Different Types of Foundry Sand
Foundry sand is a vital ingredient in the metal casting process, serving as a mold material for various metal products. The quality and type of foundry sand can significantly influence the performance, characteristics, and overall outputs of the casting. There are several different types of foundry sands, each with distinct properties and applications.
1. Green Sand
Green sand, often referred to as clay sand, is one of the most commonly used types of foundry sand. It is composed of silica sand, clay, water, and some additives. The term green reflects the fact that the sand is not dried or thermally cured. Green sand is favored for its excellent molding properties, good compressive strength, and ability to produce detailed and accurate castings. Additionally, it is relatively inexpensive and easy to work with, making it a popular choice for both small and large foundries.
Resin-bonded sand is created by mixing sand with a resin binder that hardens when subjected to heat. This type of sand boasts superior strength and dimensional precision compared to green sand. Its ability to withstand higher temperatures without deforming makes it ideal for casting high-performance and complex designs. Although it may be more expensive than traditional green sand, the increased accuracy and reduced need for post-casting processing enhance its appeal, particularly in industries such as automotive and aerospace.
3. No-Bake Sand
different types of foundry sand
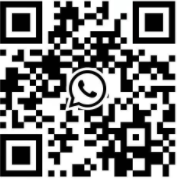
No-bake sand is another type of resin-bonded sand that does not require baking in an oven to harden. Instead, a chemical reaction occurs when the resin is mixed with a hardener, causing it to cure at room temperature. This type of sand is advantageous for creating large and intricate molds, reducing the overall production time. No-bake sand is commonly used in applications where high surface quality and accuracy are critical, allowing for thinner molds and less waste.
4. Shell Sand
Shell sand consists of a mixture of sand coated with a thermosetting resin binder that forms a thin shell when heated. This allows for the creation of strong and lightweight molds while maintaining a good finish on the casting surface. Shell sand is commonly used in the production of intricate and detailed parts due to its excellent dimensional accuracy and fine surface finish. It is particularly prevalent in the manufacturing of precision components for industries such as medical and aerospace engineering.
5. Zircon Sand
Zircon sand is a premium type of foundry sand known for its exceptional thermal stability and high refractoriness. Its superior properties make it suitable for casting metals with high melting points, such as titanium and nickel-based alloys. Zircon sand is resistant to chemical degradation, which makes it an excellent choice for high-performance molds, particularly in industries requiring extreme temperature and pressure conditions.
Conclusion
The choice of foundry sand is crucial as it directly impacts the quality and efficiency of metal casting processes. Each type of foundry sand, from green sand to specialty options like zircon sand, has unique properties that cater to diverse casting needs. Understanding these differences allows foundries to optimize their production methods, ensuring high-quality results that meet industry standards. By selecting the appropriate foundry sand, manufacturers can enhance their competitive edge and improve the overall quality of their casted products.
Post time:pro . 17, 2024 00:52
Next:foundry casting sand