What is the Sand Casting Process?
Sand casting is one of the oldest and most widely used metal casting processes. This method involves creating a mold from sand and then pouring molten metal into that mold to create a desired shape. The versatility, cost-effectiveness, and simplicity of sand casting make it a popular choice for producing metal parts in a variety of industries, including automotive, aerospace, and manufacturing.
The Sand Casting Process
The sand casting process generally consists of several key steps
1. Pattern Making The first step involves creating a pattern, which is a replica of the object to be cast. Patterns can be made from various materials, such as wood, metal, or plastic. They are typically slightly larger than the final product to account for material shrinkage during cooling.
2. Mold Preparation Once the pattern is ready, a mold is created by packing sand around it. The sand used is usually bonded with clay and moisture to hold its shape. After the pattern is placed in the sand, the sand is tightly packed around it, and the two halves of the mold are assembled. The pattern is then removed, leaving a cavity in the shape of the object to be cast.
3. Pouring The next step involves heating metal to its melting point and pouring it into the mold cavity. The molten metal fills the cavity, taking the shape of the pattern. It is crucial to control the temperature and pouring speed to minimize defects.
4. Cooling After pouring, the metal needs time to cool and solidify. The duration of this stage depends on the size and thickness of the casting. Once cooled, the mold is broken away to reveal the solidified metal cast.
what is sand casting process
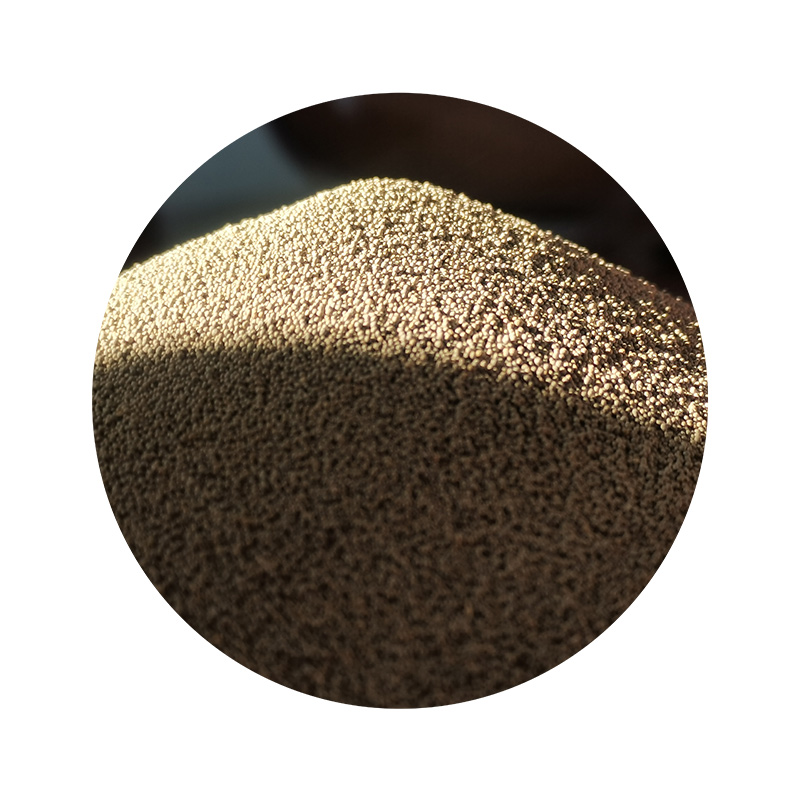
5. Finishing After the casting is removed from the mold, it often requires finishing processes to achieve the desired surface quality and dimensions. This can include grinding, sanding, machining, or painting.
Advantages of Sand Casting
One of the primary advantages of sand casting is its flexibility in producing various shapes and sizes. It can accommodate both large and small parts with complex geometries, which may be challenging for other casting processes. Additionally, sand casting allows for the use of a wide range of metals, including aluminum, iron, steel, and bronze.
Another significant benefit is cost-effectiveness. The materials used in sand casting are relatively inexpensive, and the process itself can be executed with straightforward equipment. This makes it an attractive option for both small-scale production and large-volume manufacturing.
Limitations of Sand Casting
Despite its advantages, sand casting does have limitations. The surface finish of sand-cast products is generally not as smooth as those produced by other methods, such as investment casting. Moreover, there can be issues with accuracy and tolerances, especially for intricate designs. Finally, the process can be slower compared to some modern automated casting techniques.
In conclusion, the sand casting process is a fundamental method in the field of metalworking. Its ability to produce a wide variety of shapes and sizes at a low cost has ensured its continued relevance in modern manufacturing, even as new technologies emerge. Whether for prototyping or mass production, sand casting remains an essential option worth considering.
Post time:नवम्बर . 02, 2024 03:27
Next:sintered sand