Sand Casting Procedure A Comprehensive Guide
Sand casting, also known as sand mold casting, is a widely used metal casting process that involves creating a mold out of sand and then pouring molten metal into this mold to form a desired shape. It is lauded for its versatility, cost-effectiveness, and suitability for both large and small production runs. In this article, we will delve into the sand casting procedure, outlining the key steps involved and providing insights into best practices.
Step 1 Designing the Pattern
The first step in the sand casting process is to create a pattern, which is a replica of the object to be cast. Patterns can be made from various materials, such as wood, metal, or plastic, depending on the complexity of the design and the volume of production. The pattern must account for shrinkage, which occurs as the metal cools and solidifies. Generally, an allowance of about 1% is added to the dimensions to accommodate for this shrinkage.
Step 2 Preparing the Sand Mold
Once the pattern is ready, it is time to prepare the sand mold. The sand used in sand casting is typically a mixture of silica sand, clay, and water. The clay acts as a binder, holding the sand grains together, while the water helps to activate the clay. The preparation of the sand involves a process called molding, where the sand mixture is packed around the pattern to create a mold cavity. This can be done using either the green sand method, which utilizes moist sand, or the dry sand method, which uses dry sand for higher precision.
Step 3 Assembling the Mold
After the sand has been packed around the pattern, it is necessary to remove the pattern to leave behind the mold cavity. This is done carefully to avoid damaging the mold. The two halves of the mold are then assembled using anchoring pins or clamps to ensure they stay in place when the molten metal is poured in. It is also important to create pouring basins and vents in the mold to facilitate the flow of metal and allow gases to escape.
Step 4 Melting the Metal
sand casting procedure
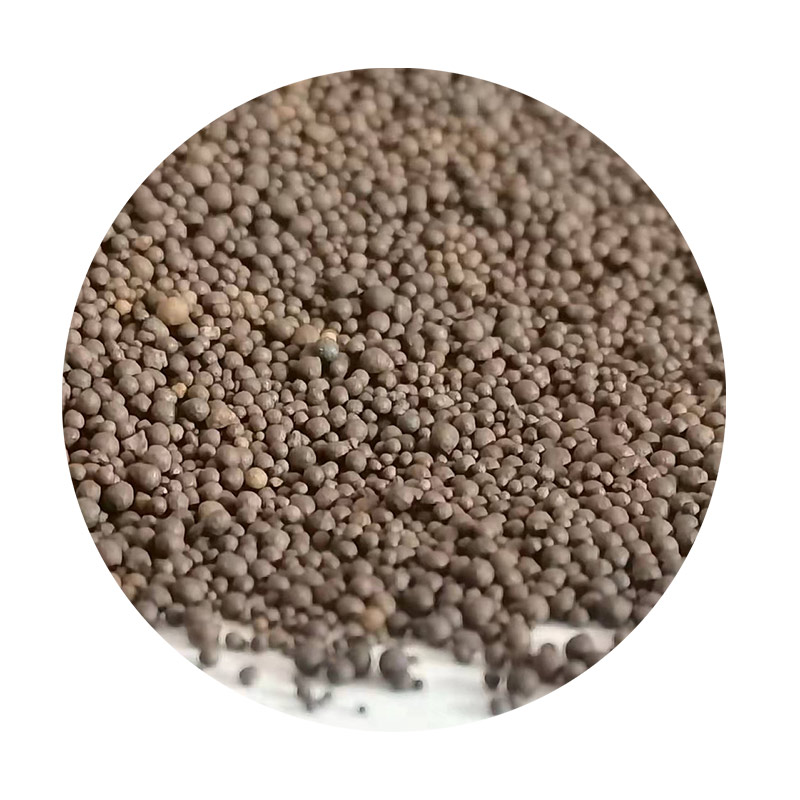
With the mold prepared, the next step is to melt the metal that will be poured into the mold. The metal is typically heated in a furnace, where it reaches its melting point before being poured. Common metals used in sand casting include aluminum, iron, and bronze, each chosen for their specific properties and applications. Safety precautions are crucial during this stage, as molten metal can be hazardous.
Step 5 Pouring the Metal
Once the metal has melted, it is poured into the mold through the pouring basin. This step requires precision to ensure that the mold is filled uniformly, minimizing the chances of defects such as air bubbles or cold shuts (areas where the metal does not fuse properly). It is essential to maintain a consistent pouring temperature and flow rate to achieve the best results.
Step 6 Cooling and Solidification
After the mold is filled, the next step is cooling. The cooling time depends on the thickness of the casting and the type of metal used. During this period, the molten metal solidifies and takes the shape of the mold. Once sufficient time has passed, the mold is broken apart, and the casting is removed. It is crucial to handle the casting with care to prevent any damage during removal.
Step 7 Finishing the Casting
Once the casting is removed, it often requires finishing to achieve the desired surface quality and dimensions. This may involve processes such as sanding, grinding, or machining. Additional operations like heat treating may also be performed to enhance the mechanical properties of the casting.
Conclusion
Sand casting is a time-tested method that continues to be invaluable in various industries, from automotive to aerospace. By understanding the steps of the sand casting procedure, manufacturers can achieve high-quality castings efficiently. Whether for prototyping or mass production, mastering the nuances of sand casting can significantly impact the quality and performance of the final product. As technology progresses, innovations in materials and methods will likely enhance the capabilities of this classic casting technique, further broadening its applications.
Post time:Dec . 03, 2024 19:29
Next:Exploring the Secrets of Gold-Rich Sands in the World’s Most Bountiful Regions