Advantages of Lost Foam Casting
Lost foam casting (LFC), a specialized form of investment casting, offers a unique approach to producing high precision metal parts. This process involves creating a foam pattern of the desired part and embedding it in a sand mold. When molten metal is poured into the mold, the foam pattern evaporates, leaving behind the intricately shaped metal component. The method has been gaining popularity in various industries, including automotive, aerospace, and manufacturing, due to several compelling advantages.
1. High Precision and Complexity
One of the primary advantages of lost foam casting is its ability to produce highly complex geometries with excellent precision. The foam patterns can accommodate intricate designs that would be difficult or impossible to achieve with traditional casting methods. This allows manufacturers to create components with hollow sections, internal cavities, and complex contours, ultimately enhancing the performance and functionality of the final product.
2. Elimination of Core Sand
In many traditional casting techniques, core sand is often required to create internal features of a part, which adds steps to the manufacturing process. With LFC, the elimination of core sand simplifies the process and reduces the need for additional equipment. This results in lower material costs and reduced overall production time, contributing to a more streamlined manufacturing workflow.
3. Improved Surface Finish
The vaporization of the foam pattern during the pouring of molten metal leads to a smoother surface finish on the cast part. Lost foam casting typically yields a surface that requires less machining after the casting process, which can significantly reduce post-production costs. This not only saves time but also minimizes material waste, as less material is removed to achieve the desired finish.
4. Reduced Waste and Environmentally Friendly
advantages of lost foam casting
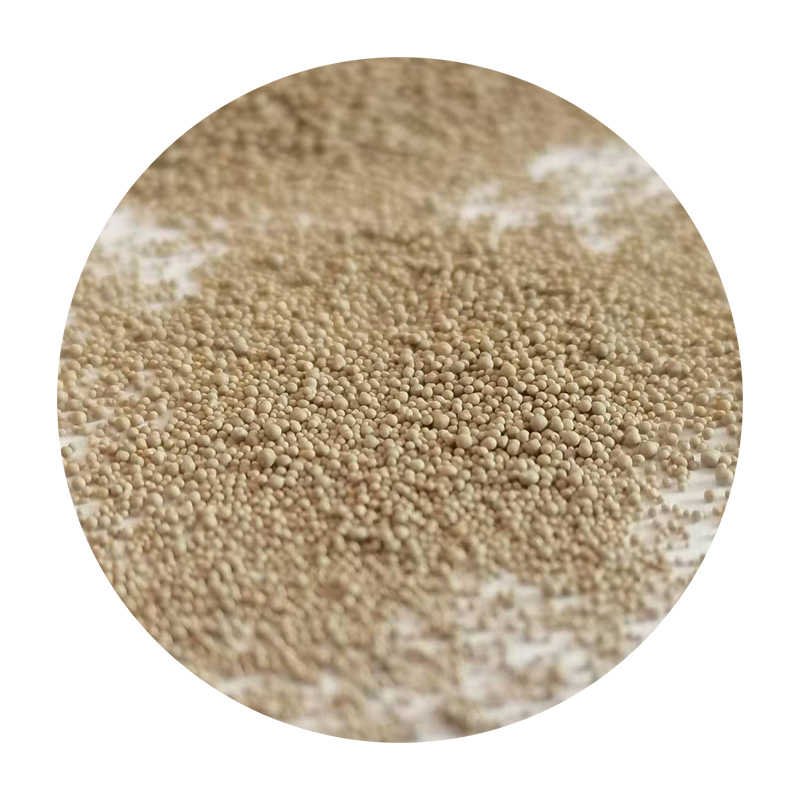
Lost foam casting is a more environmentally friendly option compared to traditional methods. The foam patterns used are often made from expanded polystyrene (EPS), which can be recycled. Additionally, because the process produces less waste in terms of excess material and scrap, manufacturers can contribute to sustainability efforts while maintaining efficient production practices.
5. Flexibility in Material Choices
Lost foam casting is versatile and can accommodate a variety of metals, including aluminum, iron, and steel. This flexibility allows manufacturers to choose the most suitable material for their specific application while benefiting from the unique characteristics that different metals provide. Whether the goal is to achieve lightweight components or high-strength parts, LFC can deliver results tailored to the requirements of the project.
6. Cost-Effectiveness for Medium to Large Production Runs
While there may be higher initial setup costs associated with the lost foam casting process, it becomes increasingly cost-effective as production volume rises. The ability to create multiple components from a single pattern further enhances efficiency, making LFC an attractive option for medium to large production runs. Manufacturers can balance the initial investment with the long-term savings realized through reduced labor, material usage, and machining requirements.
7. Enhanced Design Freedom
With lost foam casting, designers are not as constrained by the limitations of traditional molding methods. The flexibility of the foam pattern allows for innovation in design, opening new avenues for product development. This has significant implications for industries seeking to develop cutting-edge products that are both functional and aesthetically pleasing.
Conclusion
Lost foam casting stands as a noteworthy process in modern manufacturing, offering unique advantages that cater to the evolving demands of various industries. Its ability to produce complex, high-precision components with an excellent surface finish, coupled with reduced waste and increased design freedom, positions LFC as a leading choice for manufacturers looking to optimize both their production efficiency and product performance. As environmental considerations gain prominence, the sustainable aspects of lost foam casting further enhance its appeal in a competitive market, leading to greater adoption in the years to come.
Post time:stu . 25, 2024 05:19
Next:Techniques for Smoothly Sanding Your 3D Printed Models for a Professional Finish