Understanding Sand Casting Technology A Comprehensive Overview
Sand casting, also known as sand mold casting, is a metal casting process characterized by the use of sand as the primary molding material. This technology has been a cornerstone of manufacturing for centuries, enabling the production of a vast range of metal components used in various industries, from automotive to aerospace. In this article, we will explore the fundamentals of sand casting technology, its advantages, challenges, and future trends in the context of modern manufacturing.
Process of Sand Casting
The sand casting process begins with the creation of a mold. This involves two key components the pattern and the sand mixture. The pattern is a replica of the desired object, typically made from metal, plastic, or wood. Once the pattern is prepared, it is placed in a molding box, where a mixture of sand (often silica sand), clay, and water is packed around it. The clay acts as a binding agent to hold the sand grains together.
After the sand is compacted around the pattern, the molding box is separated to remove the pattern, leaving a cavity in the shape of the desired part. The two halves of the mold are then reassembled, and molten metal is poured into the cavity through a pouring cup, along with gating systems that channel the metal into the mold. Once the metal cools and solidifies, the sand mold is broken away to reveal the finished casting.
Advantages of Sand Casting
One of the most significant advantages of sand casting is its versatility. The process can accommodate a wide range of metal alloys, including aluminum, iron, copper, and magnesium, making it suitable for various applications. Additionally, the ability to produce large castings and intricate designs makes sand casting an attractive option for manufacturers.
Another advantage is the relatively low cost of materials and equipment. Sand is abundant and inexpensive, while the tooling required for sand casting, such as the patterns and molds, can be produced at a lower cost compared to other casting methods. This cost-effectiveness makes sand casting an ideal choice for low to medium production volumes.
Moreover, the sand casting process allows for excellent flexibility in part design. Complex shapes can be produced with different features, such as internal cavities, undercuts, and intricate surface details. This flexibility not only helps meet specific design requirements but also enables rapid prototyping and modification of parts.
sand casting technology
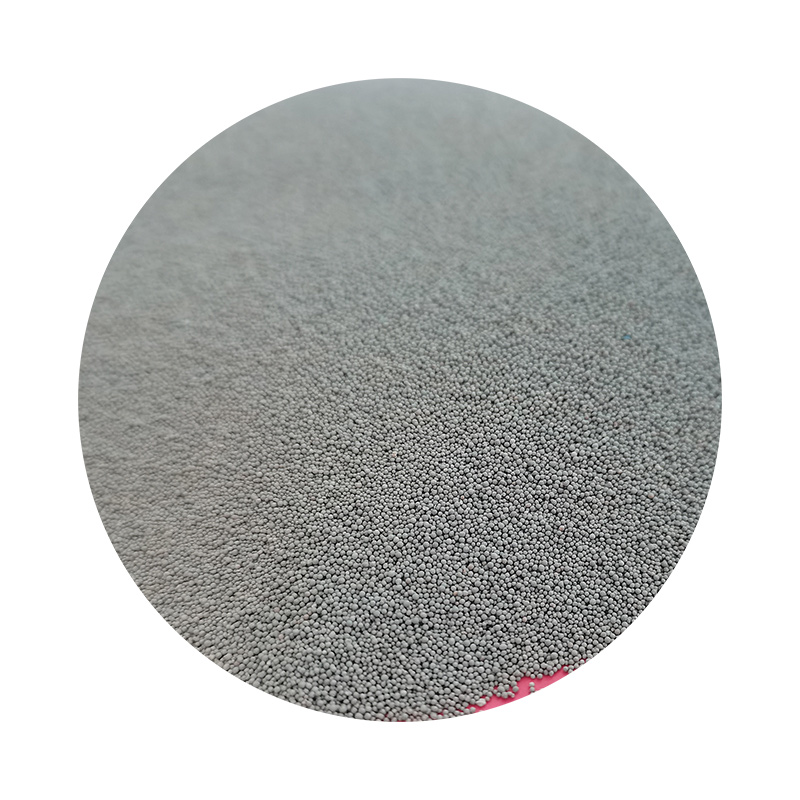
Challenges in Sand Casting
Despite its many advantages, sand casting is not without its challenges. One of the primary issues faced by manufacturers is the potential for defects in the castings, such as sand inclusion, porosity, and misalignment. These defects can arise from various factors, including improper mold preparation, insufficient ventilation, or inadequate pouring techniques.
Another challenge is the labor-intensive nature of the process. While advancements in automation have improved efficiency, many sand casting operations still rely heavily on manual labor, which can lead to variability in product quality. Additionally, the presence of sand particles can lead to environmental concerns, as dust generated during the casting process can have negative health effects on workers and environmental impacts if not managed properly.
Future Trends in Sand Casting
Looking ahead, the future of sand casting technology appears promising. Innovations in materials science and engineering are leading to improved sand mixtures that enhance the mold's stability and durability. Additionally, advancements in simulation software are helping manufacturers predict and address potential casting defects before production begins, thus reducing waste and improving quality.
The integration of Industry 4.0 technologies, such as the Internet of Things (IoT) and data analytics, is also paving the way for smarter sand casting operations. By monitoring and analyzing production processes in real-time, manufacturers can optimize their operations, increase efficiency, and reduce defects.
Furthermore, as sustainability becomes increasingly important in manufacturing, efforts to recycle sand and reduce waste in sand casting processes are gaining traction. Developing eco-friendly binders and exploring alternative materials can significantly lower the environmental impact of sand casting.
Conclusion
In conclusion, sand casting technology remains a vital component of modern manufacturing. Its versatility, cost-effectiveness, and ability to produce intricate designs make it an essential method for creating metal components across various industries. While challenges such as defects and labor intensity persist, ongoing innovations and advancements present a bright future for sand casting, promising to enhance its efficiency, sustainability, and overall effectiveness in meeting the demands of contemporary manufacturing.
Post time:नवम्बर . 12, 2024 09:22
Next:resin bonded sand casting