Sand Used in Foundry An Essential Component in Metal Casting
Sand plays a critical role in the foundry industry, serving as a primary material for molding and core making in the metal casting process. Its importance can be attributed to several factors, including its availability, cost-effectiveness, and ideal physical properties. This article delves into the various types of sand used in foundries, their characteristics, and the implications of their use in metal casting.
Types of Sand
The most commonly used sand in foundries is silica sand, due to its high silicon dioxide content. Silica sand is preferred for its excellent thermal stability, which helps withstand the intense heat generated during metal casting. In addition to silica sand, other types of sand are also utilized, including olivine sand, chromite sand, and zircon sand, each possessing unique properties suited for specific applications.
1. Silica Sand This is the most prevalent type of sand in foundry applications. Its grain shape and size can be easily manipulated, allowing for a customized mold surface finish. Moreover, silica sand is abundant and relatively inexpensive, making it economically viable for large-scale operations.
2. Olivine Sand Known for its high melting point and thermal stability, olivine sand is often used in the casting of ferrous alloys. Its unique composition minimizes the potential for metal penetration, leading to cleaner castings.
3. Chromite Sand This type of sand possesses a high degree of heat resistance and is particularly suitable for casting steel and iron. Chromite sand enhances the strength of molds and cores, improving casting quality and reducing defects.
4. Zircon Sand Zircon sand is valued for its high thermal stability and low thermal expansion, making it ideal for precision casting and applications requiring fine details. Its high melting point helps in achieving superior surface finishes.
Properties of Foundry Sand
sand used in foundry
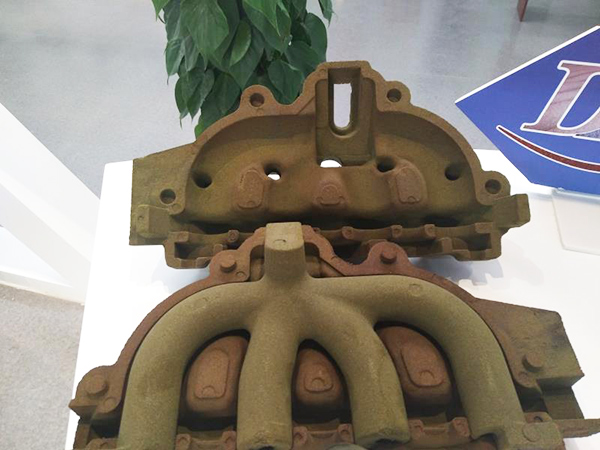
The effectiveness of sand in foundry applications can be attributed to several key properties
- Grain Size and Shape The size and shape of the sand grains affect the mold’s permeability and strength. Finer grains provide a smoother surface finish, while coarser grains enhance strength and reduce gas retention.
- Porosity A good mold sand must have an optimal balance of porosity to allow gases generated during metal pouring to escape without damaging the mold or affecting the quality of the casting.
- Thermal Conductivity The ability of the sand to dissipate heat affects the cooling rate of the metal cast, impacting the final properties of the casting. Sands with high thermal conductivity can help achieve uniform cooling.
- Reusability One of the advantages of sand used in foundry processes is its reusability. After a casting cycle, the sand can be reclaimed, cleaned, and reused for future molding, making it a sustainable choice.
Implications for the Metal Casting Industry
The choice of sand in foundry operations not only influences the quality of the finished product but also affects production efficiency and costs. High-quality sands can improve mold strength, reduce scrap rates, and enhance overall productivity. Furthermore, advancements in sand reclamation technologies enable foundries to minimize waste and reduce the environmental impact of their operations.
In conclusion, the role of sand in foundry applications is indispensable. Its unique properties and adaptability to different casting processes highlight its significance in the metal casting industry. As the demand for high-quality castings continues to rise, the exploration of new sand types and reclamation methods will play a pivotal role in shaping the future of foundry practices, ensuring sustainability and efficiency in metal casting.
Post time:दिसम्बर . 17, 2024 06:15
Next:foundry sand in concrete