternative materials that provide even better properties, paving the way for higher-quality castings and a more environmentally friendly approach to metal production. Engaging in thorough research and development efforts will ensure that foundry sand properties keep pace with the demands of modern manufacturing.
Post time:lis . 16, 2024 18:26
Next:gold sand price