The Art and Science of Sand Casting
Sand casting, one of the oldest and most versatile metal casting processes, combines ancient craftsmanship with modern engineering methods. It has stood the test of time due to its ability to produce intricate shapes and components across a variety of industries, from automotive to aerospace and even art.
What is Sand Casting?
At its core, sand casting involves creating a mold from sand that has been mixed with other materials to enhance its cohesion and durability. The process begins with the creation of a pattern, which is a replica of the desired final product. This pattern is placed in a sand mixture, which is then compacted around it to form a mold. When the pattern is removed, it leaves a cavity that is shaped exactly like the original pattern.
The success of the sand casting process largely hinges on the properties of the sand used. Silica sand is the most common choice due to its refractory properties, allowing it to withstand high temperatures without deforming. To improve the binding ability of the sand, additives such as clay or resin may be used. The result is a mold capable of enduring the stresses of molten metal being poured into it.
The Sand Casting Process
The sand casting process can be broken down into several key steps
1. Pattern Making The first step involves constructing a pattern, often made of wood, metal, or plastic. The pattern includes allowances for shrinkage and draft angles to facilitate easy removal from the mold.
2. Mold Formation The pattern is placed in a flask, a container used to hold the sand mixture. The sand is then packed around the pattern, which is typically done in two halves to create a mold.
sand cast
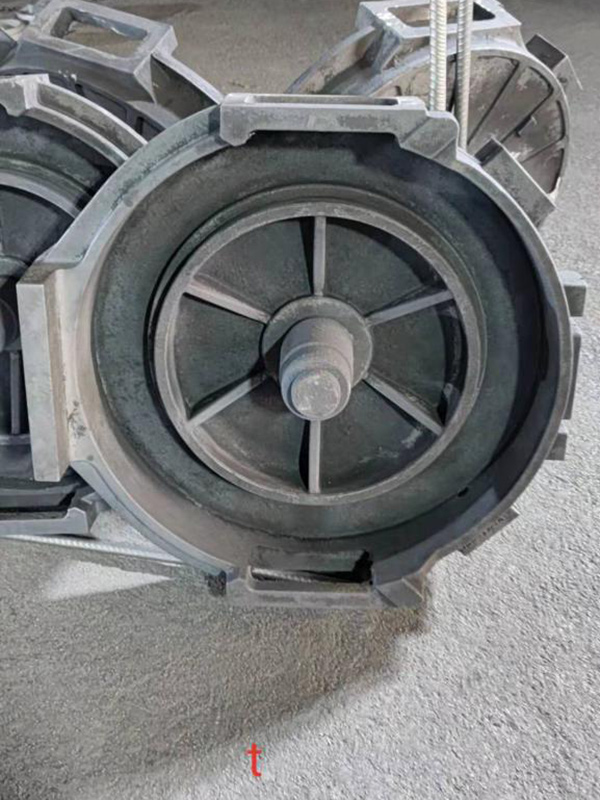
3. Pouring Once the mold is prepared, it is assembled and molten metal is poured into the cavity. The temperature of the molten metal can reach thousands of degrees, making this step crucial for the quality of the final product.
4. Cooling The metal is left to cool and solidify within the mold. This process can take several minutes to hours, depending on the material and the dimensions of the cast item.
5. Mold Removal After the metal has cooled, the mold is broken apart to reveal the cast piece. This is often followed by a cleaning process to remove any sand residues.
6. Finishing The final piece may need further processing, such as machining, painting, or plating, to achieve the desired surface finish and specifications.
Advantages of Sand Casting
One of the main advantages of sand casting is its ability to produce complex and heavy shapes that would be difficult, if not impossible, to manufacture using other methods. Additionally, the materials used in sand casting are relatively inexpensive, making it an economical choice for both small and large production runs. The reusability of sand also contributes to its cost-effectiveness.
Furthermore, sand casting can accommodate a wide range of metals and alloys, including aluminum, iron, and bronze. This versatility makes it a popular choice for various applications, from engine blocks to decorative items.
Conclusion
In summary, sand casting is a time-honored method that bridges the gap between artistic creativity and engineering precision. Its applications span numerous sectors, illustrating its enduring relevance in today’s manufacturing landscape. Whether producing a single prototype or large quantities of components, sand casting remains a fundamental technique in the metalworking world, showcasing the perfect blend of tradition and innovation. As technology continues to advance, the techniques and materials used in sand casting are likely to evolve, promising an exciting future for this ancient art form.
Post time:Oct . 13, 2024 06:58
Next:Quality Foundry Sand Solutions for Optimal Casting Performance and Efficiency