3D Printing Patterns for Sand Casting Revolutionizing Manufacturing
The advent of 3D printing technology has significantly transformed various sectors of manufacturing, and sand casting is no exception. Sand casting, a traditional method for producing metal parts, involves creating a mold from a pattern and then pouring molten metal into the mold to form the desired shape. Traditionally, manufacturing these patterns was time-consuming and costly. However, with the integration of 3D printing, the industry is witnessing a radical shift towards enhanced efficiency, reduced lead times, and increased design flexibility.
The Role of 3D Printing in Sand Casting
3D printing patterns for sand casting offers several advantages over conventional methods. Traditional pattern making often involves machining, which requires significant material removal, complex tooling, and an immense amount of manual labor. In contrast, 3D printing allows for the direct creation of patterns using additive manufacturing processes. This method significantly reduces waste, as material is only added where necessary, leading to a more sustainable production process.
Moreover, the rapid prototyping capabilities of 3D printing enable manufacturers to create patterns quickly. Designers can develop intricate designs that were previously difficult or impossible to achieve with conventional techniques. This flexibility encourages innovation and allows for the exploration of complex geometries which can enhance the product's performance or reduce its weight.
Materials Used in 3D Printing Patterns
When it comes to 3D printing patterns for sand casting, various materials can be employed. The most commonly used materials include thermoplastics, resin, and even metal in some advanced applications. Thermoplastics allow for high precision and are suitable for high-quality patterns, while resin-based printing provides intricate detail, making them ideal for complex designs. Some innovative methods also utilize a mixture of sand and a binding agent that can be 3D printed to create molds directly, streamlining the casting process further.
The choice of material can significantly influence the casting process and the properties of the final product. For instance, materials with high thermal conductivity can help in reducing cooling times, which is critical in managing the dimensional accuracy of the final cast metal part.
Cost Efficiency and Time Savings
3d printing patterns for sand casting
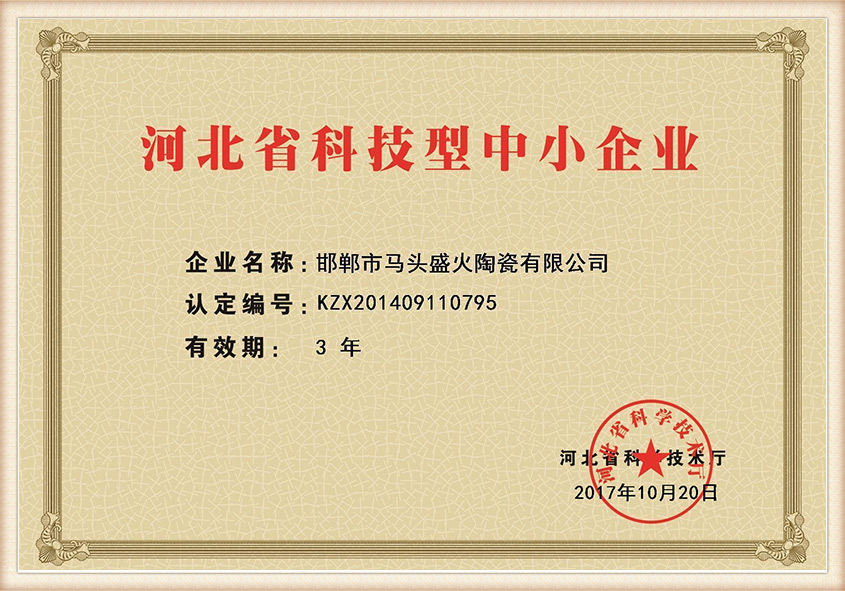
One of the primary motivations for adopting 3D printing patterns in sand casting is cost efficiency. Traditional methods often require significant investments in tooling and setup, which can be prohibitive for small manufacturers or prototyping stages. 3D printing reduces the setup costs and allows for low-volume production runs, making it feasible to produce higher-quality products without a large financial commitment.
Additionally, the fast turnaround time associated with 3D printing means that manufacturers can go from design to production in a fraction of the time. This becoming an essential factor in industries where speed to market is crucial, such as automotive and aerospace.
Challenges and Considerations
Despite the advantages, transitioning to 3D printing patterns for sand casting does come with challenges. One of the primary concerns is the quality and consistency of the printed patterns. It is essential for manufacturers to evaluate the technology and materials adequately to ensure they meet the standards required for production.
Furthermore, integrating 3D printing into existing workflows might require training and adaptation. Workers must learn new software and printing techniques, and the initial investment in 3D printing technology can be a barrier for some businesses.
Future Prospects
As 3D printing technology continues to evolve, we can expect even greater advancements in sand casting applications. Improved materials, faster printing speeds, and enhanced automation will likely drive down costs and further increase adoption rates. The future may even hold the possibility of entirely automated casting processes where artificial intelligence optimizes designs and printing parameters for maximum efficiency.
In conclusion, 3D printing patterns for sand casting represents a significant step forward for the manufacturing sector. By offering reduced costs, increased design freedom, and sustainable practices, this technology is not only enhancing current manufacturing processes but also paving the way for innovative new applications in various industries. As the technology matures, it will undoubtedly become a staple in the production of custom and complex metal components, shaping the future of manufacturing.
Post time:stu . 09, 2024 10:18
Next:Exploring Various Types of Foundry Sand for Metal Casting Applications