Advantages and Disadvantages of the Sand Casting Process
Sand casting is one of the most widely used metal casting processes, owing to its versatility and ability to produce complex geometries. This method involves creating a mold from a sand mixture, pouring molten metal into the mold, and allowing it to solidify. While sand casting has numerous advantages, it also comes with a set of disadvantages that must be considered.
Advantages of Sand Casting
One of the primary advantages of sand casting is its cost-effectiveness. The materials required—sand, clay, and water—are relatively inexpensive and readily available. This makes sand casting an economical choice for both small and large production runs. Additionally, sand molds can be reused, further reducing costs over time.
Another significant advantage is the versatility of the sand casting process. It can accommodate a wide range of metals including iron, aluminum, copper, and their alloys. This flexibility allows manufacturers to produce an array of components, from small parts to large machinery, making it suitable for various industries such as automotive, aerospace, and construction.
Furthermore, sand casting allows for the production of complex shapes and intricate designs that may be difficult to achieve with other casting methods. The process involves minimal tooling, which means faster turnaround times and the ability to quickly modify designs if necessary. This adaptability is particularly beneficial for prototyping and custom projects.
The sand casting process is also relatively easy to learn and implement
. With basic training, operators can quickly become proficient, which can lead to lower labor costs and reduced training times.advantages and disadvantages of sand casting process
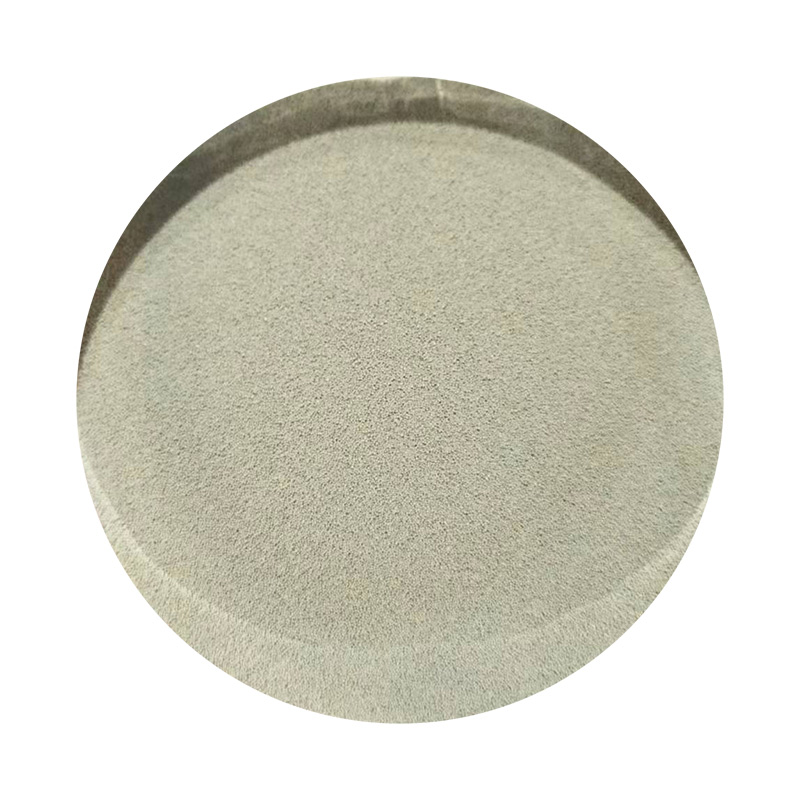
Disadvantages of Sand Casting
However, sand casting is not without its drawbacks. One notable disadvantage is the rough surface finish of cast components. The sand used in the molding process can lead to imperfections and sand inclusion in the final product, which may require additional machining or finishing processes to achieve the desired surface quality. This can increase production times and costs.
Another disadvantage is the limitation in the dimensional accuracy and tolerances that can be achieved with sand casting. Although the process can create complex shapes, maintaining tight tolerances can be challenging. This can pose problems for applications that require high precision.
The production speed of sand casting is generally slower compared to other methods such as investment casting or die casting. This is due in part to the time required for creating molds and allowing the metal to cool and solidify. For high-volume production, this can be a significant drawback.
Finally, the sand casting process often involves a degree of environmental impact. The disposal of used sand and the emissions generated during the melting and pouring of metals can pose ecological challenges. Manufacturers need to be aware of environmental regulations and may need to implement systems to mitigate their ecological footprint.
Conclusion
In summary, sand casting is a valuable manufacturing process with several advantages, including cost-effectiveness, versatility, and the ability to produce complex shapes. However, its disadvantages, such as rough surface finishes, limitations in dimensional accuracy, slower production speeds, and environmental concerns, must be carefully weighed. For many applications, the benefits of sand casting can outweigh its drawbacks, making it a vital process in the manufacturing industry. Selecting the right casting method depends on specific project requirements, production volumes, and desired quality.
Post time:kol . 30, 2024 11:07
Next:High Quality Sand Casting Services | Precision Manufacturing Solutions