Understanding Foundry Sand Density Importance and Applications
Foundry sand plays a vital role in the metal casting industry, serving as a crucial component in the formation of molds and cores. One of the key characteristics that influence the performance of foundry sand is its density. Understanding foundry sand density is essential for optimizing foundry operations, enhancing product quality, and ensuring the economic viability of casting processes.
What is Foundry Sand?
Foundry sand is a high-quality silica sand that is used in metal casting processes. Its primary function is to support the formation of molds and cores that shape molten metal into desired products. The sand can withstand high temperatures and has properties that allow it to be reused multiple times, making it a cost-effective option for foundries.
Importance of Density in Foundry Sand
Density, defined as mass per unit volume, is a critical property of foundry sand that influences its performance. The density of the sand can affect various factors in the casting process, including
1. Mold Strength Higher density can lead to stronger molds, which can withstand the pressure exerted by molten metals. This is especially important in complex casting shapes that require durability and stability during the pouring process.
2. Heat Retention Dense sands have better thermal properties and can maintain their structure under high temperatures. This helps in achieving uniform heating during the casting process and minimizes defects.
3. Sand Flowability The density of the sand impacts its flow characteristics when mixed with binders and moisture. A well-balanced density ensures that the sand can fill mold cavities efficiently, which is essential for detailed castings.
4. Reusability Foundry sands are often reused multiple times. Understanding and managing the density helps maintain the sand’s performance over several cycles, reducing waste and lowering production costs.
Measurement of Foundry Sand Density
foundry sand density
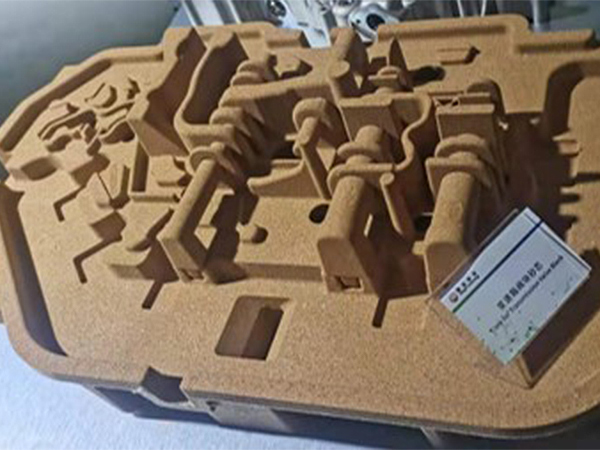
The density of foundry sand is typically measured using techniques such as the use of pycnometers and bulk density tests. These methods allow foundries to obtain precise measurements that can be correlated with the performance of the sand in casting applications.
The two primary types of density measurements relevant to foundry sands are
- Bulk Density This measurement considers the total mass of the sand, including the empty spaces between particles. High bulk density often correlates with lower porosity, which can contribute to improved mold strength.
- True Density This is the mass of the sand particles alone, excluding all voids. True density can provide insights into the material properties of the sand itself, influencing decisions on material sourcing and mixing.
Factors Affecting Foundry Sand Density
Several factors can influence the density of foundry sand, including
- Grain Size Finer sands tend to offer higher density compared to coarser ones because finer grains can pack more tightly together, reducing void space.
- Moisture Content The amount of moisture added to the sand mixture can significantly influence its density. The right moisture level is essential for achieving optimal compaction and mold integrity.
- Additives and Binders Various chemical additives may be introduced to enhance sand performance, and these can also alter the overall density of the sand mixture.
Conclusion
The density of foundry sand is a critical factor that affects the performance and efficiency of metal casting processes. By understanding and managing this property, foundries can optimize their operations, improve the quality of cast products, and reduce costs. As the industry evolves, advancements in technology and material science will further enhance our understanding of foundry sand density, leading to better practices and innovations in casting. As such, foundry professionals must prioritize the measurement and optimization of sand density to stay competitive in a rapidly changing market.
Post time:pro . 03, 2024 20:26
Next:Exploring Various Categories of Foundry Sand for Metal Casting Applications