The Importance of Sand in Sand Casting
Sand casting, one of the oldest and most versatile manufacturing processes, relies heavily on the properties and characteristics of sand. As a cornerstone of foundry practices, sand determines the quality of the final product, its production efficiency, and overall castability. In this article, we will explore the composition of sand, its various types, and its crucial role in the sand casting process.
Composition of Sand
The primary component in sand casting is, unsurprisingly, sand itself. Typically, the sand used in this process is silica sand, primarily composed of silicon dioxide (SiO2). This highly abundant material is favored for its excellent heat resistance, durability, and ability to form a mold that accurately captures the desired details of the casting.
In addition to silica, sand may be mixed with other materials to improve its properties. For example, clay is often added to enhance the binding capability, allowing the sand particles to adhere better, which is essential for maintaining mold integrity during the pouring of the molten metal. Other additives, such as water, can help reduce dust and improve the flexibility of the mold.
Types of Sand Used in Sand Casting
There are various types of sand used in the sand casting process, each with unique properties and advantages. The most common types include
1. Green Sand This is a mixture of silica sand, clay, and water. It is called green not because of its color, but because it is used in a moist state. Green sand is favored due to its excellent molding properties, ability to hold intricate detail, and ease of reclamation after use.
2. Dry Sand Unlike green sand, dry sand is baked to remove moisture. This type of sand is typically used for heavy castings, as it is more durable and can withstand higher temperatures during the casting process.
sand casting sand
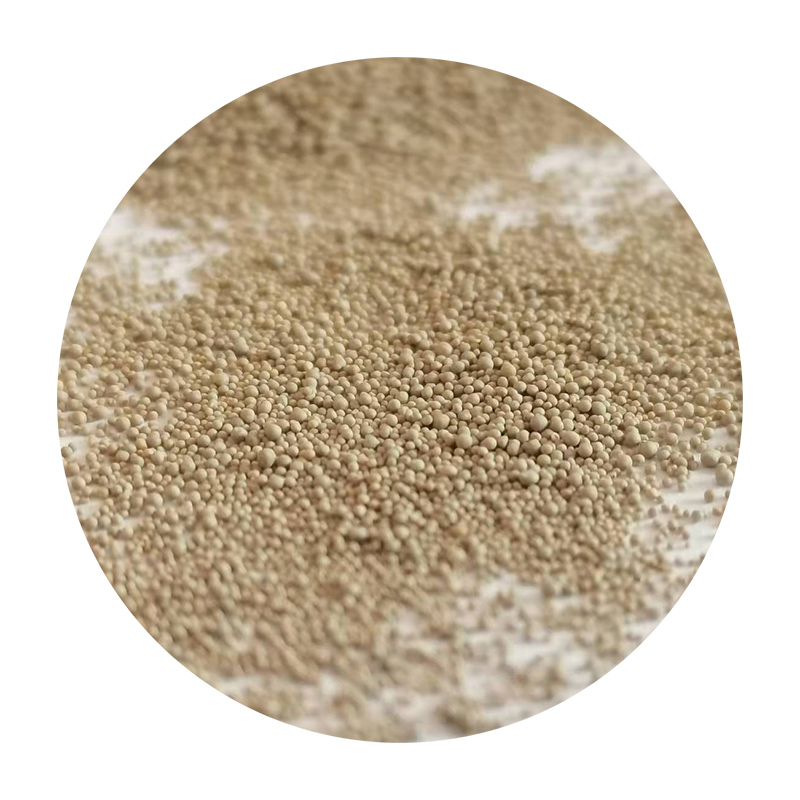
3. Resin Sand This type involves binding sand with resin, which provides superior strength and heat resistance. Resin sand molds can achieve finer details, making them ideal for precision castings, although they can be more expensive and less environmentally friendly.
4. Carbon Dioxide Sand Also known as CO2 sand, it is created by mixing different types of sand with a curative solution and then exposing it to carbon dioxide gas. This process hardens the sand quickly and is often used for producing complex shapes.
Role of Sand in the Sand Casting Process
The sand plays a pivotal role throughout the sand casting process. Initially, the sand is packed around a pattern to create a mold. The ability of the sand to maintain its shape and accurately capture the details of the pattern is critical. Properly prepared sand has the ideal grain size, moisture content, and mixture of additives, which together ensure optimal mold strength and thermal stability.
Once the mold is created, molten metal is poured into the cavity. Here, the sand's refractory properties are crucial; it must withstand the intense heat without undergoing significant thermal degradation. Additionally, good sand should allow the release of gases generated during solidification, minimizing the risk of defects such as blowholes in the final casting.
After the metal has cooled and solidified, the mold is broken away, and the sand is reclaimed for reuse. The efficiency of sand reclamation is another benefit, making sand casting a cost-effective and sustainable manufacturing method.
Conclusion
In summary, sand is not merely a component of the sand casting process; it is a vital material that influences the entire manufacturing workflow. The specific type of sand chosen, along with its properties and preparation, can greatly affect the quality of the casted product. As industries continue to innovate and seek more efficient and sustainable practices, the role of sand in sand casting remains significant, highlighting its importance in modern metallurgy and manufacturing. Understanding the various aspects of sand can lead to improvements in casting techniques, yielding better products and reducing costs, maintaining sand casting’s relevance in contemporary industry.
Post time:नवम्बर . 08, 2024 08:44
Next:Analyzing the Composition of Foundry Sand for Optimal Casting Performance