Understanding Sand Casting Processes
Sand casting, one of the oldest and most versatile manufacturing processes, is widely utilized in various industries for producing metal parts. This method involves creating a mold from sand, which allows for the intricate shaping of molten metal. Due to its flexibility, sand casting is an ideal choice for both small-scale operations and large-scale production.
Understanding Sand Casting Processes
Next, the molten metal is poured into the mold. This metal is usually heated to extremely high temperatures until it reaches a liquid state. Once the pouring is completed, the metal begins to cool and solidify, taking on the shape of the mold cavity. The cooling time can vary based on the metal type and the thickness of the casting.
sand casting processes
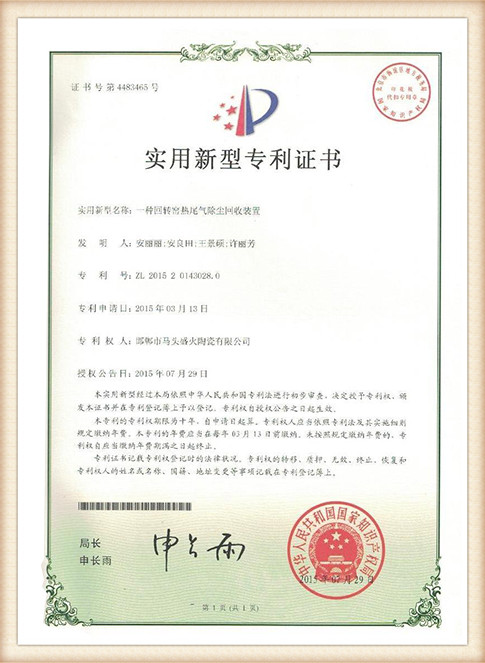
After the metal solidifies, the mold is broken away to reveal the cast part. The sand is often recycled for future use, making sand casting an environmentally friendly option. However, some secondary processes may be required to achieve the final finish of the cast part, such as machining, grinding, or polishing to remove imperfections.
One of the advantages of sand casting is its ability to produce complex shapes that would be difficult or impossible to achieve with other methods. It accommodates a wide variety of metals, including iron, aluminum, and bronze, enhancing its versatility. Furthermore, the process is suitable for both small and large production runs, making it economical for various applications.
However, sand casting does have its drawbacks, such as lower dimensional accuracy and surface finish compared to more advanced methods like investment casting. Despite these limitations, its cost-effectiveness, accessibility, and adaptability ensure that sand casting continues to be a popular choice in many manufacturing sectors worldwide. This enduring relevance speaks to the process's significance in producing custom metal parts that meet diverse industry needs.
Post time:नवम्बर . 14, 2024 15:25
Next:lost foam castings