Types of Sand Used in Sand Casting
Sand casting is a widely used manufacturing process that involves pouring molten metal into a mold made of sand. The quality and characteristics of the final product greatly depend on the type of sand utilized in this process. There are several types of sand commonly employed in sand casting, each with its own unique properties and suitability for various applications.
One of the most popular types of sand used in sand casting is silica sand. This natural mineral is composed mainly of silicon dioxide and is known for its high melting point, excellent thermal conductivity, and strength. Silica sand is often used as a base material due to its availability and cost-effectiveness. However, the grain size and shape of silica sand can vary, influencing the surface finish and dimensional accuracy of the casted parts.
Another type of sand frequently used is olivine sand, which is composed of magnesium iron silicate. Olivine sand is favored for its low expansion rate and high resistance to thermal shock, making it suitable for casting metals that require high-temperature processing. This type of sand also provides a better finish on the cast surface compared to silica sand, although it is generally more expensive.
types of sand used in sand casting
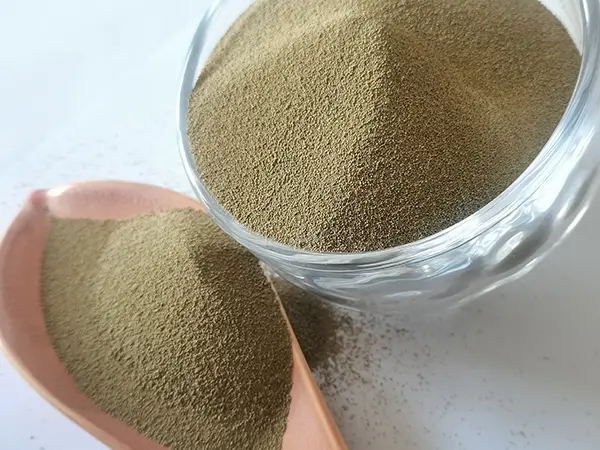
In addition to silica and olivine sands, there is also zircon sand, known for its high melting point and excellent resistance to chemical reactions. Zircon sand is often used for casting high-alloy steels and non-ferrous metals due to its durability and ability to maintain its shape under high temperatures. However, its cost can be a limiting factor for some applications.
Resin-coated sands are also gaining popularity in the casting industry. These sands are coated with a thermosetting resin that enhances their bonding properties, enabling them to withstand higher temperatures without degrading. This type of sand allows for greater dimensional accuracy and surface finish, making it ideal for intricate designs and high-quality parts. However, the cost of resin-coated sands can be significantly higher than traditional sand options.
Lastly, there is also synthetic sand, which is engineered to achieve specific properties such as improved flowability, moisture retention, and reduced dust generation. Synthetic sands can be tailored to meet the needs of particular casting processes and are increasingly being used in modern foundries for their versatility and performance benefits.
In conclusion, the type of sand used in sand casting plays a crucial role in determining the quality of the final product. Each type of sand—whether it is silica, olivine, zircon, resin-coated, or synthetic—offers distinct advantages that cater to different manufacturing requirements. Understanding these differences allows manufacturers to choose the most appropriate sand for their specific casting needs, ensuring better performance and higher quality in the finished components.
Post time:अक्टूबर . 06, 2024 15:33
Next:3d printing sanding